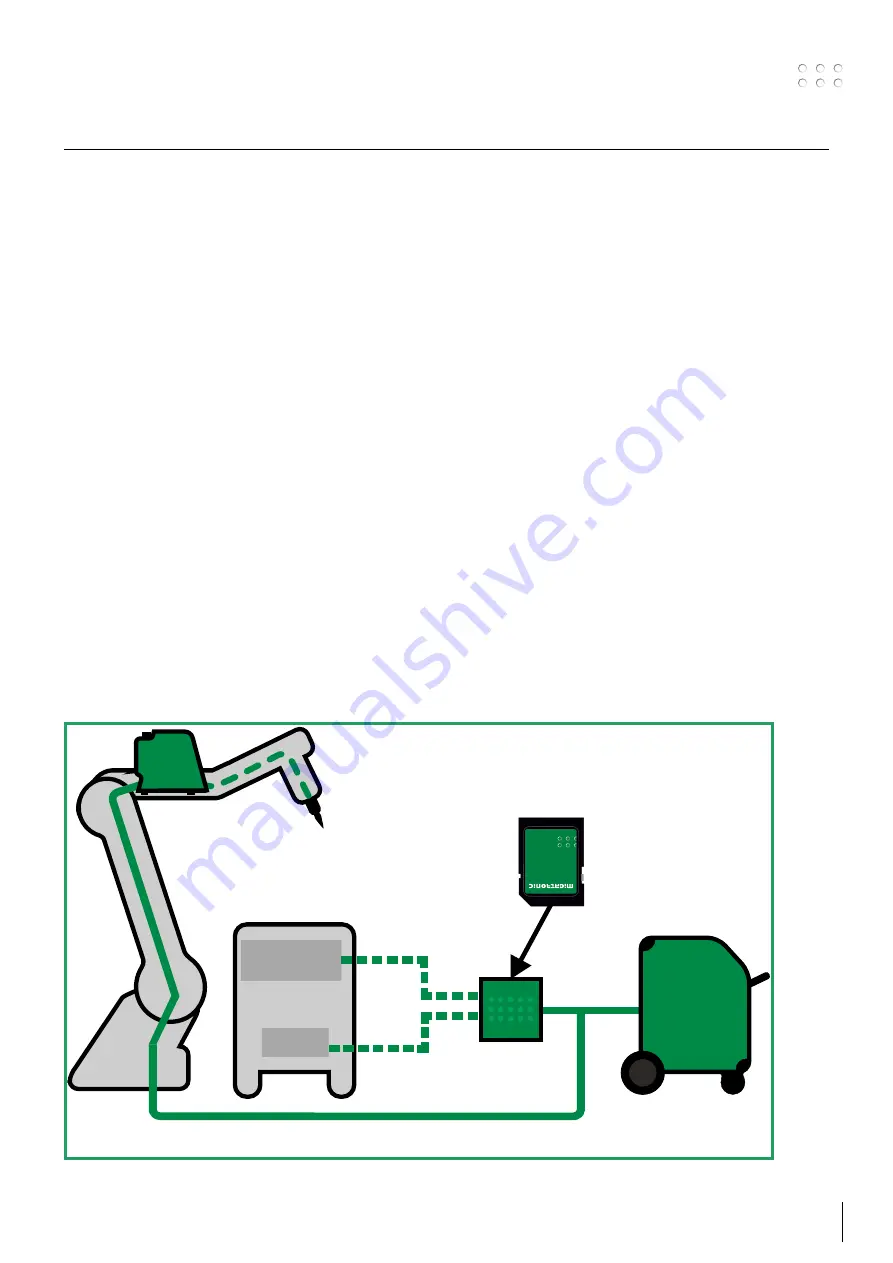
4
5
Robot Control Interface (RCI
2
)
The Robot Control Interface is a flexible I/O
interface system designed for controlling
different Migatronic machines and devices by
means of robots controllers and PLCs.
The Robot Control Interface (RCI
2
) acts as
“translator” between MIGANET and the
connected robot controller.
Interface concept
Several machine parameters like program
selection, secondary functions, internal alarms
etc. are fully accessible, and thus creation
of both sophisticated and simple custom
applications is possible.
There are two possible ways to control the
welding machine, of which only one can be
active at a time:
1: Serial communication:
Serial communication through Fieldbus
and industrial Ethernet via ANYBUS
communication modules. (Referred to as
Fieldbus in the rest of this manual.)
2: Analog communication:
A set of analog inputs and outputs can
control the welding machine.
Configuration
RCI
2
has to be setup for the desired way of
communication, by loading a configuration file
directly into RCI
2
.
There are four different groups of configuration
files.
Pi/Pi Plasma – Analog communication
Pi/Pi Plasma – Fieldbus serial communication
Sigma Galaxy – Analog communication
Sigma Galaxy – Fieldbus serial communication
Each group can contain more configuration files
with special functionality.
See list on page 33-64.
SD card
The SD card contains the configurations files that
are needed by RCI
2
.
It also contains documentation and setup files
that are needed by the robot/PLC controller.
How it works
PLC
Fieldbus
communication
Analog
communication
MIGANET
(CANBUS)
ANALOG/DIGITAL
I/O INTERFACE
ROBOT
CONTROLLER
CONFIGURATION
FILE
Содержание RCI2
Страница 1: ...USER GUIDE ROBOT CONTROL INTERFACE RCI2 50115001 C1 Valid from 2019 week 24...
Страница 79: ...79...