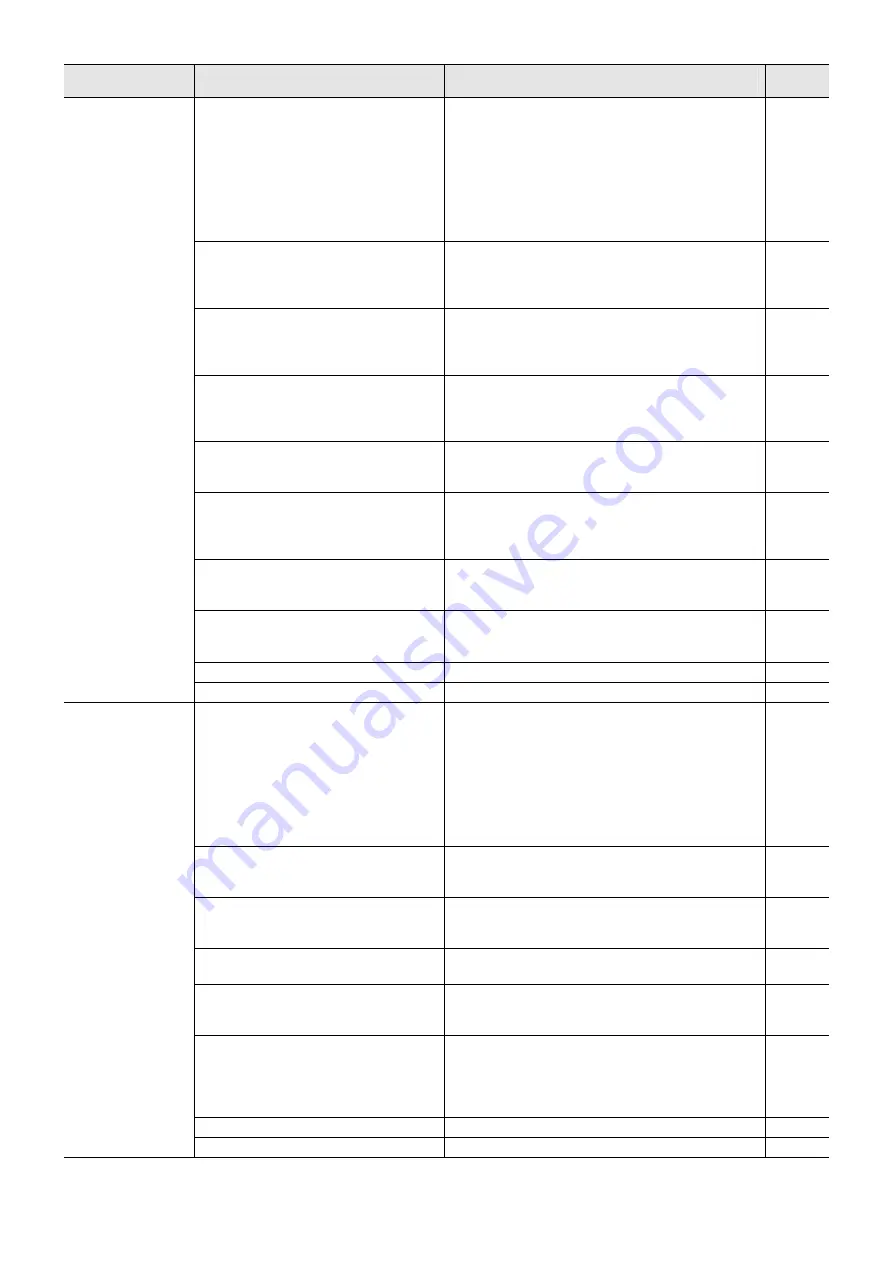
5-20
Symptom
Content of the likely cause
Countermeasures
Reference
The motor does
not operate when
the run command
is issued.
The wirings of the analogue input or
variable resistor of the frequency
command is wrong.
Correct the wirings.
• Measure the voltage between FV to SC terminal
with a tester and check that the correct voltage
is flowing if using the analogue voltage or
variable resistor input.
• Disconnect the wirings and measure the current
between current source to FI terminal with a
tester and check that the correct current is
flowing if using the analogue current input.
“51: F-TM (force terminal block)” is
assigned to the multi function input
terminal to run with the operator, and it
is in ON state.
Turn OFF the assigned terminal.
“31: OPE (force operator function)” is
assigned to the multi function input
terminal to run with the control circuit
terminal block, and it is in ON state.
Turn OFF the assigned terminal.
The inverter is tripped. (ALARM LED
lights up, and “Exxx” is displayed)
Press the STOP/RESET key to release the trip
(reset), and find the cause and perform
countermeasures from the alarm code, and then
restart.
Safety function switching switch is ON,
and either the multi function input
terminal S3/GS1, or S4/GS2 is OFF.
Turn both of the safety input GS1 and GS2 if using
the safety function. Turn the switching switch OFF if
not used.
“18: RS (reset)”, “14: CS (commercial
switch)”, “11: FRS (freelance top)” is
assigned to the multi function input
terminal, and it is in ON state.
Turn OFF the corresponding terminal.
“84: ROK (run OK signal)” is assigned
to the multi function input terminal, and
it is in OFF state.
Turn ON the assigned terminal.
There is a breakage in the wiring from
the inverter to the motor, and the
wirings within the motor.
Check the wirings.
Excessive load.
Reduce the load.
The motor is being restrained.
Release the restrain.
The rotational
speed of the motor
does not increase.
Poor contact in the analogue input or
variable resistor of the frequency
command.
Check the wirings.
• Measure the voltage between FV to SC terminal
with a tester and check that the correct voltage
is flowing if using the analogue voltage or
variable resistor input.
• Disconnect the wirings and measure the current
between voltage source to FI terminal with a
tester and check that the correct current is
flowing if using the analogue current input.
The overload restriction or the
overcurrent restriction function is
operating.
Disable the function, or raise the operation level.
The primary maximum frequency
(A004) and frequency maximum limit
(A061/A261) settings are low.
Change the settings.
Acceleration time is long
Shorten the acceleration time
(F002/F202/A092/A292).
“06: JG (jogging)” is assigned to the
multi function input terminal, and it is in
ON state.
Turn OFF the assigned terminal.
“02: CF1” to “05: CF4” are assigned to
the multi function input terminal, and is
in ON state.
Turn OFF the multi step speed setting. (If the multi
step speed setting is ON, it will run in multi step
speed operation, so it will run according to the
frequency set in the multi step speed command 1 to
15 (A021 to A035).)
Excessive load.
Reduce the load.
The motor is being restrained.
Release the restrain.
Содержание MK0003
Страница 2: ......
Страница 8: ...0 6...
Страница 12: ...1 4 2 DIMENSIONAL DRAWING OF OUTRIGGER WIDTH...
Страница 17: ...1 9 4 WORKING RADIUS LIFTING HEIGHT...
Страница 18: ...1 10 Working range diagram Outrigger extended to maximum Main boom 1 section...
Страница 19: ...1 11 Working range diagram Outrigger extended to maximum Main boom 2 sections...
Страница 20: ...1 12 Working range diagram Outrigger extended to maximum Main boom 2 5 sections...
Страница 21: ...1 13 Working range diagram Outrigger extended to maximum Main boom 3 sections...
Страница 22: ...1 14 Working range diagram Outrigger extended to minimum Main boom 1 section...
Страница 23: ...1 15 Working range diagram Outrigger extended to minimum Main boom 2 sections...
Страница 24: ...1 16 Working range diagram Outrigger extended to minimum Main boom 2 5 sections...
Страница 25: ...1 17 Working range diagram Outrigger extended to minimum Main boom 3 sections...
Страница 26: ...1 18 5 RATED TOTAL LOAD CHART...
Страница 32: ...2 4...
Страница 33: ...2 5 1 HYDRAULIC CIRCUIT DIAGRAM 200 1176600...
Страница 34: ...2 6...
Страница 35: ...2 7 2 HYDRAULIC PIPING DIAGRAM 2 1 CRANE ROTATING PART 200 1171800...
Страница 41: ...2 13 2 2 CONTROL LINE A...
Страница 43: ...2 15 2 3CONTROL LINE B Perform spiral winding on the entire perimeter of the hose of this part...
Страница 45: ...2 17 2 4 TRAVEL LINE...
Страница 47: ...2 19 2 5 OUTRIGGER LINE...
Страница 49: ...2 21 2 6 PT LINE 102 1152000 4...
Страница 69: ...2 41...
Страница 70: ...2 42...
Страница 71: ...2 43...
Страница 76: ...2 48 4 8 ENGINE ACCESSORIES 102 1149200...
Страница 90: ...2 62 7 2 INTERNAL STRUCTURE...
Страница 120: ...2 92 Part B Writing method for wire number Two places...
Страница 123: ...2 95 Figure 1 Index point Figure 2 Connection diagram...
Страница 166: ...2 138 15 4 APPEARANCE OF OUTRIGGER ON REAR LEFT SIDE 200 2167300...
Страница 173: ...2 145 17 ELECTRIC CIRCUIT DIAGRAM 200 1176500 01...
Страница 174: ...2 146 18 ELECTRIC SYSTEM 18 1 1 WIRE HARNESS OF MACHINE BODY 1 200 1172200 1...
Страница 176: ...2 148 18 1 2 WIRE HARNESS OF MACHINE BODY 2 200 1172200 2...
Страница 179: ...2 151 19 CONTROL ASSEMBLY 19 1 CONTROLLER 1 TTC60 Pin arrangement...
Страница 180: ...2 152 TTC60 I O...
Страница 181: ...2 153 2 TTC36X Pin arrangement...
Страница 182: ...2 154 TTC36X lower part I O...
Страница 209: ...2 181 19 2 5 LIST OF CONTROLLER INPUT MONITORING...
Страница 210: ...2 182 19 2 6 LIST OF CONTROLLER ANALOG INPUT OUTPUT MONITORING...
Страница 245: ...3 9 1 2 3 ANGLE METER 360 S200M3297000...
Страница 274: ...3 38...
Страница 293: ...4 19 8 SERVICE LOCATIONS...
Страница 294: ...4 20...
Страница 296: ...5 2 1 ELECTRICAL MOTOR UNIT ASSEMBLY Unit weight 180 kg...
Страница 299: ...5 5 1 1 POWER UNIT 1 Power unit cover 2 Electric motor 3 Coupling 4 Hydraulic pump Power supply box...
Страница 323: ...5 29 3 POWER SUPPLY BOX 1 Power supply box 2 Power supply box door 3 Door handle 4 Terminal block 5 Cable inserting hole...
Страница 324: ...5 30...
Страница 325: ...5 31 4 ELECTRICAL DIAGRAM S200M3122000 01...
Страница 326: ...5 32 S200M3122000 02...
Страница 336: ...6 8 1 3 2 INTERNAL STRUCTURE OF WINCH MOTOR...
Страница 345: ...6 17 4 WORKING RADIUS LIFTING HEIGHT OF ONE FALL WINCH...
Страница 348: ......