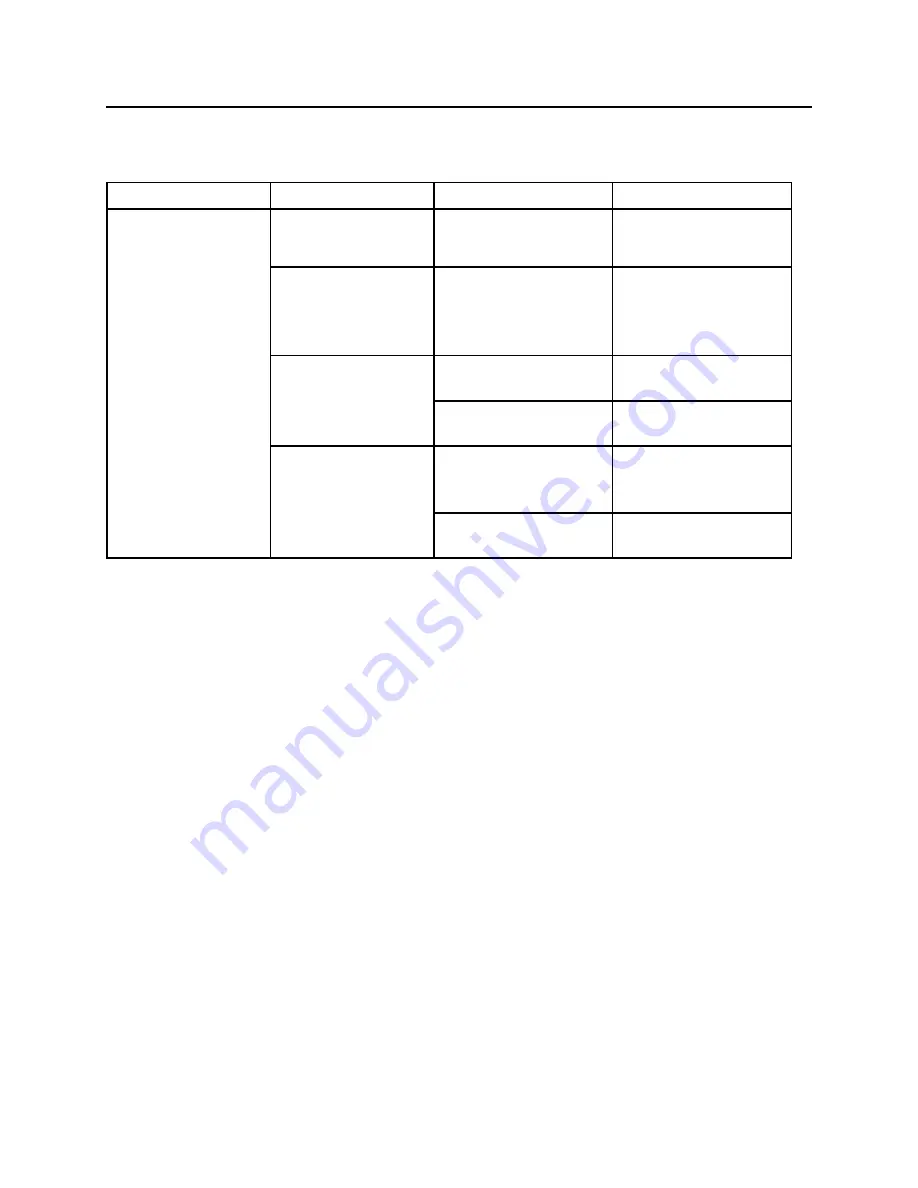
-
101
-
TROUBLESHOOTING
INTENSIFIER CHECKS
(unit clicks – does not slow down)
INTENSIFIER CHECKS
PROBLEM
CAUSE
CHECK
REMEDY
Intensifier clicks but
does not slow down
M35 Processor
relief valves
Check relief
cartridges for
tightness.
Tighten the relief
valve cartridges.
Pilot check valve
assemblies.
Inspect the booster
inlet pilot check valve
assemblies for
damaged seats.
Replace the inlet pilot
check valve
assemblies.
Booster assembly
Check poppets and
seats.
Replace poppets and
seats as necessary.
Check all o-rings and
backup rings.
Replace all o-rings
and backup rings.
Main cylinder
assemblies
Check main cylinder
piston rings for by-
passing oil.
Replace piston rings.
Check for damaged
seals.
Reseal cylinders
Содержание M35G
Страница 13: ... 13 SERIAL NUMBER LOCATION M35 ...
Страница 115: ... 115 WARRANTY STATEMENTS ...
Страница 116: ... 116 WARRANTY STATEMENTS ...
Страница 118: ... Copyright 2018 NPK Construction Equipment Inc www npkce com M000 9601B M35 Material Processor Instruction Manual 10 18 ...