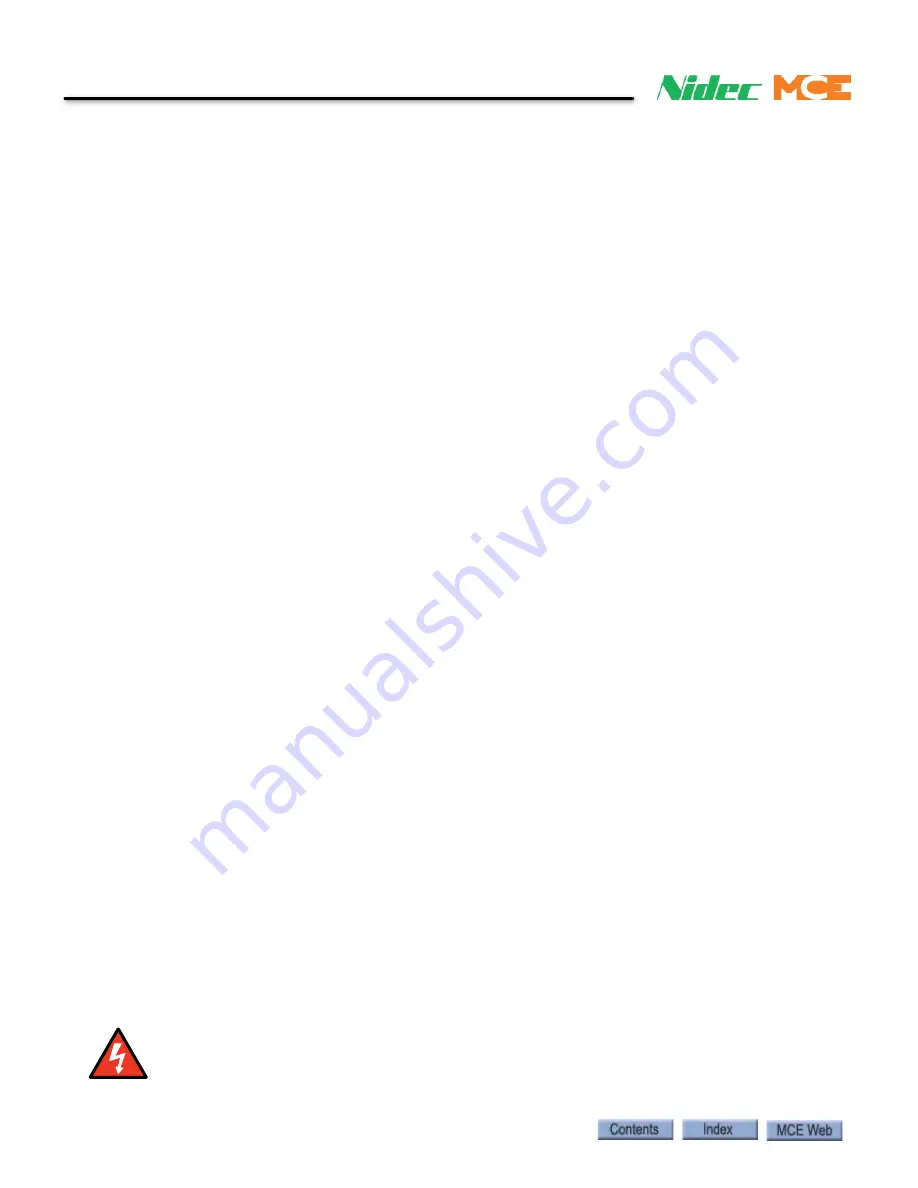
3-12 Manual # 42-02-2223
Inspection Mode
Counterweight Balancing
On modernizations, the weight of the car is often changed but compensating adjustments to the
counterweight are sometimes overlooked. This adjustment is important for achieving desired
performance and ride characteristics.
1. Place a balanced load in the car (specified percentage of full load; typically 40%).
2. On Inspection, run car to the middle of the hoistway to the position learned by perform-
ing the Counterweight Learn Procedure (
see “Counterweight Learn Procedure” on
page 3-11)
. Verify position using the
Actual
Position displayed on the Operational Status
tab.
3. Turn controller power OFF.
4. Use a portable supply to inject sufficient DC voltage at controller terminals B1 and B2 to
lift the brake. (Or, manually lift the brake.)
5. Watch the car to see if it drifts. If not, the car and counterweight are balanced.
• If the car drifts up, remove weight from the counterweight or add weight to the car and
repeat the balancing procedure.
• If the car drifts down, add weight to the counterweight or remove weight from the car
and repeat the balancing procedure.
• For a drum machine, follow the manufacturer counterweighting recommendations
and test the drum machine limit switches.
6. When car and counterweight are balanced, record the actual weight in the car for future
reference. Balanced load = _____________lbs. Restore controller power.
Run Testing
1. Verify all landing system magnets are installed according to job prints and instructions.
2. On inspection mode, run the car to the midpoint of the hoistway.
3. Set the iBox Test switch to the ON position.
4. Place the car on Machine Room Inspection, with Cartop Inspection OFF.
At this point, the car should be on Inspection operation and running without oscillation. There
may be substantial rollback when the car first starts.
5. On the iView Virtual Oscilloscope, set Test point 1 to
Pattern (Command)
.
6. Use a digital voltmeter to check the pattern voltage on iBox test point STP1 with respect
to the Common terminal.
7. Verify Pattern scaling is at 100% (Configuration > Pattern > Common tab) and the
Inspection - High speed parameter is at 10% of contract speed (Configuration > Pattern
> Modes tab). Maximum value for Inspection - High speed is 150fpm. Verify Reduced
inspection speed option is enabled and that Inspection - Low speed is set to 25 fpm.
8. Run the car on Inspection and check the voltage at iBox test point STP1. If 8.0VDC is
equal to contract speed, then the reading at 10% should be 0.8VDC (+/- 5%).
9. Set Inspection - High speed to 50fpm.
10. On Inspection, run car to, or near, the bottom landing. Use test weights to load the car to
125% of full load in preparation for checking the ability of the brake to hold this weight.
Danger
If the brake does not hold, the car may slide into the pit. Use extreme caution.
Содержание Nidec iControl
Страница 1: ...MOTION CONTROL ENGINEERING User Guide iControl with AC Drive...
Страница 15: ......
Страница 23: ...1 8 Manual 42 02 2223 iControl Overview...
Страница 75: ...2 52 Manual 42 02 2223 Construction Mode...
Страница 89: ...3 14 Manual 42 02 2223 Inspection Mode...
Страница 138: ...4 49 Safety Tests iControl AC 4 Figure 4 6 Typical Brake Test Circuit Machine Brake Emergency Brake...
Страница 280: ...6 95 iControl Circuit Board Quick References iControl AC 6 Figure 6 7 Earthquake Board Supporting Information...
Страница 303: ...6 118 Manual 42 02 2223 Troubleshooting...