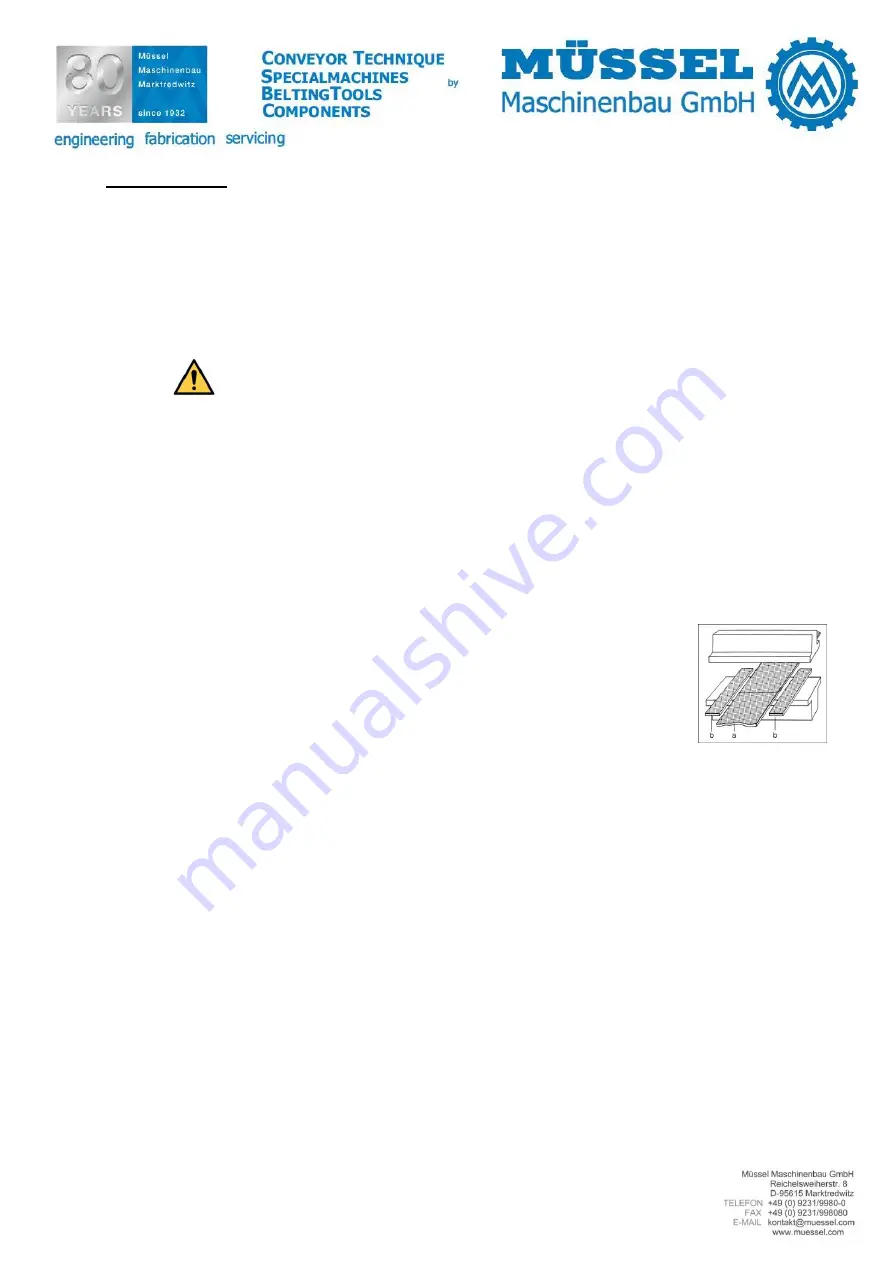
Operating instruction: O003 / 5759
Edition: 04/2019
Reproduction, duplication of this document - even a partial form –
are subject to our permission. All rights reserved.
In this data sheet any liability for changes, errors or misprints is excluded.
16
5
Handling
5.1
General
Heating presses are electrical heating devices for use in fabricating (splicing) belting material that
can withstand maximum temperatures of 210°C.
Note:
When making melting splices always observe the splicing instructions for the belt type to be spliced.
Attention
Before every heating process check the heating press for signs of damage.
5.2
Inserting the belt into the heating press
1. Prepare both belt ends according to the required splice (Z-splice).
2. Cover the bottom part of the press according to the splicing instruction for the respective belt
type to the full heating surface and fold it out with respective material to the full width.
3. Both belt ends must be centrically placed on the covered bottom part (with the operating side
reversed).
4. Place material of the same thickness to the left and right next to the
ends of the belt (refer to the following figure).
Note:
Always fold out the areas to be pressed to the full width. If the belting
material is a) narrower than the area to be pressed, (so that the press
does not deflect) – b) belting remnants in the same thickness of the
same material must be additionally inserted. Please only insert the
same material and don’t insert others (like shim bars, etc.)!
5. Please entirely push together and mark the Z-splice as per specification of the belt producer.
6. Place the top hold-down bar and tighten it slightly on both sides.
7. Centre and align the belt.
8. Tighten the top hold-down bar on both sides!
9. If necessary etc., cover the splice with additional material (PVC-Z-foil, PU-Z-foil) (Fig. 3).
10. Depending on the belt type, place the prescribed covering material (silicone embossing mat,
separating paper, textured fabric fine etc.) over the full heating surface to the full width.
11. Place the top part of the press with pressure hose. The centering pin of the bottom beam has
to be inserted in the centering bore of the top beam.
Please note to cover the full width with respective material to gain an optimal tempera-
ture distribution and an optimal pressure.