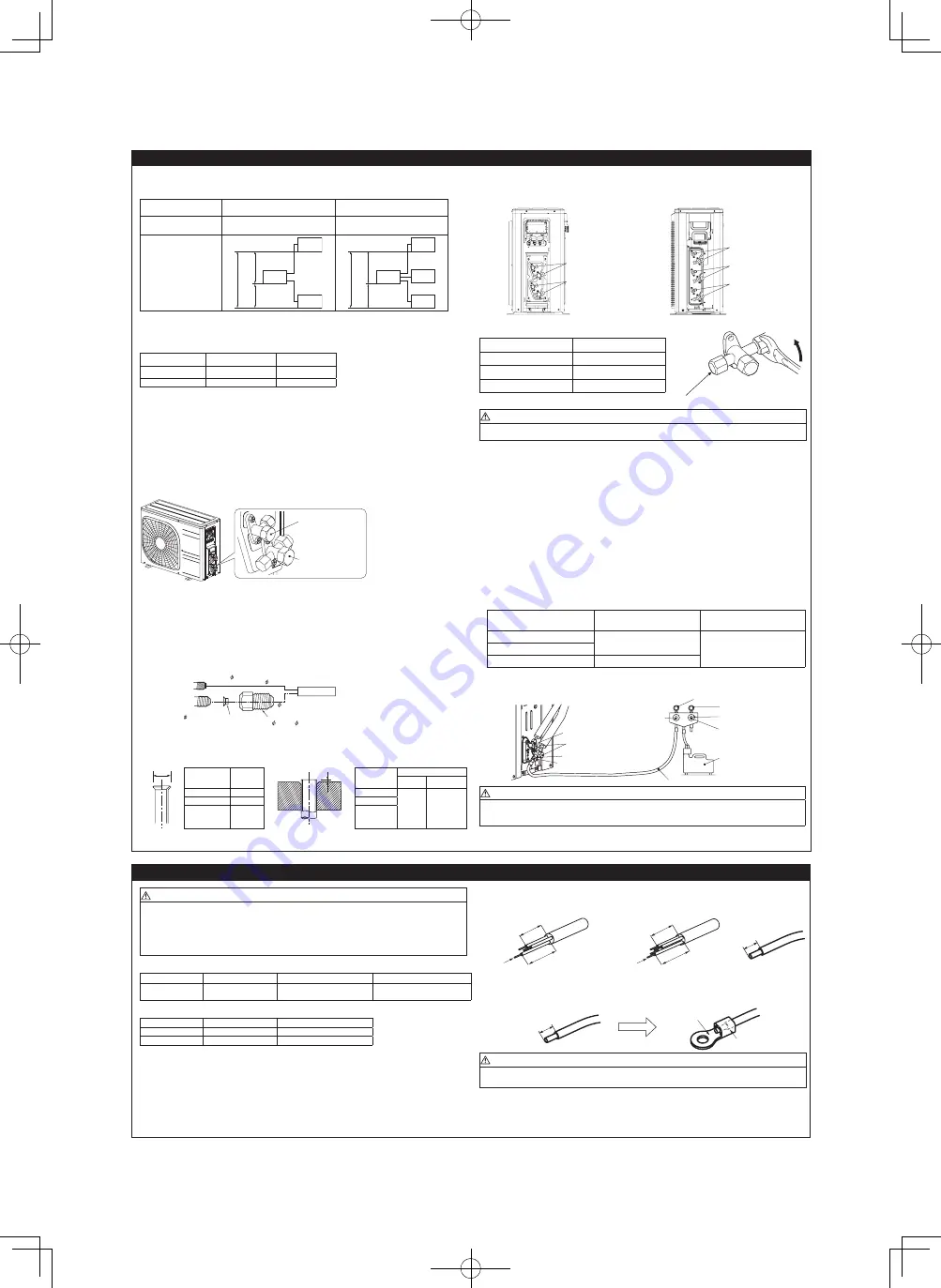
-
20
-
'16 • SCM-T-199
4. CONNECTING PIPING WORK
1. Restrictions on unit installation
Abide by the following restrictions on unit installation.
Improper installation can cause compressor failure or performance degradation.
Model SCM40/45
Model SCM50/60
piping length
one indoor unit MAX 25m
all indoor unit MAX 30m
one indoor unit MAX 25m
all indoor unit MAX 40m
hight difference
MAX
25m
MAX 15m
MAX 15m
outdoor
unit
indoor
unit
indoor
unit
MAX
25m
MAX 15m
MAX 15m
outdoor
unit
indoor
unit
indoor
unit
indoor
unit
2. Preparation of connecting pipe
2.1. Selecting connecting pipe
Select connecting pipe according to the following table.
Indoor unit
Model 20/25/35
Model 50/60
Gas pipe
ø9.52
ø12.7
Liquid pipe
ø6.35
ø6.35
• Pipe wall thickness must be greater than or equal to 0.8 mm.
• Pipe material must be O-type (Phosphorus deoxidized seamless copper pipe ICS 23.040.15, ICS
77.150.30).
2.2. Cutting connecting pipe
(1) Cut the connecting pipe to the required length with pipe cutter.
(2) Hold the pipe downward and remove the burrs. Make sure that no foreign material enters the pipe.
(3) Cover the connecting pipe ends with the tape.
3. Piping work
Check that both liquid and gas operation valves are fully closed.
Carry out the piping work with operation valves fully closed.
Liquid service valve
Gas service valve
3.1. Flaring pipe
(1) <SCM40/45>
Take out flare nuts from the service valves of outdoor unit and engage them onto connecting pipes.
<SCM50/60>
Take out flare nuts from the service valves of outdoor unit.
If a 5.0, 6.0 kw class indoor unit (gas side pipe 12.7) is going to be connected to the service valves
(9.52), variable joints available as accessories must be applied to the gas side service valves.
Securely fit the copper packing between the service valve and the variable diameter joint to
prevent shifting.
Engage flare nuts onto connecting pipes.
Service
valve
Liquid side service valve ( 6.35)
6.35 pipe
50,60 model
Indoor unit
Gas side service
valve ( 9.52)
Copper packing
Variable diameter joint
( 9.52 - 12.7)
12.7 pipe
(2) Flare the pipes according to table and figure shown below.
Flare dimensions for R410A are different from those for conventional refrigerant.
Although it is recommended to use the flaring tools designed specifically for R410A, conventional flaring
tools can also be used by adjusting the measurement of protrusion B with a flare adjustment gauge.
A
Copper pipe
outer diameter A
0
–0.4
B
Copper pipe
outer diameter
Rigid (clutch) type
R410A
Conventional
ø6.35
9.1
ø6.35
0-0.5
1.0-1.5
ø9.52
13.2
ø9.52
ø12.7
16.6
ø12.7
3.2. Connecting pipes
(1) Connect pipes on both liquid and gas sides.
<SCM40/45>
<SCM 50/60>
Service valve
for room B
Service valve
for room A
Service valve
for room C
Service valve
for room B
Service valve
for room A
(2) Tighten nuts to specified torque shown in the table below.
Service valve size (mm)
Tightening torque (N·m)
ø6.35 (1/4")
14-18
ø9.52 (3/8")
34-42
ø12.7 (1/2")
49-61
Do not hold the valve cap area with a spanner
CAUTION
• Do not apply refrigerating machine oil to the flared surface. It can cause refrigerant leakage.
• Do not apply excess torque to the flared nuts. The flared nuts may crack resulting in refrigerant leakage.
4. Evacuation
(1) Connect vacuum pump to gauge manifold. Connect charge hose of gauge manifold to a service port
of outdoor unit.
(2) Run the vacuum pump for at least one hour after the vacuum gauge shows -0.1MPa (–76cm Hg).
(3) Confirm that the vacuum gauge indicator does not rise even if the system is left for 15 minutes or more.
Vacuum gauge indicator will rise if the system has moisture left inside or has a leakage point.
Check the system for the leakage point. If leakage point is found, repair it and return to (1) again.
(4) Close the Handle Lo and stop the vacuum pump.
Keep this state for a few minutes to make sure that the compound pressure gauge pointer does not
swing back.
(5) Remove valve caps from liquid service valve and gas service valve.
(6) Turn the liquid service valve's rod 90 degree counterclockwise with a hexagonal wrench key to open
valve.
Close it after 5 seconds, and check for gas leakage.
Using soapy water, check for gas leakage from indoor unit's flare and outdoor unit's flare and valve rods.
Wipe off all the water after completing the check.
(7) Disconnect charging hose from gas service valve's service port and fully open liquid and gas service
valves. (Do not attempt to turn valve rod beyond its stop.)
(8) Tighten service valve caps and service port cap to the specified torque shown in the table below.
Service valve size (mm)
Service valve cap tightening
torque (N·m)
Service port cap tightening
torque (N·m)
ø6.35 (1/4")
20-30
10-12
ø9.52 (3/8")
ø12.7 (1/2")
25-35
(9) Repeat the above steps (1) to (8) for all connected indoor units.
Charge hose
Handle Lo
Valve cap
Liquid service valve
Gas service valve
Service port
Compound pressure gauge
Pressure gauge
Gauge manifold
Handle Hi
Vacuum pump
CAUTION
• To prevent the entering of different oil into the refrigeration system, do not use tools designed for any
other refrigerant type (R22, R407C, etc.).
• To prevent vacuum pump oil from entering into the refrigerant system, use a counterflow prevention adapter.
5. ELECTRICAL WIRING WORK
WARNING
• Make sure that all the electrical work is carried out in accordance with the national or regional electri-
cal standards.
• Make sure that the earth leakage breaker and circuit breaker of appropriate capacities are installed
(Refer to the table given below).
• Do not turn on the power until the electrical work is completed.
• Do not use a condensive capacitor for power factor improvement under any circumstances.
(It does not improve power factor. Moreover, it can cause an abnormal overheat accident).
Breaker specifications
Model
Phase
Earth leakage breaker
Circuit breaker
SCM40/45/50/60
Single phase
Leakage current: 30mA,
0.1sec or less
Over current: 25A
Main fuse specification
Model
Specification
Parts No.
SCM40/45/50
250V 15A
SSA564A136
SCM60
250V 20A
SSA564A136A
1.Preparing cable
(1) Selecting cable
Select the power source cable and connecting cable in accordance with the specifications mentioned below.
(a) Power source cable
3-core* 4.0mm
2
or more, conformed with 60245 IEC57(CENELEC H05RN-F)
When selecting the power source cable length, make sure that voltage drop is less than 2%.
If the wire length gets longer, increase the wire diameter.
(b) Connecting cable
4-core* 1.5mm
2
, conformed with 60245 IEC57(CENELEC H05RN-F)
* 1 Earth wire is included (Yellow/Green).
(2) Arrange each wire length as shown below.
Make sure that each wire is stripped 10mm from the end.
<Power source cable>
<Connecting cable>
<Wire end>
Earth wire
40mm or more
30mm or more
40mm or more
Earth wire
30mm or more
10mm
(3) Attach round crimp-type terminal to each wire as shown in the below.
Select the size of round crimp-type terminal after considering the specifications of terminal block and wire
diameter.
10mm
Round crimp-type terminal
Sleeve
CAUTION
Power source cable and connecting cable must conform to the specifications mentioned in the manual.
Using cables with wrong specifications may result in unit malfunction.
Содержание SCM40ZS-S
Страница 114: ...113 16 SCM T 199 source PJA012D783...
Страница 200: ...199 16 SCM T 199 4 Troubleshooting procedure If the air conditioner runs NO NO NO NO YES YES YES YES 200 201 207 201 207...
Страница 285: ...284 16 SCM T 199 B PJZ012D077 2 Model RC EX1A eco touch REMOTE CONTROL RC EX1A INSTALLATION MANUAL...
Страница 311: ...310 16 SCM T 199 4 10 5 Superlink E board SC ADNA E F SL2NA E and SL4 AE BE to control...
Страница 312: ...311 16 SCM T 199...