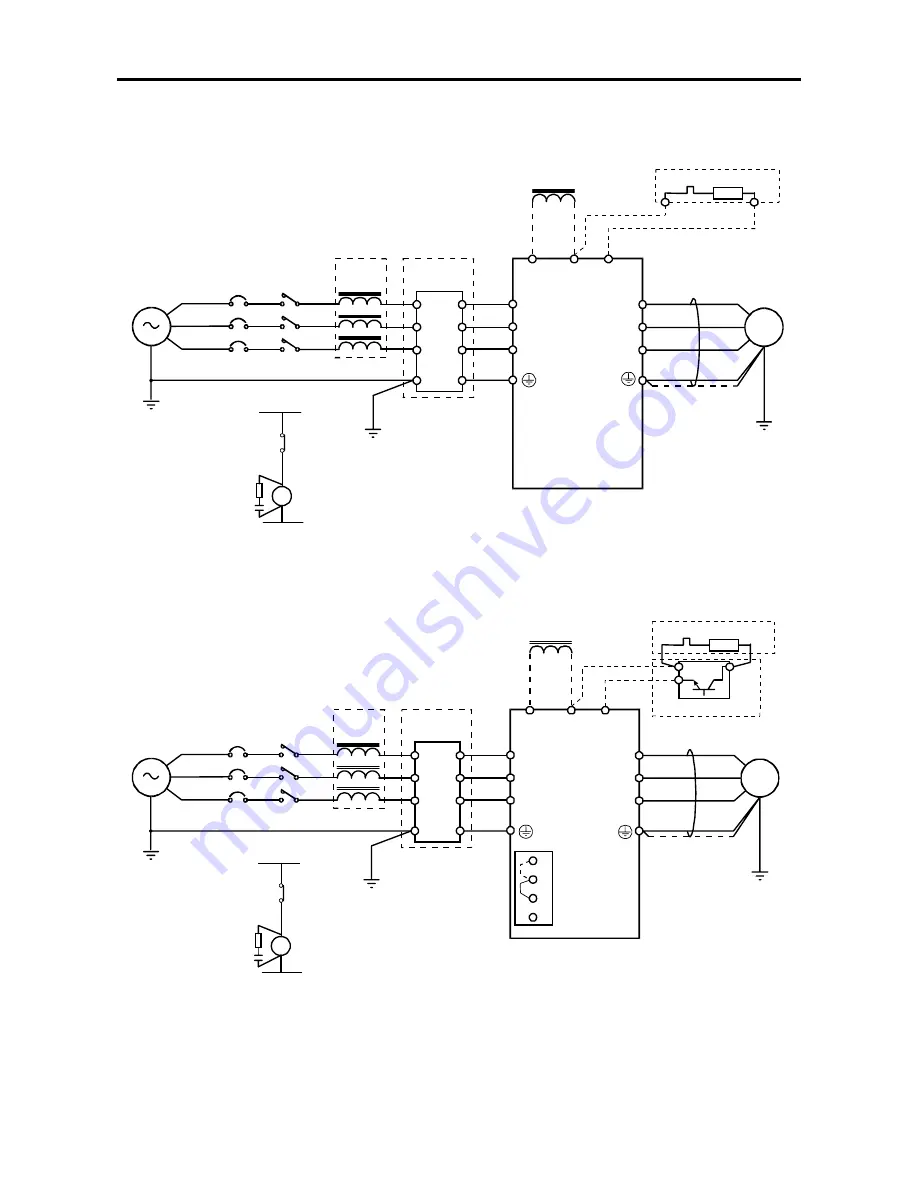
2. Installation and Wiring
2-4
Main circuit wiring
a)
N07K5S, X07K5S and smaller units
For DC Drives (main option “D”), check Chapter 7-2.
U
D C L
N o te 1 3 )
N o t e 11
N o t e 9 )
N o t e 1 )
N o te 8 )
N o te 1 0 )
N o te 9 )
N o te 7 )
VAT 20 00
D B R R es is to r
7 6D
L 1
L +1
L +2
B
L 2
M C
A C L
N o is e F ilte r
M C C B
L 3
V
W
P o w er S u pp ly
3 80 -46 0V
5 0/6 0 H z
M C
N o te 1 3 ) 7 6 D
N o te 1 4 )
N o te 2 )
N o te 6 )
N o te 5 )
N o te 6 )
N o te 7 )
N o te 3 )
x
M
1
2
4
5
6
E
3
E
b) N11K0S, X11K0S and larger units
For DC Drives (main option “D”), check Chapter 7-2.
U
D C L
D BR U nit
N o te 1 3 )
N o te 1 2 )
N o t e 1 1 )
N o t e 9 )
N o t e 4 )
N o t e 1 )
N o te 8 )
N o te 1 0 )
N o te 9 )
N o te 7 )
VAT20 00
D BR R es is to r
L 1
L +1
L +2
L -
L 2
M C
A C L
N o is e Filte r
M C C B
L 3
V
W
1
2
3
4
4 15 -48 0V
3 80 -40 0V
P o w er S u pply
3 80 -46 0V
5 0/6 0 H z
M C
N o te 1 2 ) 7 6 D
N o te 1 4 )
N o te 2 )
N o te 6 )
N o te 5 )
N o te 6 )
N o te 7 )
N o te 3 )
x
M
1
2
4
5
6
E
3
E
Fig. 2.4 Example of main circuit wiring