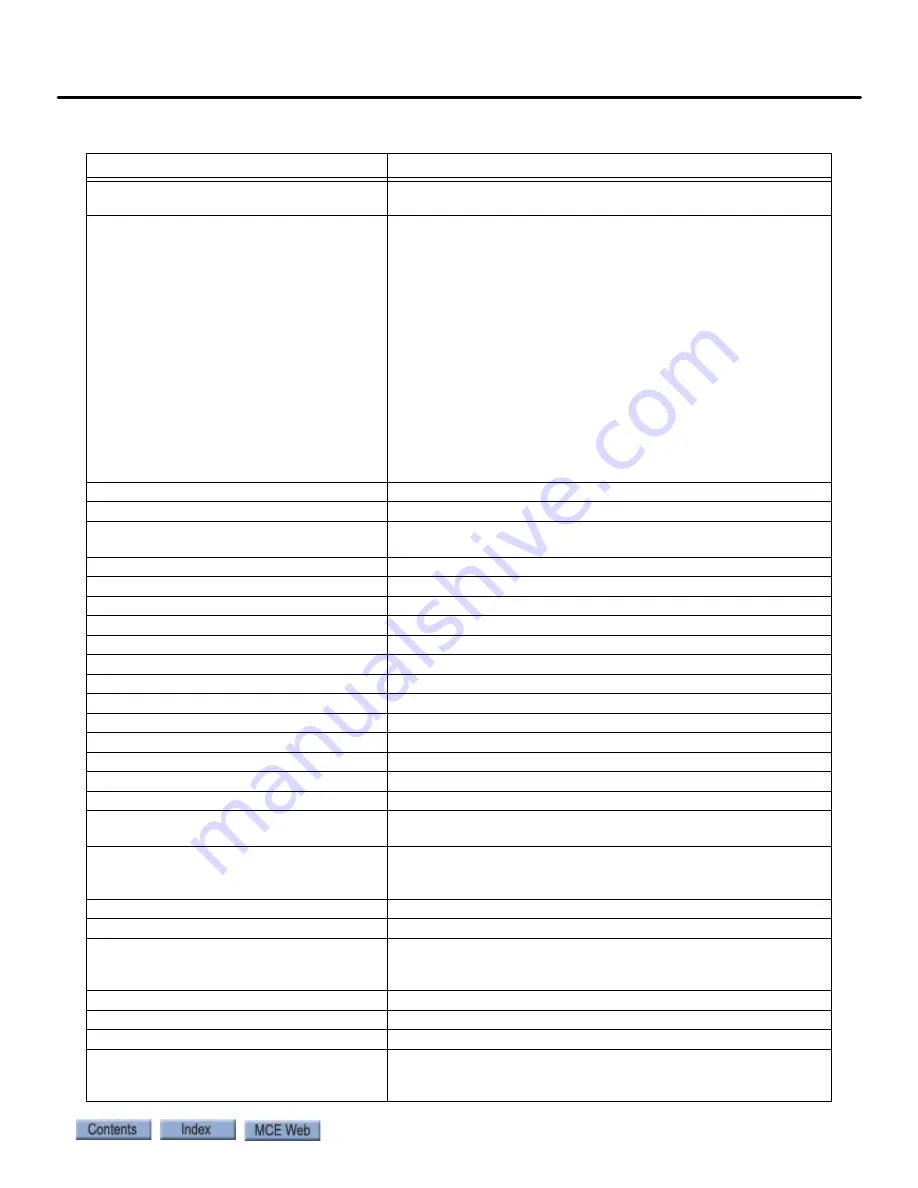
9-3
Software Test Point Signals
iControl AC
9
Armature Composite Control
The summation of Armature Command Control and Armature
Feed forward Control.
Armature Control Set
PID control sets that reflect standard, start (normal), stop (nor-
mal), steady-state (normal) and start (relevel) adjustment
parameters.
Normal:
0 = Idle - before motor contactor picks [PID - Standard]
1 = Idle - after motor contactor picks [PID - Start (normal)]
2 = Acceleration [PID - Standard]
3 = Peak [PID - Steady-State (normal)]
4 = Deceleration [PID - Standard]
5 = Flare [PID - Stop (normal)]
6 = Leveling [PID - Standard]
7 = Idle - before motor contactor drops [PID - Standard]
Relevel:
8 = Idle - before motor contactor picks [PID - Standard]
9 = Idle - after motor contactor picks [PID - Start (relevel)]
10 = Acceleration - Leveling [PID - Standard]
Armature Current Dampen Feedback
Armature current dampening signal.
Armature Current Signal
Raw armature current feedback signal.
Armature Current Synthetic Feedback
Armature current synthetic speed signal used for internal speed
reference and for current safety calibration.
Armature Differential Command
Armature differential command.
Armature Differential Gain
Armature differential gain.
Armature Error (Damped)
Dampened armature error signal.
Armature Error (Raw)
Raw armature error signal.
Armature Feedforward (Control)
Filtered armature feedforward command.
Armature Feedforward (Raw)
Raw armature feedforward command.
Armature Integral Command
Armature integral command.
Armature Integral Gain
Armature integral gain.
Armature On Status
High = PID control enabled.
Armature Proportional Command
Armature proportional command.
Armature Proportional Gain
Armature proportional gain.
Armature Voltage Dampen Feedback
Armature voltage dampening signal.
Armature Voltage Signal
Raw armature voltage feedback signal.
Armature Voltage Synthetic Feedback
Armature voltage synthetic speed signal used for internal speed
reference and for voltage safety calibration.
Brake Contactor Status
Indicates status (open/closed) of brake contactor. When the sig-
nal is high, the contacts are closed. When the contactor is closed
AND the brake field module is enabled, the brake will lift.
Brake Current Feedback
Filtered brake current feedback signal.
Brake Current Signal
Raw brake current feedback signal.
Brake Enable Status
Indicates status of signal that enables the brake field module.
When high, the module is enabled. When the module is enabled
AND the contactor is closed, the brake will lift.
Brake Voltage Feedback
Filtered brake voltage feedback signal.
Brake Voltage Signal
Raw brake voltage feedback signal.
DAC Offset Status
Indicates whether DAC signal offset is positive or negative.
Drive Enable Status
Indicates status of signal that enables the motor field module.
When high, the module is enabled. When the module is enabled
AND the contactor is closed, the motor will run.
Table 9.2 Test Point Signals
Test Signal
Description / Text References
Содержание Nidec iControl
Страница 1: ...MOTION CONTROL ENGINEERING User Guide iControl with AC Drive...
Страница 15: ......
Страница 23: ...1 8 Manual 42 02 2223 iControl Overview...
Страница 75: ...2 52 Manual 42 02 2223 Construction Mode...
Страница 89: ...3 14 Manual 42 02 2223 Inspection Mode...
Страница 138: ...4 49 Safety Tests iControl AC 4 Figure 4 6 Typical Brake Test Circuit Machine Brake Emergency Brake...
Страница 280: ...6 95 iControl Circuit Board Quick References iControl AC 6 Figure 6 7 Earthquake Board Supporting Information...
Страница 303: ...6 118 Manual 42 02 2223 Troubleshooting...