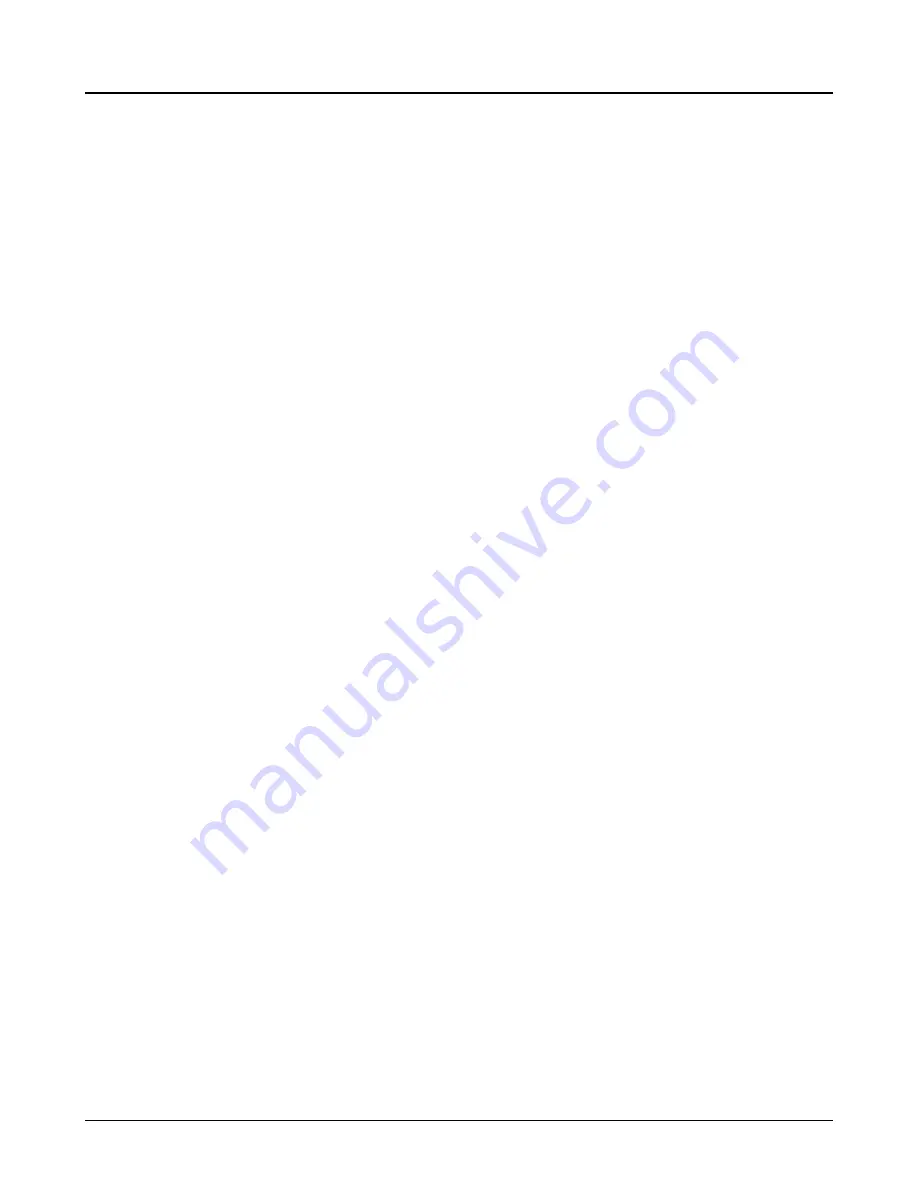
This is extremely important, as the life of a ball bearing can be drastically reduced if contaminated
with even a small amount of dirt. All bearing assembly operations should be done in as dust-free an
atmosphere as possible. All tools, as well as the hands, should be kept clean.
If new ball bearings are being used, they should not be unwrapped until ready for installation and
should not be cleaned or washed unless the protective
wrapper has been broken and dirt allowed to enter the bearing.
If old bearings, or new ones that have been allowed to become dirty, are being used, clean thor-
oughly before installing as follows: Use a clean pail or receptacle. Pour into it one or two quarts of
clean, water-free kerosene. Dip the bearing into the kerosene and spin slowly. Repeat until all
traces of grease have been removed. Now blow dry with clean filtered compressed air, holding the
two races together so that they do not rotate but allowing the inner race to rotate a few turns now
and then to dislodge the kerosene from the retainer pockets. If the bearing is very dirty, it is advisa-
ble to rinse it in a second bath of clean kerosene. When the bearing has been blown dry, oil it imme-
diately with a good grade of clean machine oil; especially the race grooves and balls to prevent cor-
rosion or rust.
15. Place deflectors (123) on shaft. On the Model 3406 - Wipe a small amount of grease on oil seal lips
(332B) and slide bearing housing covers (160) carefully over shaft and replace oil rings (114) on
shaft against bearing housing covers (160).
16. Wipe a small amount of grease on the grease seal lips in bearing housing (134 or 166). Place bear-
ing housings on shaft and slide them along until they contact the shaft sleeves. Care must be taken
not to injure the lips of the grease seals during this operation. A thin piece of shim stock, wrapped
inside the grease seal before sliding over the shaft will protect the seal lips and can readily be re-
moved after the seal is past the shaft shoulder.
17. Slide ball bearing collar (237) over thrust end of shaft (122) and push up against shaft shoulder.
18. The thrust and coupling end ball bearings are the same and can be installed on either end of shaft.
Both bearings are installed in a like manner as follows: Apply a film of oil to the bearing seat on the
shaft. Start bearing "square" and drive on about 1/8", keeping bearing square at all times. Use a
driving sleeve as shown in
Figure 21: Left hand pump on page 48
. Note that the outside diameter of this sleeve should never be larger than the outside
diameter of the inner race of bearing. Next slip the bearing housing over the ball bearing toward the
end of the shaft to eliminate any possibility of binding between the outside of the bearing and the
bearing housing bore. Now continue to drive the bearing solidly against the shaft shoulder.
On the Model 3416 coupling end bearing is single row. Thrust bearing is a duplex bearing (two an-
gular contact bearings, specially matched) and must be mounted in "back-to-back" position. This is
done on the bearing originally sent with the pump by having the stamped faces of the outer rings
against each other.
Both bearings are installed in same manner as the 3405.
Model 3416 uses the following bearings:
Group S
Group M
Group L
Coupling end
305S
307S
310S
Thrust end
7304PD-DB
7306PD-DB
7308PD-DB
19. Place snap ring (361) in groove in shaft on thrust bearing end. Be sure that groove is clean and that
snap ring seats in bottom of groove. Snap ring is flat on one side, tapered on other side. Flat side of
ring must be against bearing.
In the Model 3406 slide oil rings (114) toward bearing to the proper position in the bearing housings.
Bolt the bearing housing covers to the bearing housing, making sure that the oil breather fitting
(113A) in the bearing cover is up when the double locks of the bearing housing are in the lowermost
position. This fitting is used as a pressure release for the bearing housing. It must be in the vertical
position or the bearing will not be properly oiled. (Thrust end bearing end cover is not installed until
Step No. 22.)
7.5 Reassembly of pump
3405-3406-3416 Installation, Operation and Maintenance Instructions
51
Содержание Goulds Pumps 3405
Страница 1: ...Installation Operation and Maintenance Instructions 3405 3406 3416 ...
Страница 2: ......
Страница 19: ...Figure 6 2 5 Install suction piping 3405 3406 3416 Installation Operation and Maintenance Instructions 17 ...
Страница 41: ...7 3 Sectional view 7 3 Sectional view 3405 3406 3416 Installation Operation and Maintenance Instructions 39 ...
Страница 42: ...7 3 Sectional view 40 3405 3406 3416 Installation Operation and Maintenance Instructions ...