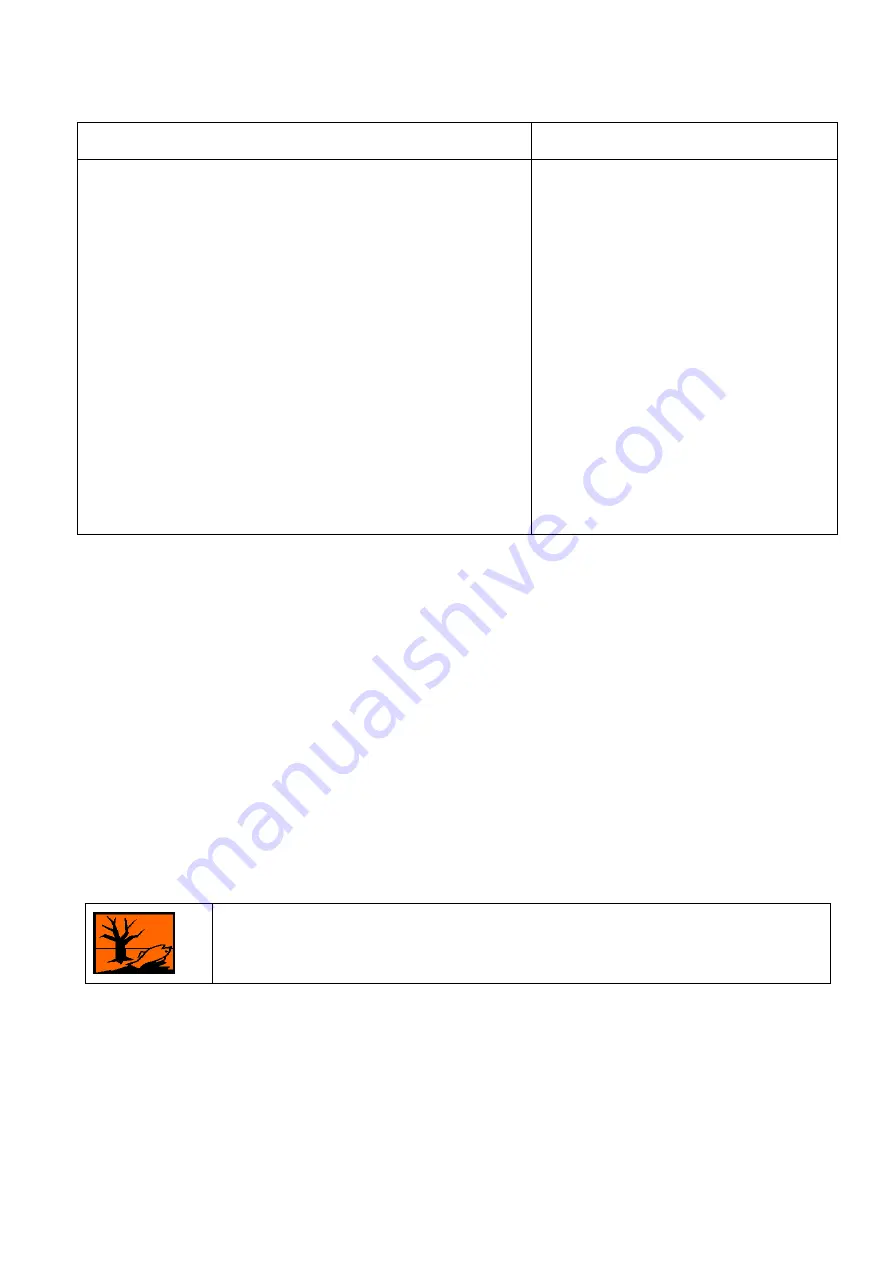
30
Main inspection.
According to the requirements a main inspection of the motor must be organised
annually after approximately 7,000 hours of operation.
The following examinations will be done at standstill of the
motor:
The following examinations will be
done when the motor is running:
- Check of the foundations. There must be no cracks or
other damages like depressions.
- Check of the motor alignment. The motor alignment must
be within the given tolerances.
- Check of the fastening bolts. All bolts used for fixing
mechanical and electrical connections must be tight (see
also the table for tightening torques for bolts in chapter 11.
Commissioning).
- Check of the cables and the insulation material. The
examination must check if the cables and used insulation
materials are in good conditions. They must not be
discoloured or even burnt and they must not be broken,
cracked or faulty in any other way.
- Check of the insulation resistance. The insulation
resistance of the winding must be measured.
- According to the grease quality and bearing type of the
motor it can be necessary to change the grease after 7,000
working hours. Apart from that the necessary relubrication
periods for friction bearings must be observed, because
they differ from the inspection periods.
- Check of the electric characteristics.
- Check of the bearing temperatures. It
is examined if the permissible bearing
temperatures will be exceeded during
operation of the motor.
- Check of the running noises. When
the motor is running, it is checked if the
quiet running has changed for the
worse.
If the examination results in differences from the values specified in the mainenance manual or if
there are other faults or damages detected, than these must be corrected immediately.
Periodically they need to be cleaned externally and if they work in an environment where impurities
can close the ventilation openings on fan cover or fill the spaces between the cooling ribs, such
impurities must be blown out with compressed air or swept-off with brush. Any aberration from motor
ratings or irregular motor operation must be carefully inspected for possible cause (i.e. increased
motor current, temperature increase over the permitted value for the declared insulation class,
increased vibrations, peculiar noises, specific insulation smell presence, activated motor protection
devices or similar). If this is caused by the motor, the repair work must be performed by the
authorized and skilled personnel only.
For spare parts contact the manufacturer with exact motor type mark and code number from motor
nameplate (please note the ordering instruction attached).
Standard bearing assembly is with single row deep-grove ball bearings (ZZ or 2RS), with clearance
C3 (motors of 7AT132-315 series are made with standard clearance bearings) as listed in table
below. The bearings are lubricated for life. Bearing change in case of breakdown, noise or at regular
service intervals must be performed with adequate tools without the use of excessive force and
punching.
9. Bearing and regressing
Before carrying out any maintenance work on the beds, drain oil. The operator is
responsible for the safe disposal of used oil in accordance with the regulations for
environmental protection
If bearings with regressing possibility are built-in, the intervals between regreasing are as shown in
the diagram attached. During service repair such bearings are to be taken off from shaft in a proper
way, washed well in gasoline, dried, put on the shaft in a proper way, regreased with adequate grease
in such way that approx. 2/3 of bearing nest free space is filled with grease. Alternatively, the
regreasing can be performed also during the motor is in operation, via regreasing nipples situated on
bearing shields using the hand pump for consistent grease. Depending on the motor size (mostly 132-
280), whith each regreasing approx. 20-40 grams of grease must be pressed-in. Recommended
grease brands are SKF, LIS-2 (INA), SHELL ALVANIA G3, ESSO UNIREX N3, or all others lithium
soap based with drip temperature of 180-200
0
C and for use in environment temperature range from –
20
0
C to +150
0
C.