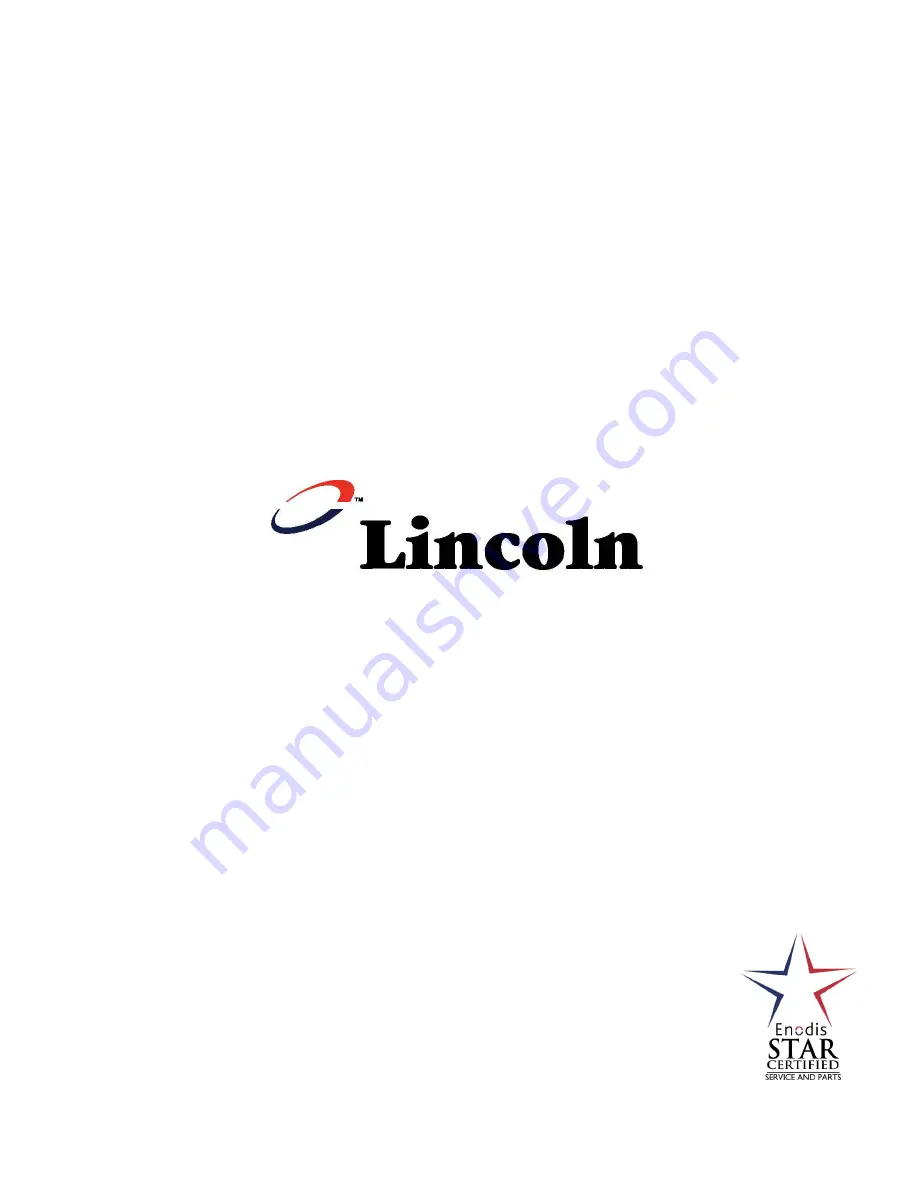
1100svcdom
REV 1/5/07
SERVICE MANUAL
(DOMESTIC)
IMPINGER CONVEYOR OVENS
MODEL 1100 SERIES
Lincoln Foodservice Products, LLC
1111 North Hadley Road
Fort Wayne, Indiana 46804
United States of America
Phone : (800) 374-3004
U.S. Fax: (888) 790-8193 • Int’l Fax: (260) 436-0735
Technical Service Hot Line
(800) 678-9511
www.lincolnfp.com
Содержание IMPINGER 1100
Страница 8: ...Impinger II 1100 Series Service Manual Domestic 8 SCHEMATIC 1100 1101 ...
Страница 9: ...Impinger II 1100 Series Service Manual Domestic 9 SCHEMATIC 1102 1103 ...
Страница 10: ...Impinger II 1100 Series Service Manual Domestic 10 SCHEMATIC 1116 1117 S N 2011383 BELOW ...
Страница 11: ...Impinger II 1100 Series Service Manual Domestic 11 SCHEMATIC 1116 1117 S N 2011384 ABOVE ...
Страница 13: ...Impinger II 1100 Series Service Manual Domestic 13 SCHEMATIC 1130 1131 S N 2011384 ABOVE ...
Страница 14: ...Impinger II 1100 Series Service Manual Domestic 14 SCHEMATIC 1160 1161 S N 2011978 ABOVE ...
Страница 16: ...Impinger II 1100 Series Service Manual Domestic 16 SCHEMATIC 1132 1133 S N 2011384 ABOVE ...
Страница 17: ...Impinger II 1100 Series Service Manual Domestic 17 SCHEMATIC 1162 1163 S N 2011978 ABOVE ...
Страница 51: ...Impinger II 1100 Series Service Manual Domestic 51 BLOW UP GENERAL 1100 SERIES ...
Страница 55: ...Impinger II 1100 Series Service Manual Domestic 55 BLOW UP CONTROL COMPARTMENT FRONT 1116 1117 ...
Страница 65: ...Impinger II 1100 Series Service Manual Domestic 65 BLOW UP OVEN BACK ASSEMBLY 1100 SERIES ...
Страница 67: ...Impinger II 1100 Series Service Manual Domestic 67 BLOW UP GEARMOTOR ASSEMBLY 1100 SERIES ...
Страница 69: ...Impinger II 1100 Series Service Manual Domestic 69 BLOW UP CONVEYOR DOOR 1100 SERIES ...
Страница 71: ...Impinger II 1100 Series Service Manual Domestic 71 This page intentionally left blank ...
Страница 72: ...Impinger II 1100 Series Service Manual Domestic 72 ...