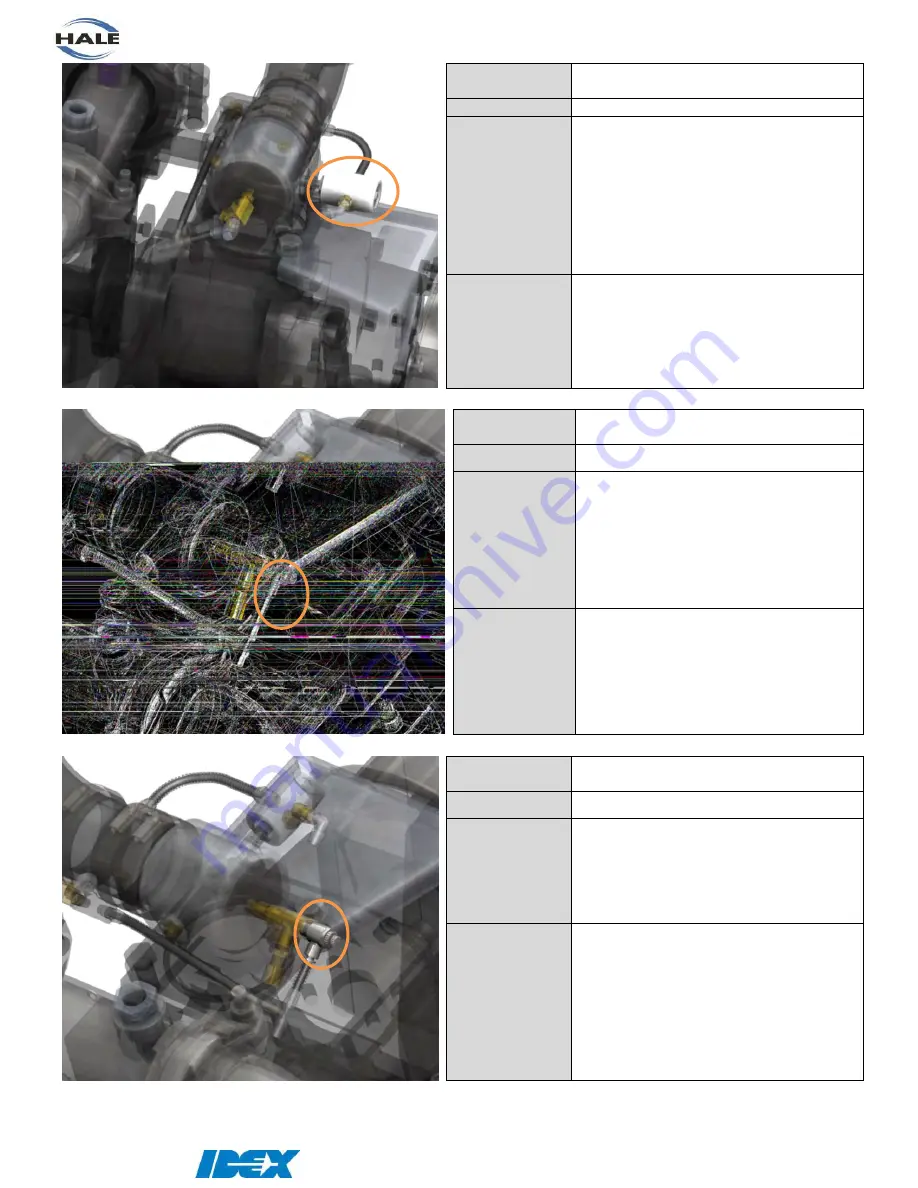
Page
109
of
116
©HALE PRODUCTS, INC. Our policy is one of continuous development. We therefore
reserve the right to amend specifications without notice or obligation.
PART
NUMBER
038-1560-00-0
DESCRIPTION
Blow Down Valve
OPERATION
Releases built up pressure in air system.
Air pressure is supplied from the oil
separator and the air intake. If they don’t
match the valve opens connection from
the oil separator to atmosphere
POSSIBLE
FAULT
•
Air leaks
o
Valve is bad
o
Fittings are loose
PART
NUMBER
038-00071-001
DESCRIPTION
Air Relief Valve
OPERATION
This valve relieves pressure from the
control side of the air intake valve. Any
pressure above the required pressure to
close the air intake valve will be released.
This improves the tracking speed for the
pressure match, especially when
reducing water pressure.
POSSIBLE
FAULT
•
Pressure isn’t matching
o
Relief pressure is set too low.
Tighten to increase relief
pressure.
•
Air leaks
o
O-ring/Seal is bad
PART
NUMBER
70141
DESCRIPTION
Air Intake Control Needle Valve
OPERATION
This valve controls the amount of air
pressure limiting the air intake. The larger
the air pressure the lower the air flow into
the compressor. It also dampens the
response of the air intake plunger.
POSSIBLE
FAULT
•
Air/Water tracking is not steady
o
Needle valve is open too far.
•
Air/Water tracking is too slow when
changing water pressure
o
Needle valve is closed too far.
Содержание HALE SmartCAFS
Страница 106: ......