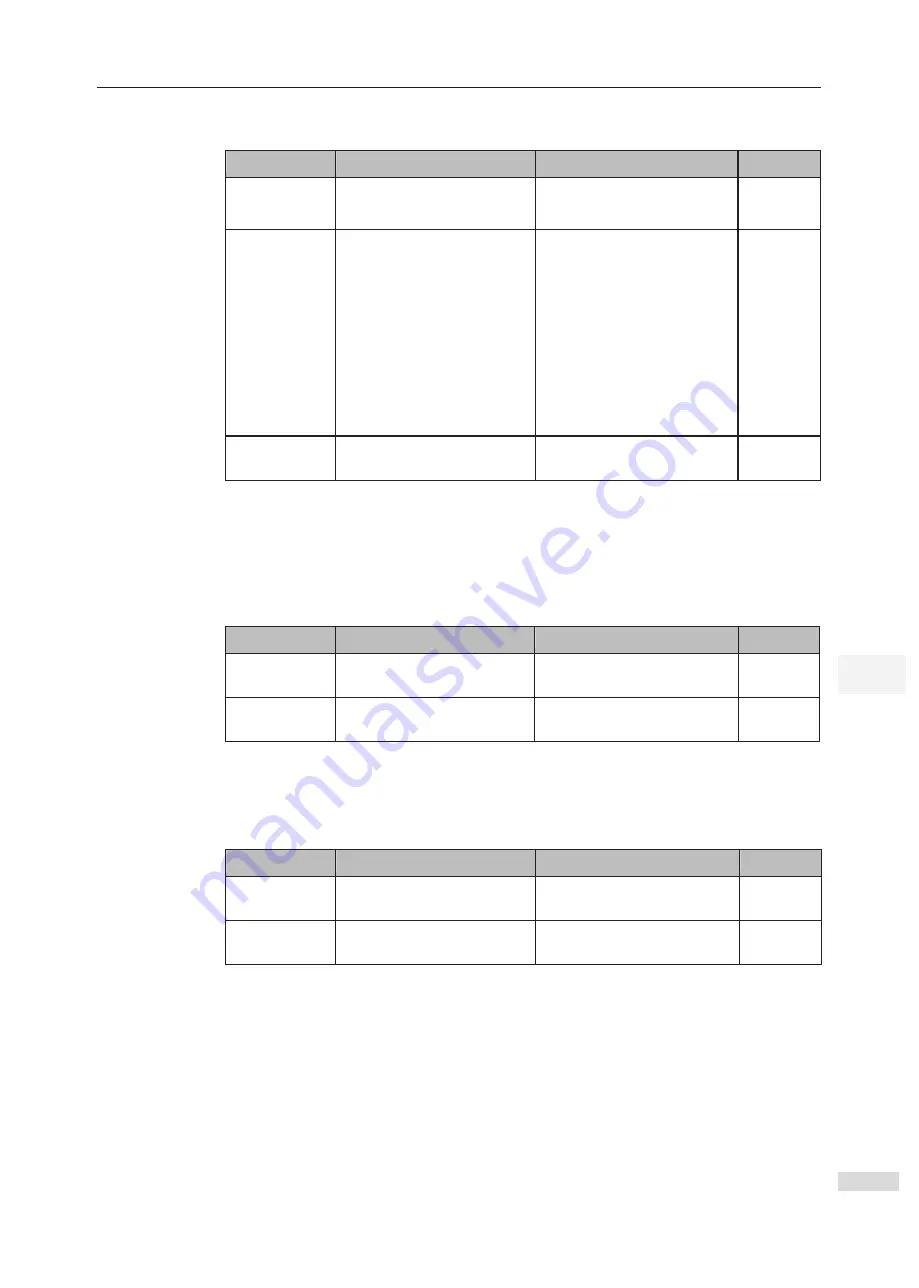
6. Description of Parameters
Function Code
Parameter Name
Setting Range
Default
A0-05
Forward max. frequency in
torque control
0.00 Hz to max. frequency
(F0-10)
50.00 Hz
A0-06
Reverse max. frequency in
torque control
0.00 Hz to max. frequency
(F0-10)
50.00 Hz
6
■
Setting Torque Limit in Torque Control
Function Code
Parameter Name
Setting Range
Default
A0-00
Speed/Torque control
selection
0: Speed control
1: Torque control
0
A0-01
Torque reference source in
torque control
0: Set by A0-03
1: AI1
2: AI2
3: AI3
4: Pulse reference (DI5)
5: Communication reference
6: MIN (AI1, AI2)
7: MAX (AI1, AI2)
0
A0-03
Torque digital setting in
torque control
-200.0% to 200.0%
150.0%
These two function parameters select channel of setting torque reference in torque
control.
Torque reference is a relative value. 100.0% corresponds to rated AC drive torque (can
be viewed in U0-06). When torque reference is a positive value, the AC drive runs in
forward direction. When torque reference is a negative value, the AC drive runs in reverse
direction.
These function parameters set maximum frequency of the AC drive in forward and
reverse directions in torque control.
Motor speed will rise continuously if load torque is smaller than motor output torque. This
function limits motor speed in torque control to prevent runaway.
Function Code
Parameter Name
Setting Range
Default
A0-07
Acceleration time in torque
control
0.00s to 65000s
0.00s
A0-08
Deceleration time in torque
control
0.00s to 65000s
0.00s
These function parameters set acceleration/deceleration time in torque control to
implement smooth change of motor speed. This helps to prevent problems such as big
noise or too large mechanical stress caused by quick change of motor speed.
But in applications where rapid torque response is required, for example, two motors are
used to drive the same load, you need to set these two parameters to 0.00s.
For example, two motors drive the same load. To balance the load level of the two motors,
set one drive as master in speed control and set the other as slave in torque control.
The slave will follow output torque of the master as its torque reference, which requires
quick response to the master output torque. In this case, set acceleration/deceleration
time of the slave in torque control to 0.00s.
- 155 -
Содержание GT600-4T132G
Страница 1: ...GT600 AC Drive...
Страница 5: ......
Страница 86: ...5 Quick Setup 5 1 Get Familiar With Operating Panel 86 5 2 Setup Flowchart 87...
Страница 87: ......
Страница 100: ...5 Quick Setup 98 5...
Страница 280: ...8 Peripherals and Options 278 8...
Страница 306: ...12 303 11...
Страница 362: ......