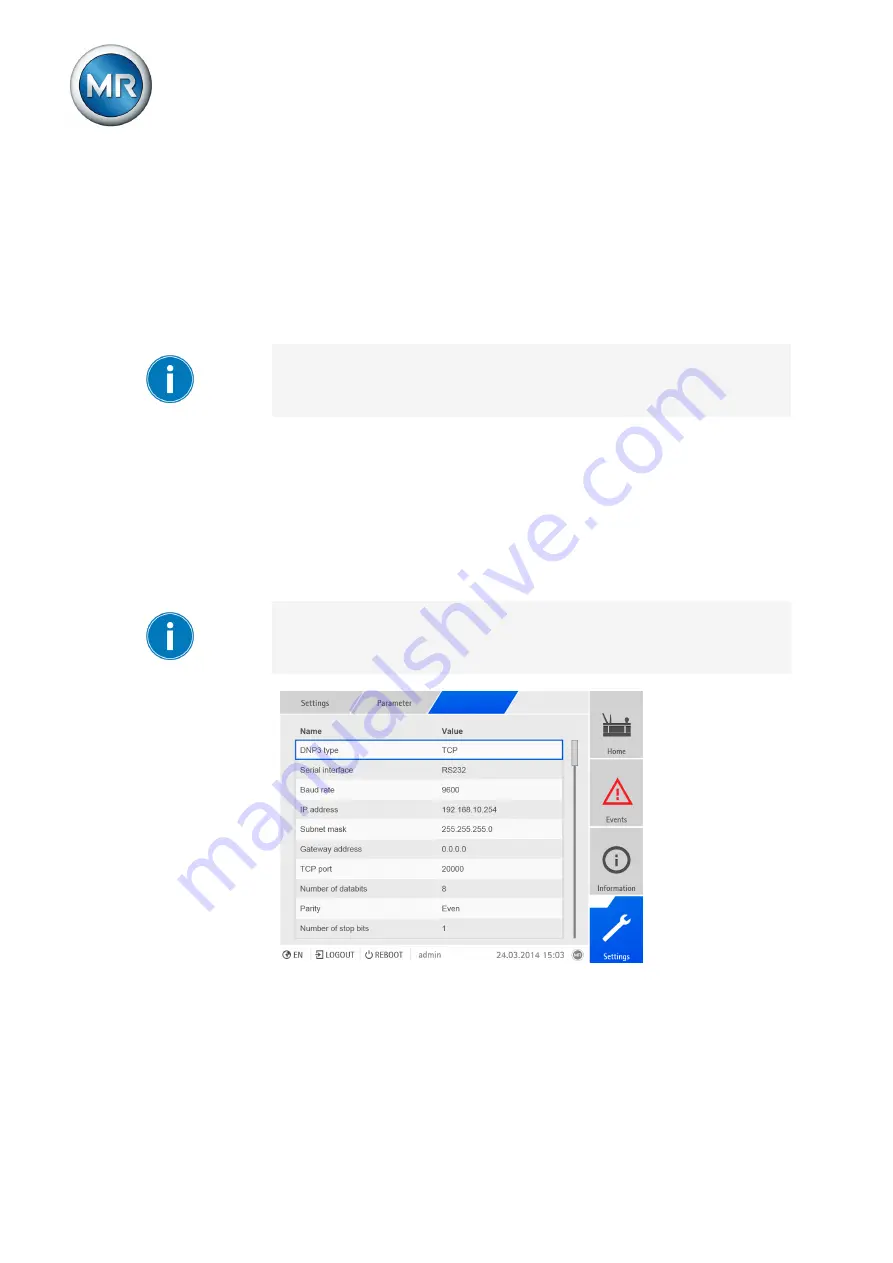
8 Operation
Maschinenfabrik Reinhausen GmbH 2018
126
5252433/02 EN
ECOTAP
®
VPD
®
CONTROL PRO
To activate/deactivate the "TCP Keepalive" function, proceed as follows:
1. Go to
Settings > Parameters > Modbus > TCP Keepalive
.
2. Select the desired option.
3. Press the
Accept
button to save the modified parameter.
IP address
You can use this parameter to assign an IP address to the device.
Assign IP addresses to both web-based visualization and SCADA (optional)
in different subnets. Otherwise you will not be able to establish a connec-
tion.
1. Go to
Settings > Parameters > Modbus > IP address
.
2. Enter the IP address.
3. Press the
Accept
button to save the modified parameter.
8.11.5 Configuring DNP3 (optional)
If you would like to use the DNP3 control system protocol, you must set the
parameters listed below.
The device only supports DNP3 TCP.
Figure 82: Setting parameters for DNP3
IP address
You can use this parameter to assign an IP address to the device.
Содержание ECOTAP VPD CONTROL PRO
Страница 1: ...Voltage Regulator ECOTAP VPD CONTROL PRO Operating Instructions 5252433 02 EN ...
Страница 190: ......
Страница 191: ......