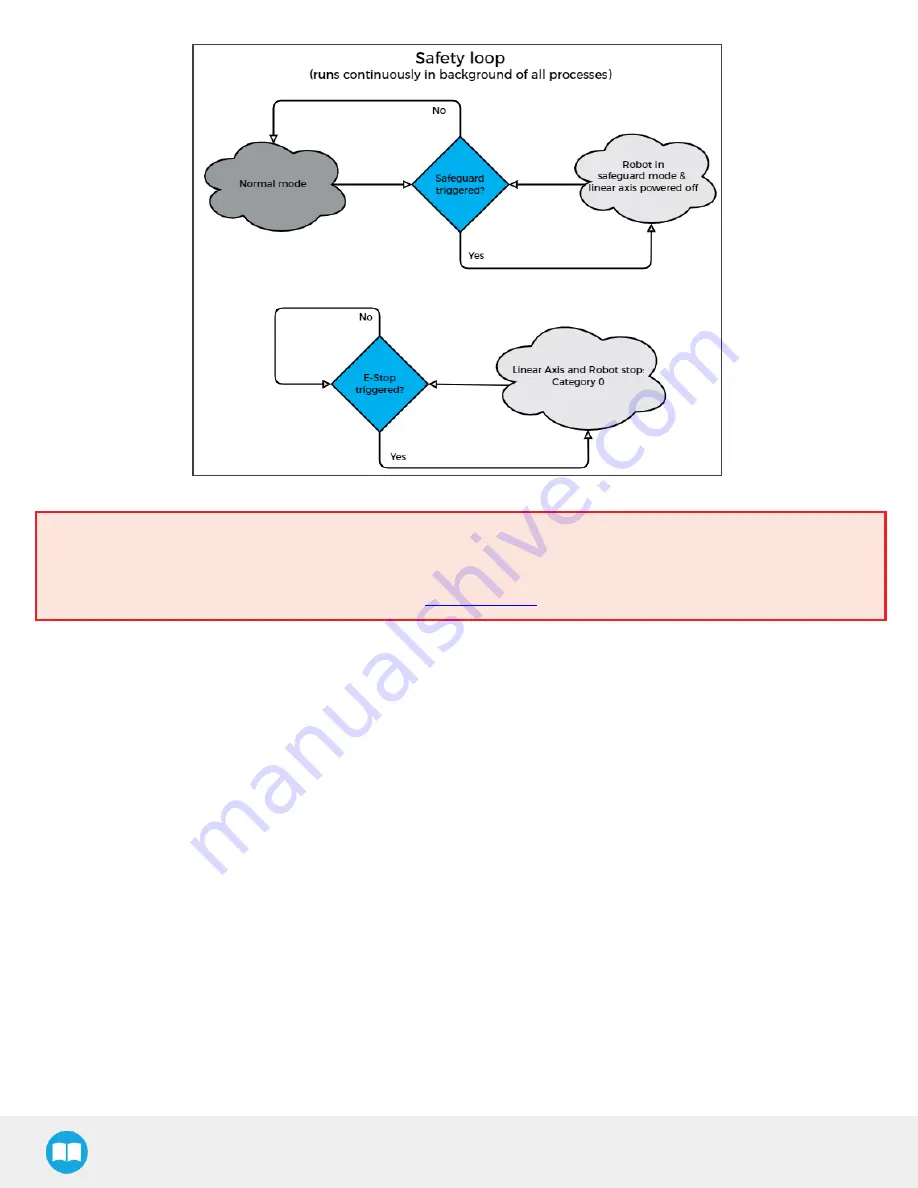
Fig. 2-1: Safety Logical Schema
Warning
In the event of a collision or after an emergency stop, an inspection of the solution must be performed before resuming
the use of the machine. Special attention must be given to the carriage assembly, the linear axis, the cable management
system, and the gripper components. Please contact
if any sign of damage is detected.
2.3.2. Linear Axis Stop Category 0 and 1
When a stop is required, the robot and the linear axis start the process at the same time, even if they are independent, so the
stopping time can differ.
l
For robot information, please refer to the Universal Robots documentation.
l
For the linear axis:
o
Maximal stopping time for Category 1: 500 ms;
o
Maximal stopping time for Category 0: 100 ms*;
o
Travelled distance when there is a stopping time: 33 mm (1-5/16 in)*
*For cases where the robot is immobile, with a payload of 8 kg and the initial speed of the linear axis is 500 mm/s, which is the
maximum allowed speed.
20
Содержание ROBOTIQ AX Series
Страница 4: ...Palletizing Solution Instruction Manual 4...
Страница 14: ...Palletizing Solution Instruction Manual 14...
Страница 21: ...Palletizing Solution Instruction Manual 21...
Страница 82: ...6 1 2 AirPick Vacuum Gripper Fig 6 1 AirPick general dimensions 82...
Страница 83: ...Palletizing Solution Instruction Manual 6 1 3 Extra Reach Bracket 83...
Страница 84: ...6 1 4 Bracket for Two 2 Suction Cups Fig 6 2 Two air nodes bracket s dimensions 84...
Страница 110: ...1 2 2 Safety Connections Fig 12 2 Universal Robots Controller Safety Connections Schema 110...