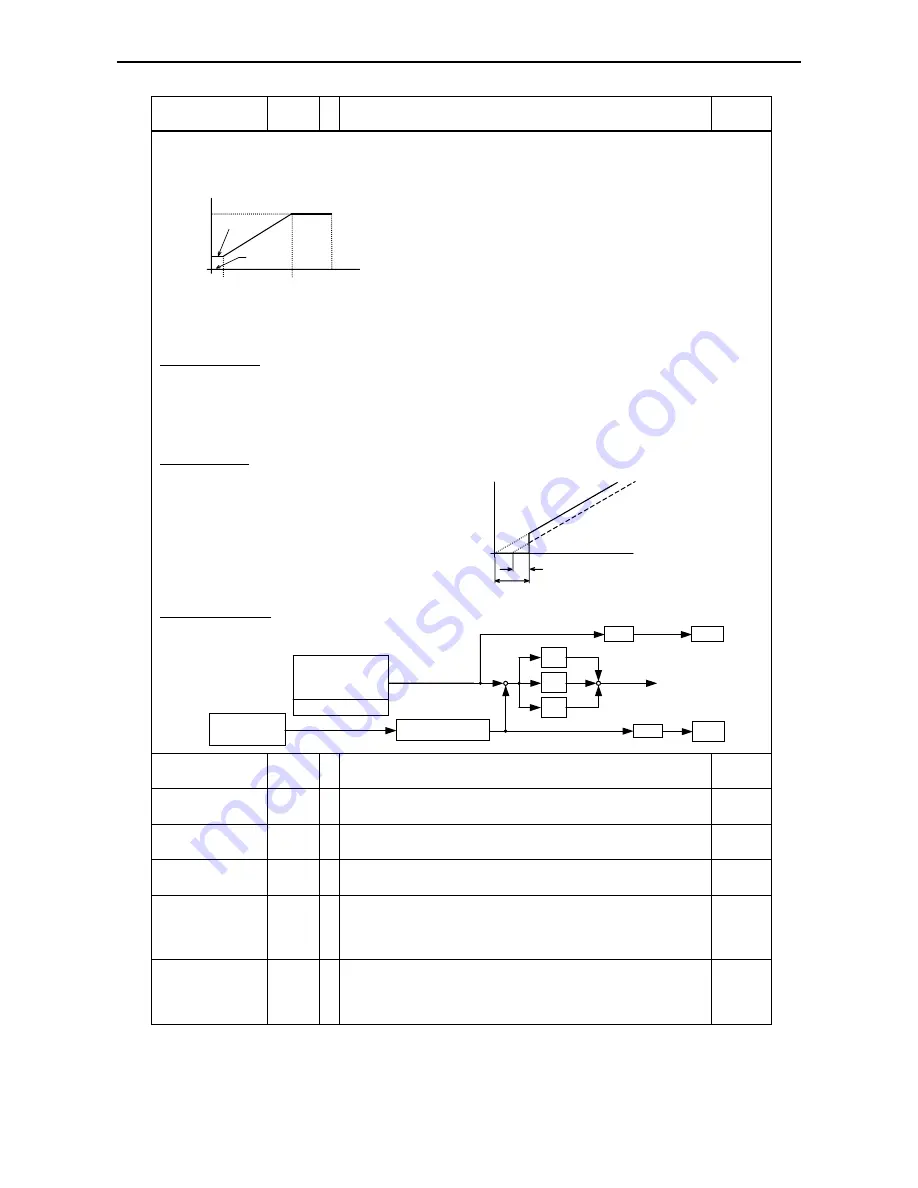
Chapter 8 – Using the digital operator
8-8
Function Display
*
)
Function description / parameter setting range
Standard
setting
(C
ontinued from previous page
)
control is not used, in this case it is really the set value that gets adjusted. So when the PID control is activated, the
functions
A 11
through
A 14
do not adjust the set value but the actual value instead).
f
A 12
x axis:
Voltage or current
actual
value into analog input (when PID control is used)
Voltage or current
set
value into analog input (when PID control is not used)
A 11
20mA
A 14
A 13
0V
4mA
10V
A 15
= 01
A 15
= 00
The parameters of functions
A 11
through
A 14
are changed from Hz to % due to the PID control’s activation (done
using
A 71
) and to engineering units by setting function
A 75
. For this reason, function
A 71
must be set to 01
before
the other functions are configured.
Displayed values
Function
d 04
enables the display of the actual value while
F 01
enables the display of the set value. These values can
be displayed in engineering units by setting function
A 75
.
When function
F 01
is activated the PID set value will be displayed, but there is no permanent update of the displayed
value. When function
d 04
is activated the actual value will be displayed which in contrast to the set value does get
permanently updated.
P, I and D gain
Control output
jump response
0
t
T
N
T
N*
T
N
: Set readjustment
time (kp = 1)
T
N*
: Effective readjust-
ment time (kp = 0,5)
Although these gains can be set independently of each
other, there are interactions between them. When the P
gain (k
p
) is changed, the effective I gain changes (T
N*
)
also. Only when k
p
=
1, the effective I gain (T
N*
) is equal
to the I gain that had been entered (T
N
). When k
p
is not
equal to 1, T
N*
can be calculated as follows:
T
N*
= T
N
*
k
p
(refer to the figure on the right).
PID block diagram
P
A 72
I
A 73
D
A 74
+
+
+
F 01
+
Monitor
d 04
-
A 75
Analog set value adjustm.
A 11
through
A 14
Set value input:
settable using
A 76
(terminals O or OI)
Set value (set under
A 01
):
- Digital operator pot
- Entry using
F 01
- Terminal O or OI
-
Multistage frequencies
A 75
Output frequency
PID control
active / not active
A 71
N
00: PID control is not used (not active)
01: PID control is used (active)
00
P (proportional) gain
of PID control
A 72
Y
The proportional gain of PID control can be set in the range of
0.2 through 5.0.
1.0
I (integral) gain
of PID control
A 73
Y
The integral gain of PID control can be set in the range of 0.0s
through 150s.
1.0
D (differential) gain
of PID control
A 74
Y
The differential gain of PID control can be set in the range of 0.0s
through 100s.
0.0
Scale conversion
of PID control
A 75
N
The set value or actual value to be displayed on the LED display can
be multiplied by a factor in the range of 0.01 through 99.99 so that
engineering units (e.g. flow or throughput) can be displayed instead
of the frequency.
1.00
Feedback signal
location
A 76
N
The set value can be fed into one of two different analog inputs:
00: analog input OI
01: analog input O
(The set value can also be set using the potentiometer or the multistage
frequencies).
00
Содержание L100 IP Series
Страница 2: ......
Страница 14: ...Chapter 2 Inspection upon unpacking 2 2 ...
Страница 16: ...Chapter 3 Appearance and names of parts 3 2 ...
Страница 46: ...Chapter 7 Control circuit terminal functions 7 18 ...
Страница 74: ......
Страница 84: ......