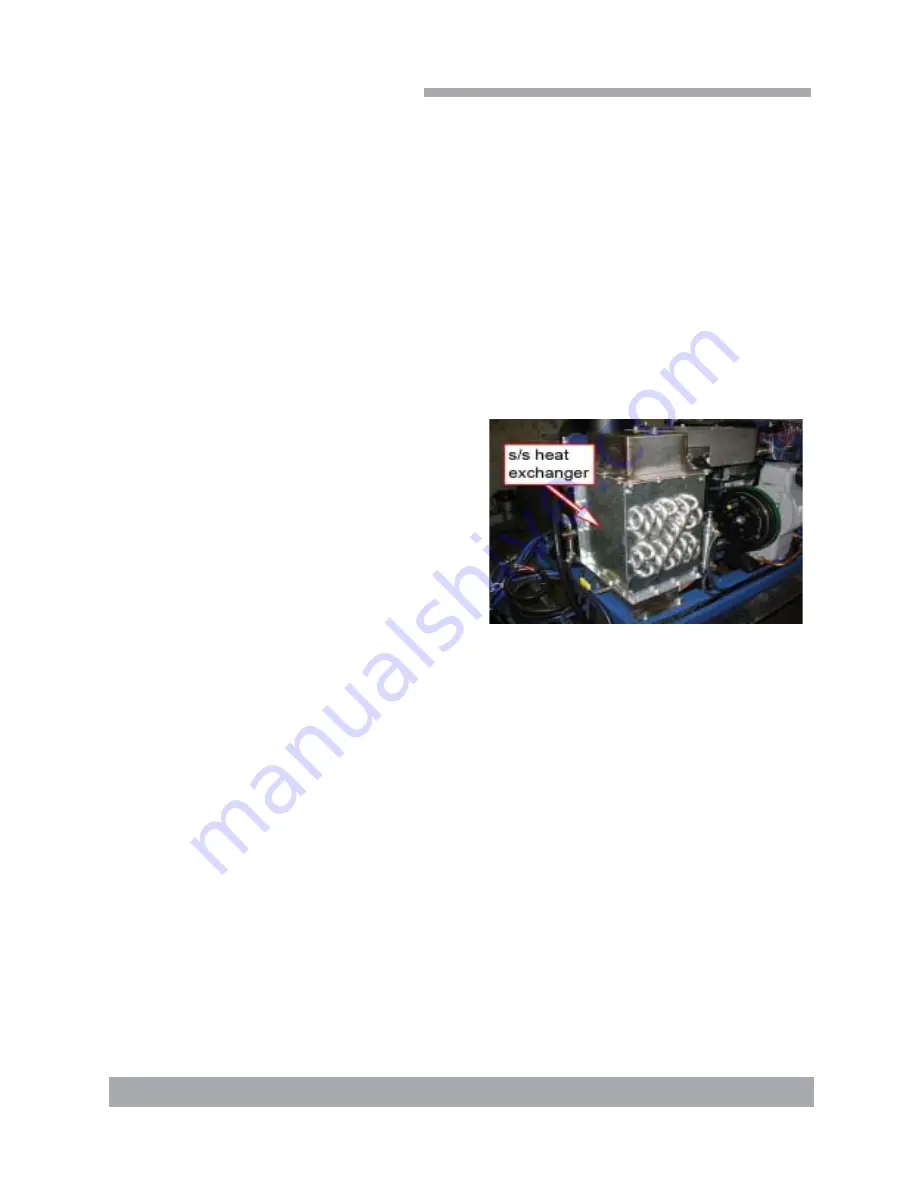
Page 9-1 : CTS 330 Owner’s Manual
Hot Carbonating Truckmount System
CTS 330
Water and Chemical System
Chemical Flow Operation
The engine, vacuum pump, air compressor, drive system, and heat exchanger are the
primary components of the cleaning system. The objective of this system is to move
cleaning solution from the solution tank
to the surface in need of cleaning, and
eventually back to the recovery tank. The first part of this process is to move the
cleaning solution out of the solution tanks. This is accomplished by pressurizing the
solution tanks with the air compressor. The compressed air pushes the solution out of
the tanks and through hoses to the orifice.
The orifice regulates the flow of the cleaning
solution. The solution then flows through the
heat exchange system into the outlet manifold.
The outlet manifold contains a solution valve,
pop off valve, and solution outlet. If the wand
trigger is in use and the solution is at the
desired temperature, the chemical solution will
flow through the solution outlet. The solution
valve and the pop off valve send the solution to
the recovery tank.
The heat exchange system (
Figure 5
) elevates the cleaning solution to the desired
temperature. This system is comprised of two main components: The components are
the engine/blower exhaust heat exchanger and the diverter valve system. The engine/
blower exhaust heat exchanger is a cross-flow heat exchanger; solution flows through
the stainless steel tubes which flows the mixed exhaust along the outside.
The heating process begins when the mixed exhaust flows through the heat exchanger.
The cleaning solution is heated by the mixed exhaust as it flows through the coils of the
heat exchanger. Once the cleaning solution has passed through the heat exchanger
the flow is directed to the outlet manifold then to the cleaning tool.
The
compressor valve
’s purpose is to manually relieve the system of compressed air.
This is done in situations such as removing the lids on the solution tanks.
Figure 9-1
Содержание CTS 330
Страница 2: ......
Страница 23: ...Page 1 15 CTS 330 Owner s Manual CTS 330Hot Carbonating Truckmount System Figure 1 4 Hard Water Map...
Страница 93: ...Page 9 5 CTS Owner s Manual CTS 330Hot Carbonating Truckmount System...
Страница 137: ...40 NOTES...
Страница 142: ......
Страница 143: ......
Страница 144: ......
Страница 145: ......
Страница 146: ......
Страница 147: ......
Страница 148: ......
Страница 149: ......
Страница 150: ......
Страница 151: ......