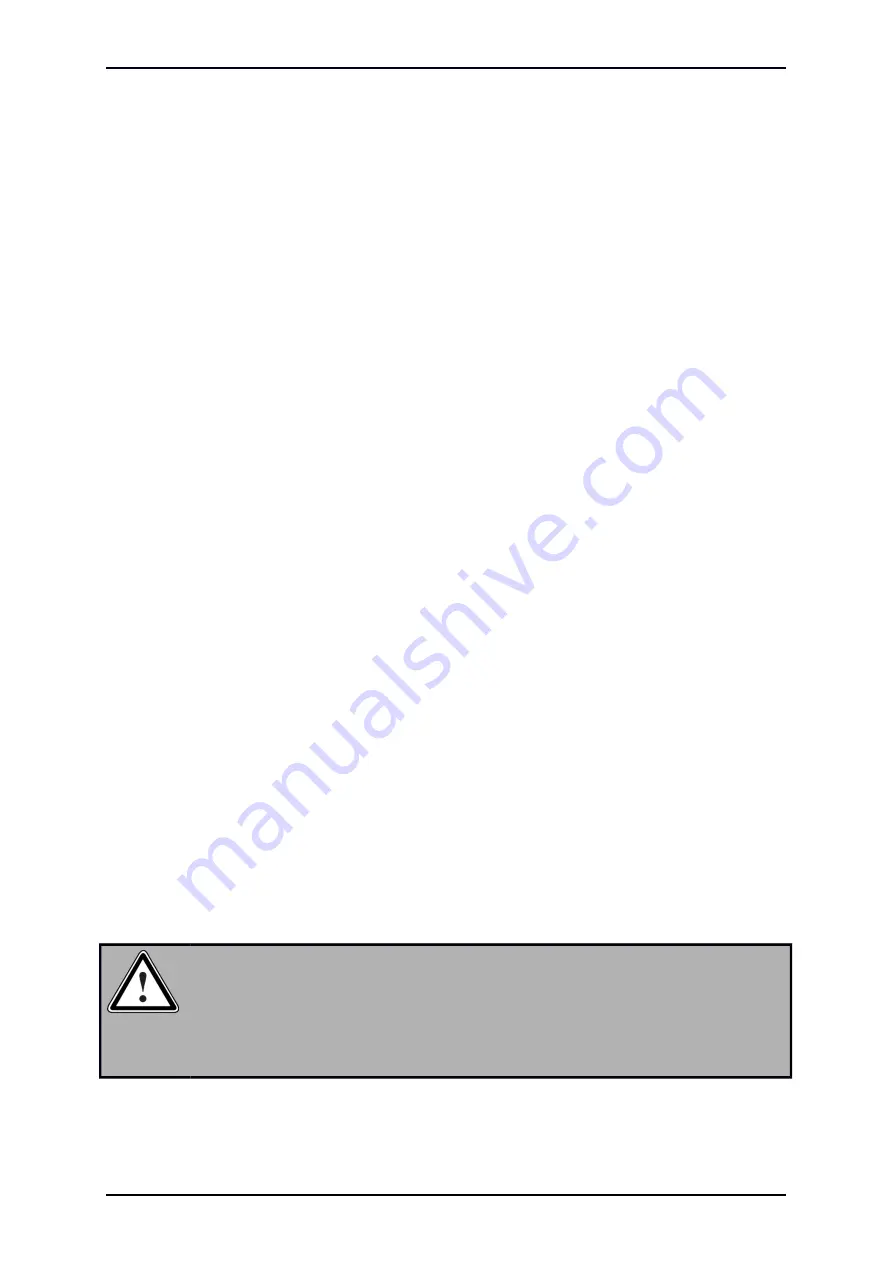
Page 111
8.14.4 EMC compliant cabling
The following must be considered for an EMC-compliant setup of the drive system (see also
chapter 8
Electrical installation, page 72
):
In order to keep the leakage currents and the losses in the motor connection cable as small as
possible, the servo drive ARS 2100 SE should be located as close to the motor as possible (see
also the following
chapter
Operation with long motor cables , page 112
Motor cable and angle encoder cable must be shielded
The shield of the motor cable is connected to the housing of the servo drive ARS 2100 SE (shield
connection terminal). The cable shield also has to be connected to the associated servo drive so
that the leakage currents can flow back into the servo drive causing the leakage
The mains-end PE connection is connected to the PE connection point of the supply connection
[X9]
The inner PE conductor of the motor cable is connected to the PE connection point of the motor
connection [X6]
The signal lines must be as far away from the power cables as possible. They should not be
placed parallel. If intersections cannot be avoided, they should be perpendicular (that is at a 90°
angle), if possible
Unshielded signal and control lines should not be used. If their use is inevitable they should at
least be twisted
Even shielded cables will inevitably have short unshielded ends (unless shielded connector
housings are used). In general, the following applies:
Connect the inner shields to the corresponding pins of the connectors; Maximum length
40 mm
Length of the unshielded cores 35 mm maximum
Connect the total shield on the servo drive side plane to the PE terminal; Maximum length
40 mm
Connect the total shield on the motor side plane to the connector housing or motor housing;
Maximum length 40 mm
DANGER!
For safety reasons, all PE ground conductors must be connected prior to initial
operation.
The EN 61800-5-1 regulations for protective earthing must be complied with during
installation!
Product Manual „Servo drives ARS 2100 SE“
Version 5.0