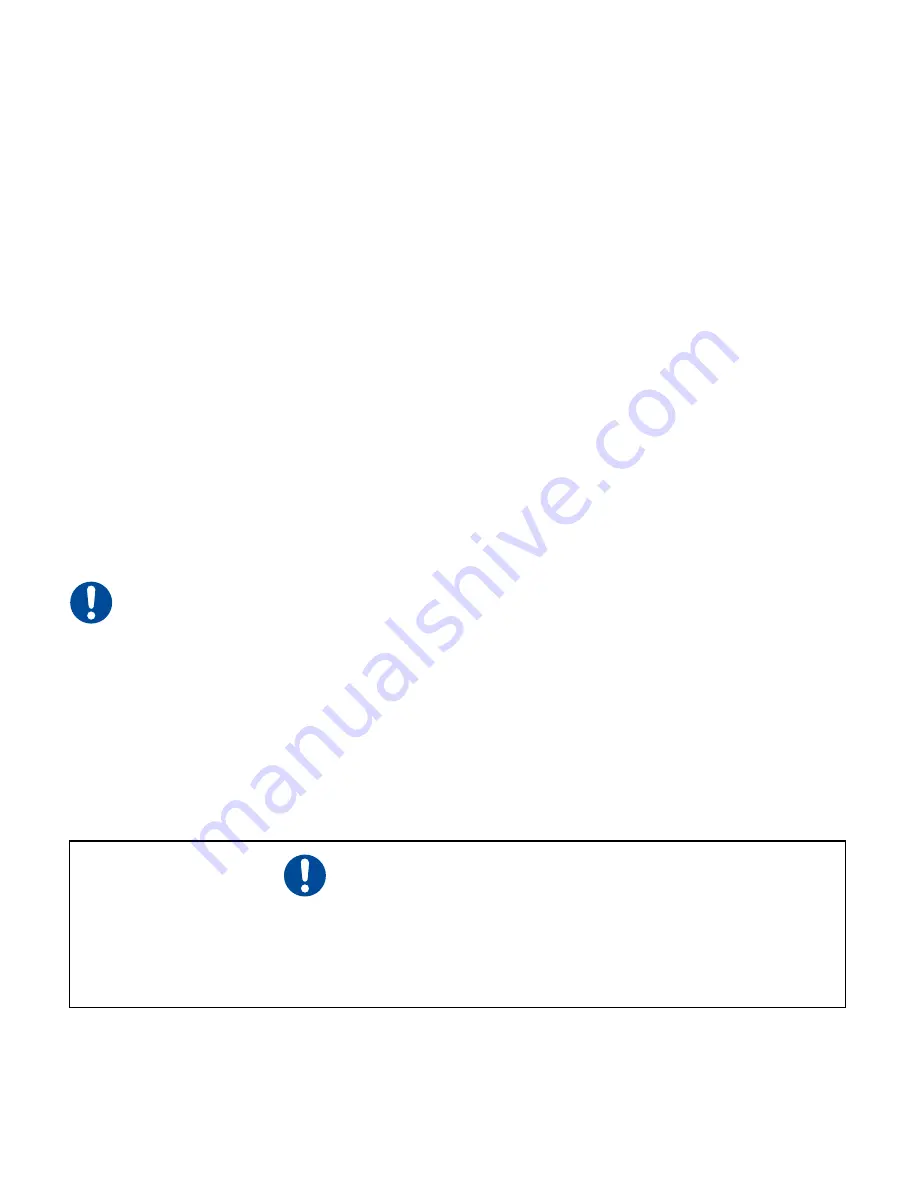
BEAM DELIVERY OPTICS
PAGE
|
45
Optical setup
After selecting a laser for a CO2 laser processing system, the two most important elements to consider
are: (1) beam delivery optics to transmit the beam to the work area; and (2) focusing optics to focus the
beam onto the part or material to be processed. Each element is crucial in the development of a reliable
laser-based material processing system and each element should be approached with the same careful
attention to detail.
Beam delivery optics
Divergence, or expansion, of the laser beam is important in materials processing since a larger beam
entering the focusing optic produces a smaller focused spot. Because the v30 laser beam diverges by 7
mm over each meter of distance traveled, the laser should be mounted 1.0–1.5 m (40–60 in) away from
the work area and no closer than 0.75 m (30 in) for optimum performance. Right angle turning mirrors
(beam benders) are often used in conjunction with the laser mounting position to obtain this distance.
Expander/collimators are optical devices that increase beam diameter by a selectable magnification
factor while reducing beam divergence at the same time. Adding an expander/collimator substantially
reduces beam divergence and any variance in beam diameter caused by the changing optical path
length in an XY (“flying optics”) table application. In fixed-length delivery systems where the laser is
positioned only one meter away from the focusing optic and a small spot size is required, an
expander/collimator is again the best solution to provide the required beam expansion before reaching
the focusing optic.
Important Note:
Optical components in the beam path must always be aligned to the actual
beam path, not the laser faceplate. Because of slight variations in laser construction, the beam
path may not always be centered in, or perpendicular to, the aperture in the faceplate.
Focusing optics
When selecting a focusing optic, the primary consideration should be material thickness and any vertical
tolerances that occur during final part positioning rather than selecting based only on minimum spot
size. The chosen focal length should create the smallest possible focused spot while providing the depth
of field required for the material to be processed.
Caution: Possible Equipment Damage
Any contaminants on the laser’s output window (or on any optic in the beam path) can absorb
enough energy to damage the optic. Inspect all beam delivery optics periodically for signs of
contaminants and carefully clean as required. In dirty environments, purge laser optics using filtered
air or nitrogen to prevent vapor and debris from accumulating on optical surfaces.
Содержание v30
Страница 1: ...ENGINEERED BY SYNRAD v30 Laser User Manual...
Страница 16: ...OEM V30 LASER LABEL LOCATIONS PAGE 16 OEM v30 Laser label locations...
Страница 22: ...DECLARATION OF CONFORMITY PAGE 22 Declaration of conformity Figure 2 Declaration Document...
Страница 64: ...INTERFACE CONNECTIONS PAGE 64 Figure 3 16 Laser OK output to PLC input...
Страница 90: ...BEAM DELIVERY OPTICS PAGE 90 This page is left blank intentionally...
Страница 100: ...INDEX PAGE 1 This page is intentionally left blank...