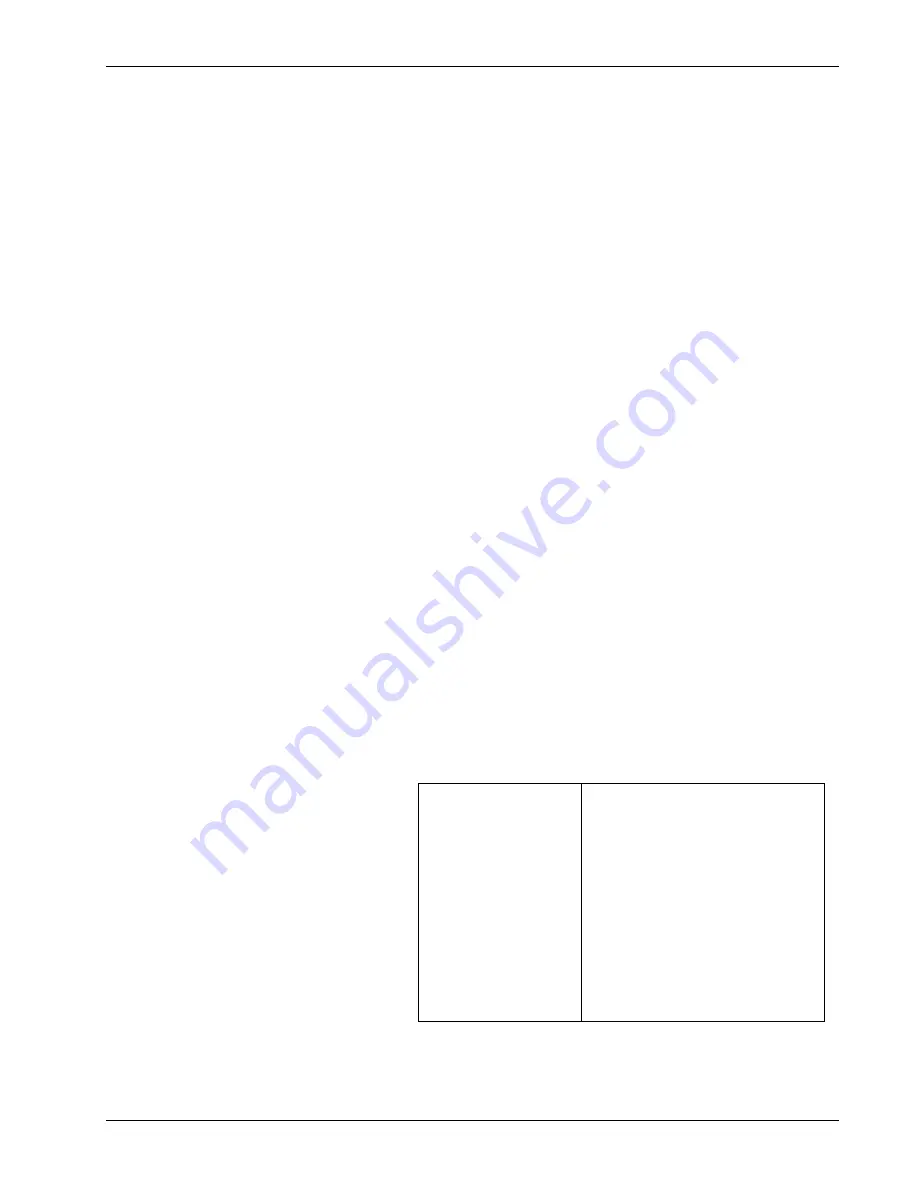
Lake Shore Model 325 Temperature Controller User’s Manual
Remote Operation
6-15
Table 6-6. Serial Interface Specifications
Connector Type:
Connector Wiring:
Voltage Levels:
Transmission Distance:
Timing Format:
Transmission Mode:
Baud Rate:
Handshake:
Character Bits:
Parity:
Terminators:
Command Rate:
9-pin D-style connector plug
DTE
EIA RS-232C specified
50 ft maximum
Asynchronous
Half duplex
9600, 19200, 38400, 57600
Software timing
1 start, 7 data, 1 parity, 1 stop
Odd
CR(0DH) LF(0AH)
20 commands per second maximum
6.2
SERIAL INTERFACE OVERVIEW
The serial interface used in the Model 325 is commonly referred to as an RS-232C interface. RS-232C is a standard of
the Electronics Industries Association (EIA) that describes one of the most common interfaces between computers and
electronic equipment. The RS-232C standard is quite flexible and allows many different configurations. However, any
two devices claiming RS-232C compatibility cannot necessarily be plugged together without interface setup. The
remainder of this section briefly describes the key features of a serial interface that are supported by the instrument.
A customer-supplied computer with similarly configured interface port is required to enable communication.
6.2.1
Physical Connection
The Model 325 has a 9-pin D-subminiature plug on the rear panel for serial communication. The original RS-232C
standard specifies 25 pins but both 9- and 25-pin connectors are commonly used in the computer industry. Many third
party cables exist for connecting the instrument to computers with either 9- or 25-pin connectors. Section 8.7.1 gives the
most common pin assignments for 9- and 25-pin connectors. Please note that not all pins or functions are supported by
the Model 325.
The instrument serial connector is the plug half of a mating pair and must be matched with a socket on the cable. If a
cable has the correct wiring configuration but also has a plug end, a “gender changer” can be used to mate two plug ends
together.
The letters DTE near the interface connector stand for Data Terminal Equipment and indicate the pin connection of the
directional pins such as transmit data (TD) and receive data (RD). Equipment with Data Communications Equipment
(DCE) wiring can be connected to the instrument with a straight through cable. As an example, Pin 3 of the DTE
connector holds the transmit line and Pin 3 of the DCE connector holds the receive line so the functions complement.
It is likely both pieces of equipment are wired in the DTE configuration. In this case Pin 3 on one DTE connector (used
for transmit) must be wired to Pin 2 on the other (used for receive). Cables that swap the complementing lines are called
null modem cables and must be used between two DTE wired devices. Null modem adapters are also available for use
with straight through cables. Section 8.7.1 illustrates suggested cables that can be used between the instrument and
common computers.
The instrument uses drivers to generate the transmission voltage levels required by the RS-232C standard. These
voltages are considered safe under normal operating conditions because of their relatively low voltage and current limits.
The drivers are designed to work with cables up to 50 feet in length.
6.2.2
Hardware Support
The Model 325 interface hardware supports the following features. Asynchronous timing is used for the individual bit
data within a character. This timing requires start and stop bits as part of each character so the transmitter and receiver
can resynchronize between each character.
Half duplex transmission allows the
instrument to be either a transmitter or a
receiver of data but not both at the same time.
Communication speeds of 9600, 19200,
38400, 57600 baud are supported. The baud
rate is the only interface parameter that can be
changed by the user.
Hardware handshaking is not supported by the
instrument. Handshaking is often used to
guarantee that data message strings do not
collide and that no data is transmitted before
the receiver is ready. In this instrument,
appropriate software timing substitutes for
hardware handshaking. User programs must
take full responsibility for flow control and
timing as described in Section 6.2.5.
Содержание 325
Страница 4: ...Lake Shore Model 325 Temperature Controller User s Manual...
Страница 6: ......
Страница 22: ...Lake Shore Model 325 Temperature Controller User s Manual 1 10 Introduction This Page Intentionally Left Blank...
Страница 47: ...Lake Shore Model 325 Temperature Controller User s Manual 3 11 This Page Intentionally Left Blank...
Страница 48: ...Lake Shore Model 325 Temperature Controller User s Manual 3 12 This Page Intentionally Left Blank...
Страница 76: ...Lake Shore Model 325 Temperature Controller User s Manual 4 28 Operation This Page Intentionally Left Blank...
Страница 122: ...Lake Shore Model 325 Temperature Controller User s Manual 6 36 Remote Operation This Page Intentionally Left Blank...
Страница 128: ...Lake Shore Model 325 Temperature Controller User s Manual 7 6 Options and Accessories...