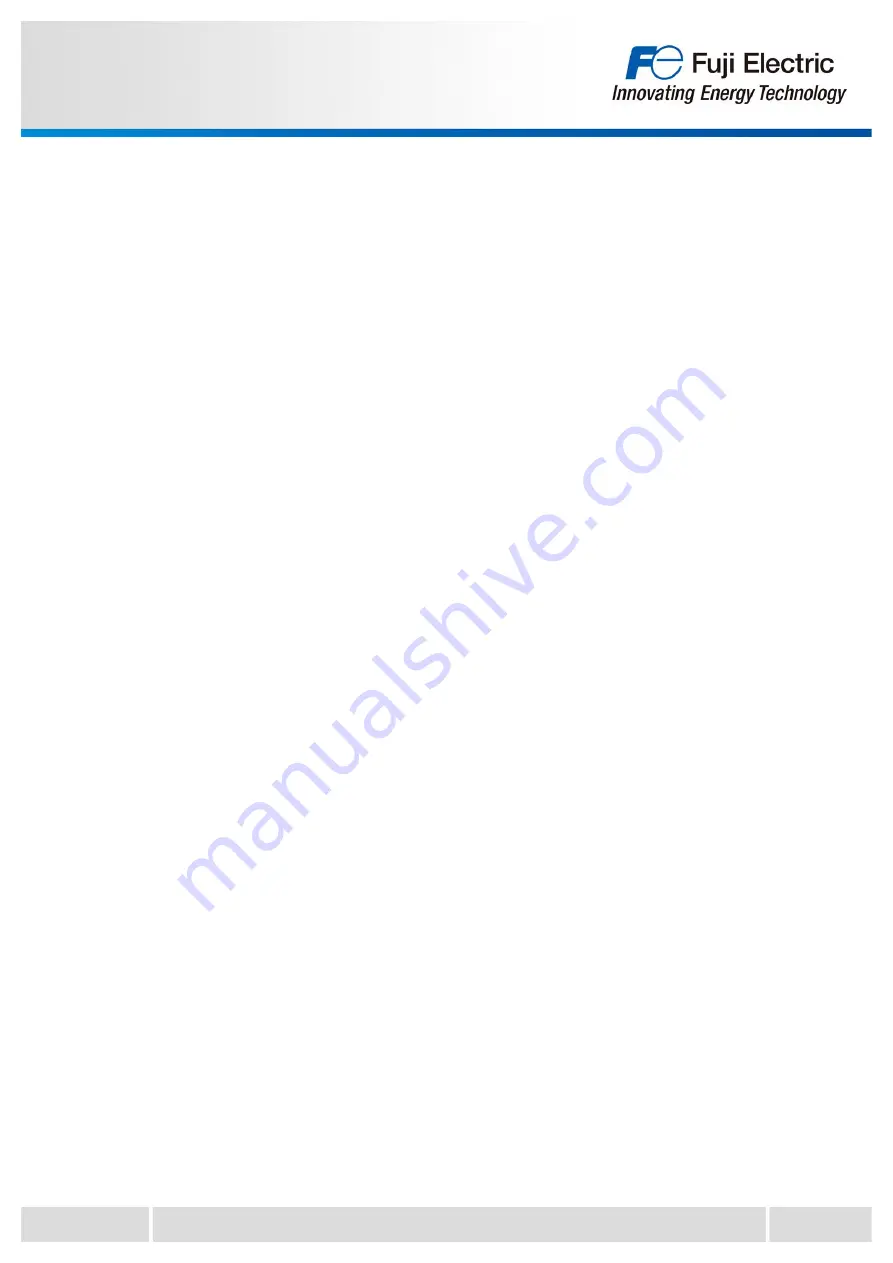
MT6M15962a
3. 第7世代RC-IGBTチップの特徴
© Fuji Electric Co., Ltd. All rights reserved.
5.2 Precautions for mounting procedure
①
Reduce the contact thermal resistance as much as possible between the IPM and the heat sink by
applying thermal grease. (See Chapter 5, Section 3.)
②
Use appropriate length of screws. The package may be damaged if the screw length is longer than
the screw hole depth. (See Chapter 1, Section 5.)
③
Tightening torque and heat sink flatness should be within the range of specified values.
Wrong handling may cause an insulation breakdown. (See Chapter 5, Section 2.)
④
Do not apply excessive weight to the IPM.
Do not apply deforming forces to the lid. If pushing force is applied to the lid, the internal circuit may
be damaged. If pulling force is applied to the lid, it may come off. Do not bend the control terminals.
⑤
Do not apply reflow soldering to the main terminals or control terminals. In addition, be careful so
that heat, flux and cleaners for other products do not affect the IPM.
⑥
Avoid places where corrosive gases are generated or where there is an excessive dust.
⑦
Avoid applying static electricity to main terminals and control terminals of the IPM.
⑧
Please confirm that the
V
CC
is 0V before mounting/dismounting the control circuits to/from the IPM.
⑨
Do not make the following connections outside of the IPM:
Control terminal GNDU and main terminal U
Control terminal GNDV and main terminal V
Control terminal GNDW and main terminal W
Control terminal GND and main terminal N (N1, N2 in case of P631)
It may cause malfunction.
⑩
If the IPM is used in a single phase, or if the brake is not used in a built-in brake type, supply the
control power to the unused phases as well. Supply the control power and pull up both input
terminal (
V
in
) and alarm output terminal (ALM) to
V
CC
. If the control power supply is turned on while
the input terminal (
V
in
) is open, the alarm output state will occur.
⑪
If the warning function is not used, it is recommended that the warning pin be left open. If the
warning pin is pulled up to
V
CC
, the current consumption by
V
CC
/
R
WNG
increases during warning
operation; thus design the control power supply properly. Pulling down the warning pin to GND is
not recommended, as a current of about 200uA always flows from the control IC.
⑫
The alarm output is output with different pulse width depending on the protection factor. (See
Chapter 3, Section 2.)
The alarm output time on the secondary side of the optocoupler for alarms must be designed in
consideration of the delay time of the optocoupler and peripheral circuits..
⑬
The IPM cannot be used in parallel because each IPM has its own driving and protection circuits. If
they are operated in parallel, the current may concentrate in a specific IPM and destroy it because
of the difference in switching time or the timing of protection..
⑭
The case material meets the standard UL 94V-0, but is not non-flammable.
⑮
The surface temperature of the lid should not exceed the heatproof temperature during soldering. If
the solder touches the lid, it may be deformed or the solder may adhere.
⑯
Our IPM is designed for inverter applications. Application to converters requires thorough
verification. Please contact us if it is used for converter.
⑰
The brake section is designed on the assumption that resistance load is applied. Please contact us
if it is used for inductor load or boost circuit, etc.
6-8