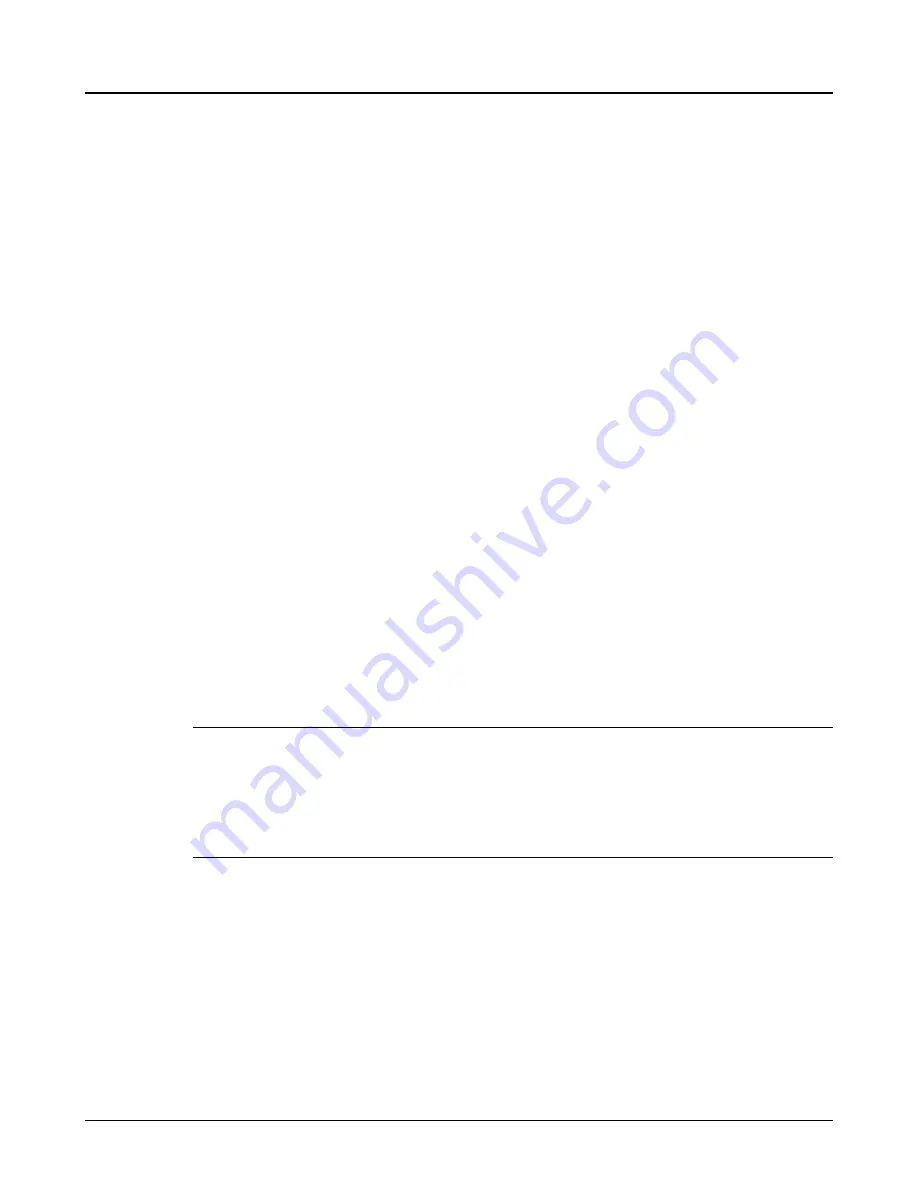
Group
Left hand pump
22: Right hand pump on page 49
S
7-13/16"
9-13/16"
M
9-1/32"
12-17/32"
L
10-3/4"
16"
5.
If it is necessary to replace the impeller wearing rings on pumps so equipped, proceed as follows:
•
Remove old rings. Rings are held by press fit and also by 3 set screws in edge of impeller
and ring.
•
Clean wearing ring seats and press on new rings.
•
Drill 3 holes ("F'' drill, 11/16" deep, 120° apart), so that holes are half in impeller and half in
ring. Tap holes (5/16"-18 tap, 3/8" deep). Screw set screws in hole, and lightly upset first
thread to keep screw from backing out.
•
The impeller wearing rings are supplied 0.020-0.030 inch oversize on the O.D. They should
be turned to size after they are mounted on the impeller. Turning to size after mounting is
the procedure used in the factory, and has the following advantages:
•
Eliminates possibility of runout.
•
Eliminates distortion and expansion due to the press fit.
•
Permits the user to compensate for wear of the casing wearing rings, so that the
casing wearing rings need not be replaced to restore original clearances.
•
Permits the user to select a special clearance for unusual operating conditions.
The table of original clearances in section
7.7 Overhaul of pump on page 54
guide in setting the final dimension of the impeller rings. If rings are 300 series stainless steel, or if
extremely viscous liquids are being handled, the suggested clearance should be increased 0.005
inch.
6.
Insert impeller key (178) in shaft keyway. Turn sleeve (104) about a quarter turn, either way, so that
key cannot enter keyway in this sleeve until after impeller is checked for correct setting in casing.
7.
If the impeller diameter has been cut in the field, the impeller should be statically balanced and, if
possible, dynamically balanced. Balancing can be effected by grinding on the outside of the shrouds
near the periphery.
8.
Place "O" Ring (412A) in groove in end of shaft sleeve (126). Screw shaft sleeve on shaft up to key.
NOTICE:
Model 3405 pumps were previously supplied without "O"-rings ( 412A) in the ends of the shaft
sleeves. On these pumps, coat the large ends of the shaft sleeves and the ends of the impeller
hub with plastic thread compound, gas oil a varnish, or white lead. Old and new style sleeves
are interchangeable. "O"'-rings (412) must be used between shaft sleeve and shaft whether
"O"- rings ( 412A) are used or not. (This applies to step 10 below also.)
9.
Slide impeller on shaft and tap in place against the sleeve with a lead mall. Tap evenly around the
impeller near the wearing ring surface. Do not tap against the sealing surface on end of hub.
10. Place O-ring (412A) in groove in end of shaft sleeve (126). Screw shaft sleeve on shaft up to key.
11. Slip wearing rings (103 or 127) on impeller, being sure that the single lock on the upper half of ring
is toward the center of the impeller.
12. Place stuffing box bushings (125) on shaft and slide over shaft sleeves toward impeller. The single
lock on the upper half of bushings must be toward the outside, away from impeller.
13. If grease or oil seals (322, 333, 332A, or 332B) are being replaced, make sure that the seals are
installed so that the lips of the grease seals face outward, away from the bearings, and the lips of
the oil seals face inward, toward the bearings.
14. Make sure that all parts that are assembled inside the bearing housings, including the shaft, snap
ring, bearing end covers, bearings and oil rings, are entirely free from dust and dirt.
7.5 Reassembly of pump
50
3405-3406-3416 Installation, Operation and Maintenance Instructions
Содержание Goulds Pumps 3405
Страница 1: ...Installation Operation and Maintenance Instructions 3405 3406 3416 ...
Страница 2: ......
Страница 19: ...Figure 6 2 5 Install suction piping 3405 3406 3416 Installation Operation and Maintenance Instructions 17 ...
Страница 41: ...7 3 Sectional view 7 3 Sectional view 3405 3406 3416 Installation Operation and Maintenance Instructions 39 ...
Страница 42: ...7 3 Sectional view 40 3405 3406 3416 Installation Operation and Maintenance Instructions ...