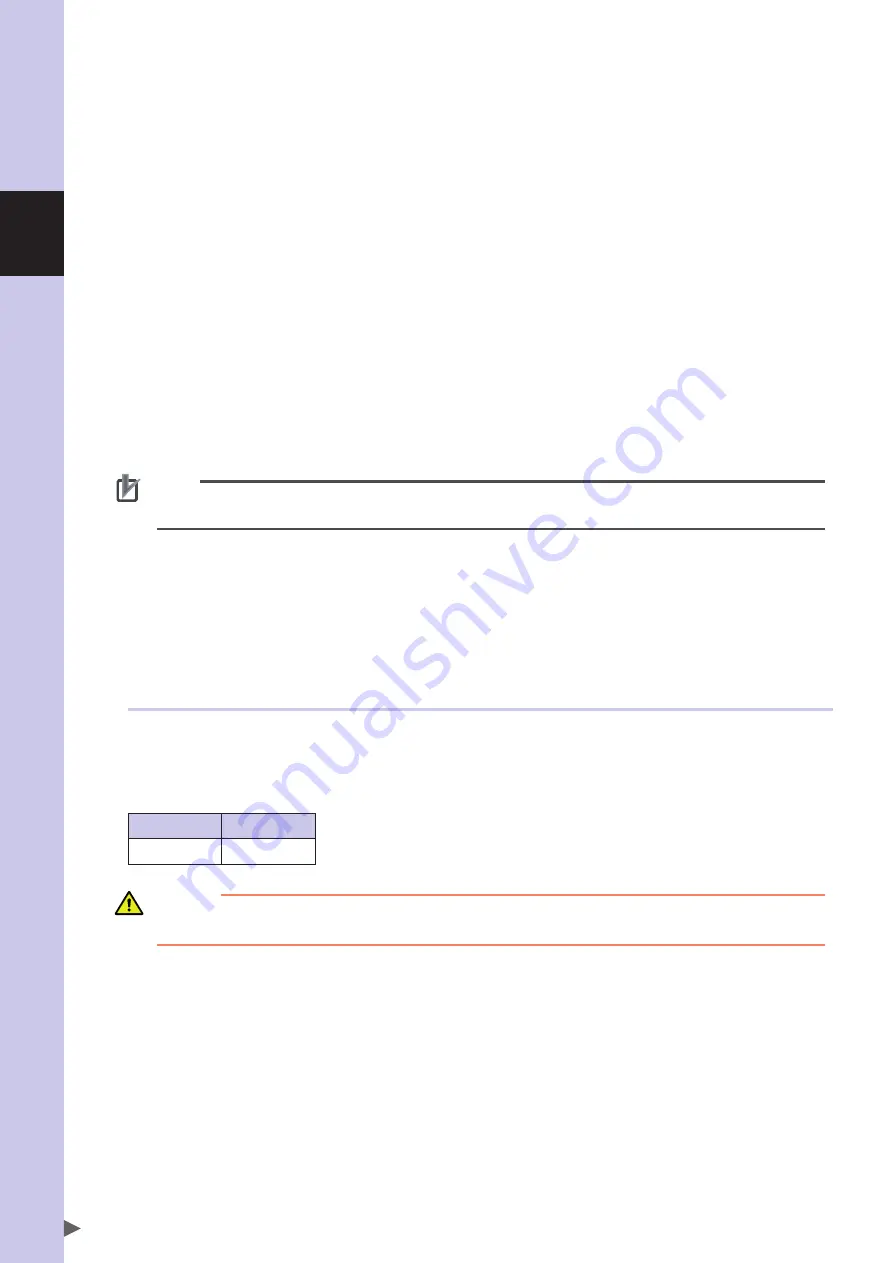
2
Installa
tion
2-72
5
Install the additional stopper.
Install the additional stopper (1) to the ball screw by tightening the bolts (3) to the specified torque shown below.
• Tightening torque: 4.5 nm (46 kgfcm)
Alternately tighten the bolts a little at a time.
The stopper position in the plus direction L
1
must be 4mm or more.
6
Secure the urethane damper.
Widen the notch part of the urethane damper (2), pass it through the ball screw shaft, and bond it onto the additional stopper
(1) in the Z-axis plus direction using adhesive. Use Threebond 1739 instant adhesive as the adhesive. Fully degrease the
bonding surfaces before applying the adhesive.
7
Go out of the safety enclosure.
8
Turn on the controller.
Check that no one is inside the safety enclosure, and then turn on the controller.
9
Set the soft limits.
Set the soft limits in the plus direction while referring to the calculation values shown in the Table "
n
Soft limits after
installing additional stoppers" described previously.
10
Check that Z-axis stops firmly.
Whether or not the Z-axis stops at a position before the stopper by the soft limit must be checked from the outside of the
safety enclosure.
NOTE
The Z-axis may not stop at a position before the stopper due to the stopper part accuracy or position. If this happens, decrease the value
while referring to the Table "
n
Soft limits after installing additional stoppers" described previously.
11
Check that the movement range is limited.
12
Turn off the controller.
13
Enter the safety enclosure.
14
Reattach the Y-axis arm cover.
8.1.3 Overrun amounts during impacts with Z-axis additional mechanical stopper
A urethane damper is installed to absorb the shock when an impact occurs with the mechanical stopper, so a certain
amount of overrun occurs when the robot strikes the mechanical stopper. Use caution and take overrun into account
since the end effector may interfere with the robot body and peripheral equipment or the robot body may interfere with
the peripheral equipment. maximum overrun amounts are listed below (for normal operation, maximum payload,
maximum speed).
Upper end
Lower end
1mm
1mm
CAUTION
After the robot strikes the Z-axis mechanical stopper, the stopper position may shift, and so check the stopper position. If shifted, move
the stopper to the correct position and refasten it securely by following the assembly procedure.
Содержание R6YXG500
Страница 1: ...ZX T Series Cat No I155E EN 03A R6Y XG series INSTALLATION MANUAL SCARA Robots XG Series...
Страница 2: ......
Страница 10: ......
Страница 36: ......
Страница 38: ......
Страница 39: ...Contents Before using the robot Be sure to read the following notes i Introduction v Introduction...
Страница 40: ......
Страница 46: ......
Страница 48: ......
Страница 56: ......
Страница 169: ...2 Installation 2 111 Installing the extension shaft Extension shaft 1 Upper nut Bolt 2 6 Go out of the safety enclosure...
Страница 174: ......
Страница 176: ......
Страница 220: ......
Страница 221: ...Chapter 4 Periodic inspection Contents 1 Overview 4 1 2 List of inspection items 4 2...
Страница 222: ......
Страница 226: ......
Страница 227: ...Chapter 5 Harmonic drive replacement period Contents 1 Overview 5 1 2 Replacement period 5 2...
Страница 228: ......
Страница 232: ......
Страница 238: ......
Страница 239: ...Chapter 7 Torque limit designated Z axis pushing action Contents 1 Torque limit designated Z axis pushing action 7 1...
Страница 240: ......
Страница 244: ......
Страница 246: ......
Страница 323: ...8 Specifications 8 77 1 3 Robot inner wiring diagram Robot inner wiring diagram R6YXG500...
Страница 330: ...Cat No I155E EN 03A Note Specifications subject to change without notice Authorized Distributor Printed in Europe...