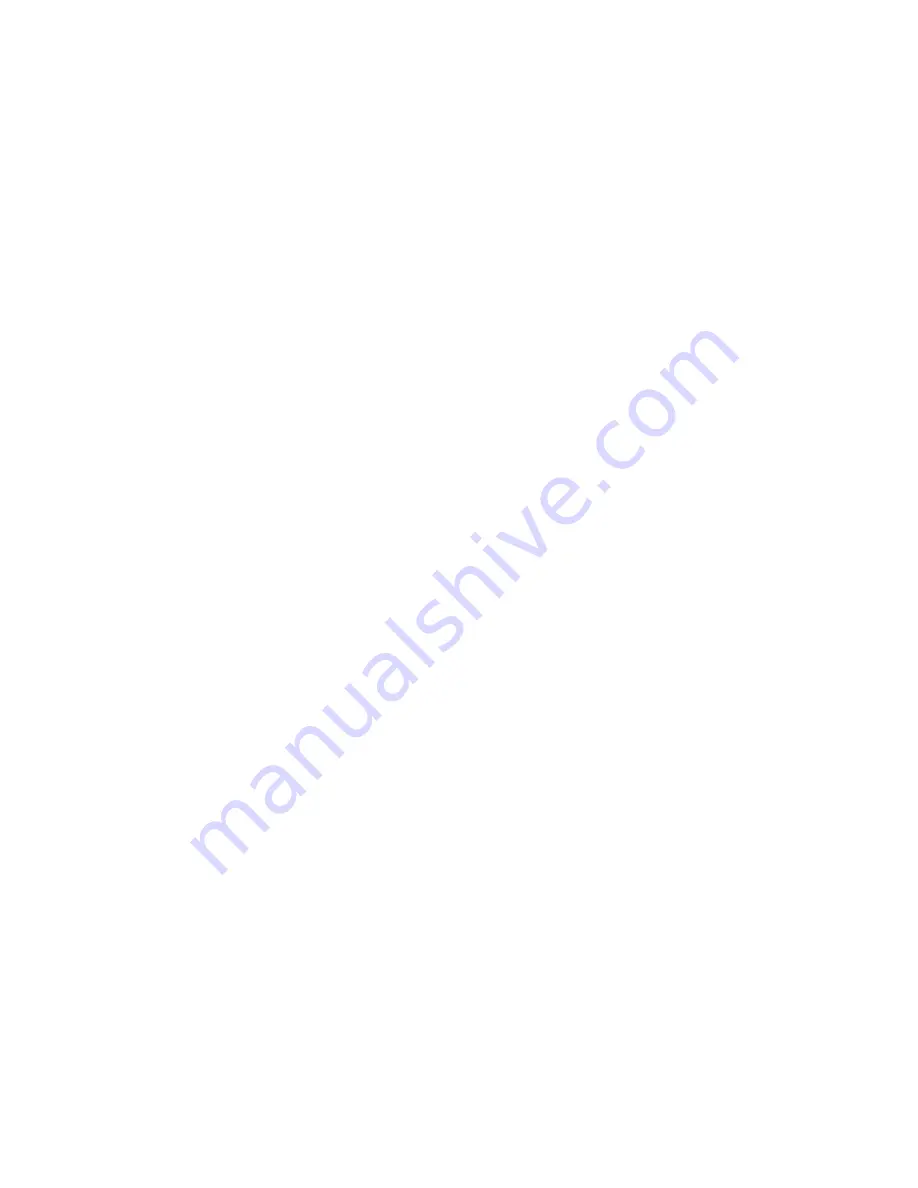
6.0 PRINCIPLE OF OPERATION
6.1
General
Figure 6.1 illustrates the block diagram of the DP Series power supply. As illustrated, DP Series
power supplies are comprised of master/slave modules. Master/slave modules have a power
ratings of 5 kW, 10 kW, or 15 kW to produce 10 kW, 20 kW, or 30 kW system output,
respectively.
DP Series power supplies have a number of feedback loops to insure balance between modules.
The details of the modules are described below.
6.2
Master Module
Power is fed through ac fuses and is distributed to the driver board, inrush limiter, and main 3ö
contactor. The driver board contains a switching power supply and supplies power to the other
printed circuit boards in the system. The inrush limiter is a step start device which is used to
initially charge capacitors on the input dc bus and limit the inrush of current. The inrush limiter is
initiated when the power supply is switched from a standby to a power state. After the charge
cycle, the main 3ö contactor is energized and power is allowed to flow to the load. The optional
EMI filter filters common mode and differential mode noise emanating from the supply.
Output power is controlled through a polyphase chopper. For the 15 kW master module, three
choppers, phased 120° apart, provide a current source to a current fed inverter. The 10.0 kW
master module uses two choppers, phased 180° apart, and the 5.0 kW master module uses only one
chopper. The choppers are controlled with current mode, pulse width modulation (PWM). This
modulation scheme provides a quick response for transients and filtering harmonics on the dc bus.
As illustrated, chopper output current is monitored for balancing and for sensing overload current
conditions. The polyphase chopper has been engineered to eliminate harmonic components
minimizing currents circulating in the power supply.
The polyphase chopper produces a controlled dc bus which is connected to dc link inductors and
current fed, IGBT medium frequency link inverter. The inverter, which operates at 400 Hz to 600
Hz, excites the main transformer at higher than normal line frequencies. This operation produces
ohmic isolation between the input and output of the power supply using a transformer of
dramatically reduced size.
The inverter operates with a 50% duty cycle and its frequency of operation is transparent to the
performance of the power supply.
The output of the main power transformer is converted to dc via rectifiers. Low voltage versions
of the DP Series power supply use midpoint diode configurations and higher voltage versions use
bridge configurations.
107
Содержание DP SERIES II
Страница 1: ...OPERATING AND SERVICE MANUAL DP SERIES II DC POWER SUPPLIES...
Страница 2: ......
Страница 3: ...MAGNA POWER ELECTRONICS INC 39 ROYAL ROAD FLEMINGTON NJ 08822 January 6 2010...
Страница 4: ......
Страница 6: ...improper use of the equipment and accessories ii...
Страница 28: ...Figure 1 2 DP Series air cooled 10 kW to 30 kW package drawing with D Version front panel 15...
Страница 29: ...Figure 1 3 DP Series water cooled 10 kW to 30 kW package drawing with D Version front panels 16...
Страница 39: ...Figure 2 3 DPC Series controls and indicators Energizes control circuits without turning on main power 26...
Страница 44: ...Figure 3 2 Set voltage output at memory displayed Figure 3 3 Set current output at memory displayed 31...
Страница 45: ...Figure 3 4 Set over voltage trip at memory displayed Figure 3 5 Set over current trip at memory displayed 32...
Страница 47: ...Figure 3 7 Set remote sense Figure 3 8 Set internal control 34...
Страница 48: ...Figure 3 9 Set external control Figure 3 10 Set rotary input 35...
Страница 49: ...Figure 3 11 Set keypad input Figure 3 12 Set external program input 36...
Страница 50: ...Figure 3 13 Set remote input Figure 3 14 Set external interlock 37...
Страница 53: ...Figure 3 15 Calibration 40...
Страница 56: ...Figure 3 17 Set remote sense Figure 3 18 Set internal control Figure 3 19 Set external control 43...
Страница 57: ...Figure 3 20 Set rotary input Figure 3 21 Set external program input Figure 3 22 Set remote input 44...
Страница 61: ...Figure 3 24 Calibration 48...
Страница 63: ...Figure 3 25 a Local and b remote sensing 50...
Страница 64: ...Figure 3 26 External a resistive b voltage and current programming 51...
Страница 111: ...98...
Страница 113: ...Figure 5 1 Configuration setup Figure 5 2 GPIB communications setup 100...
Страница 118: ...Figure 5 7 Register Panel Figure 5 8 Calibration Panel 105...
Страница 119: ...Figure 5 9 Firmware Panel Figure 5 10 Modulation Panel for Version D models only 106...
Страница 121: ...Figure 6 1 Block diagram 108...
Страница 128: ...source Figure 8 2 Leadless remote sensing Figure 8 3 IV characteristics for a typical photovoltaic array 115...
Страница 139: ...Figure B 1 Information Panel Figure B 2 Configure Panel 126...
Страница 140: ...Figure B 3 Reboot in Progress Panel Figure B 4 Web Control Panel 127...
Страница 145: ...Figure D 1 RS485 a 2 wire and b 4 wire connections 132...