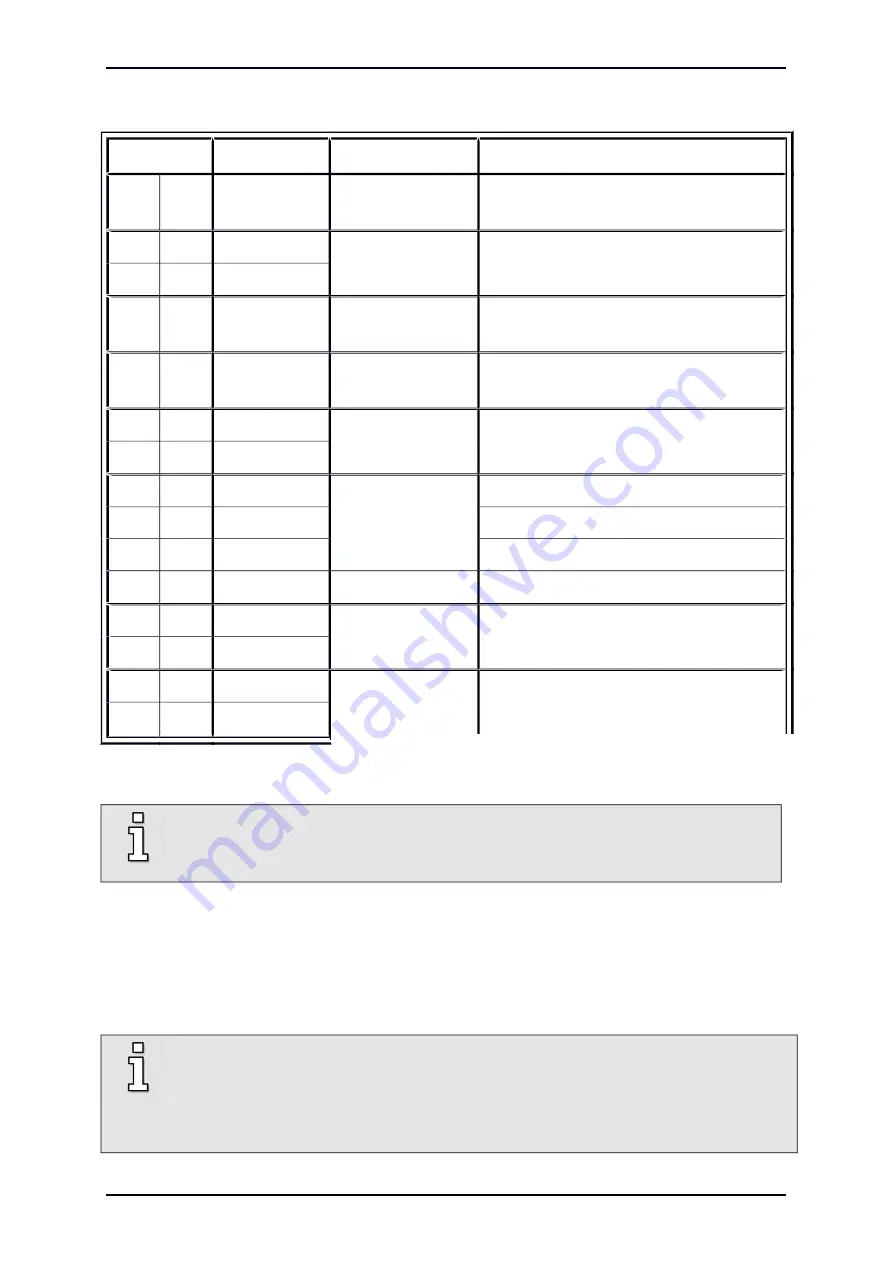
Page 94
Table 37:
Pin assignment: Digital incremental encoder [X2B]
Pin No
Denomination
Values
Specification
1
MT+
+3,3 V / Ri = 2 k
Motor temperature sensor
1)
, normally closed
contact, PTC, KTY
9
5 V ... 12 V
R
I
1 k
Sensor cables for encoder supply
2
U_SENS-
10
US
5 V / 12 V /
10 %
I
max
= 300 mA
Supply voltages for high-resolution
incremental encoder
3
GND
0V
Reference potential encoder supply and
motor temperature sensor
11
N
2 V
SS
…
5 V
SS
RI
120
Reset pulse trace signal RS422 (differential)
from digital incremental encoder
4
#N
12
H_U
0 V / 5 V
RI
2 k
at VCC
Phase U hall sensor for commutation
5
H_V
Phase V hall sensor for commutation
13
H_W
Phase W hall sensor for commutation
6
14
A
2 V
SS
…
5 V
SS
RI
120
A trace signal RS422 (differential) from
digital incremental encoder
7
#A
15
B
2 V
SS
…
5 V
SS
RI
120
B trace signal RS422 (differential) from
digital incremental encoder
8
#B
1)
Please comply with
Chapter 9 Additional requirements for the servo drives concerning the UL approval
on
page 113.
In addition, a low-impedance connection of the outer cable shield to the housing of the
servo drive has to be established. Therefore, the outer cable shield of the angle
encoder cable must be connected to the housing of the angle encoder connector.
8.7.4 Cable type and design [X2B]
We recommend using the encoder connection cables released for their product by the corresponding
manufacturer (Heidenhain, Sick-Stegmann, and so on). If the manufacturer does not recommend a
particular cable, we recommend the assembly of the encoder connection cables as described below.
For the angle encoder supply US and GND, we recommend
a minimum cross-section of 0,25 mm² for an angle encoder cable length up to 25 m
and
a minimum cross-section of 0,5 mm² for an angle encoder cable length up to 50 m.
Product Manual „Servo drives ARS 2100 SE“
Version 5.0