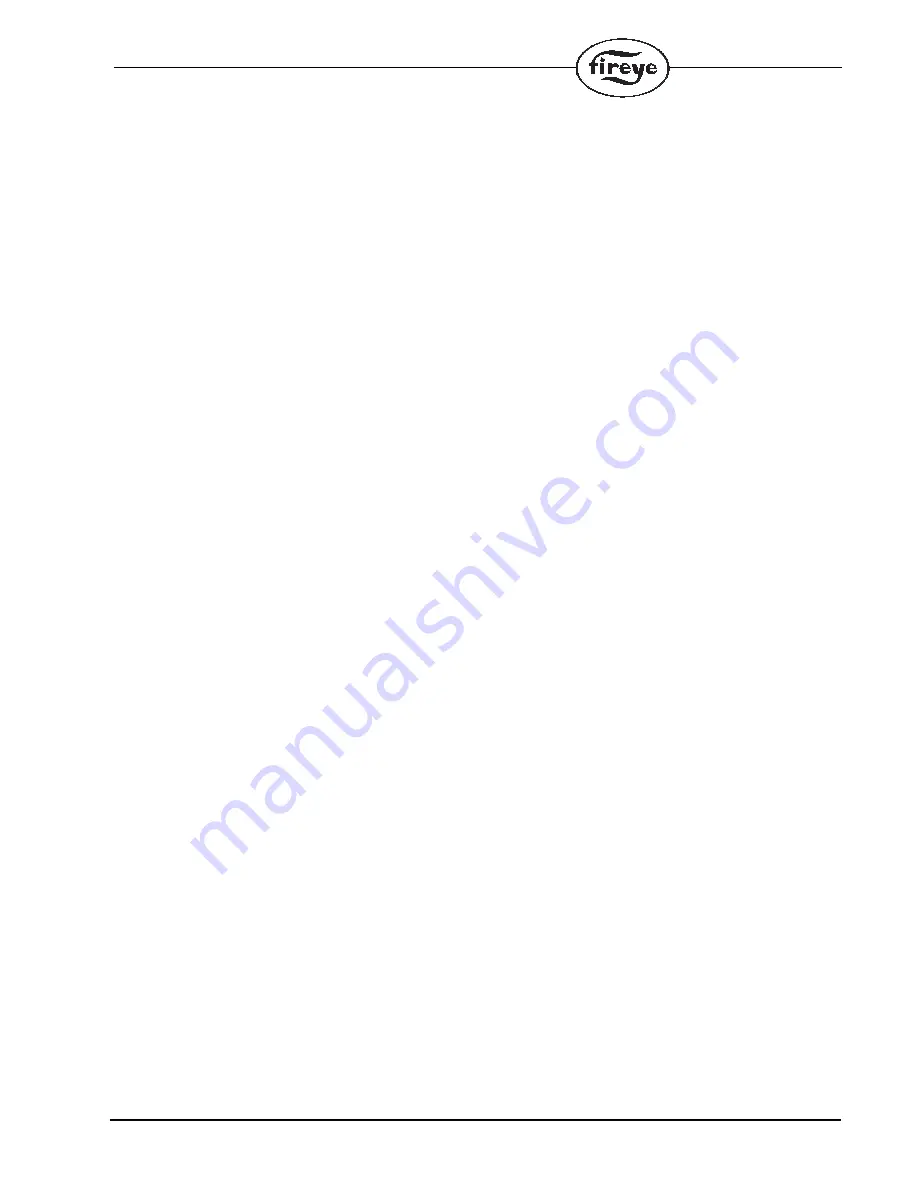
39
b. Integral is the time between error corrections or updates to the VFD. A high rate of updates
(short integral time) to the VFD can result in unstable operation. Conversely too few updates
(long integral time) to the VFD can result in large deviations from setpoint. Update time to the
VFD output is done at ¼ second intervals. The range of value for INTEGRAL is 0 to 100 in
increments of 0.1 with a default of 0.0. The lower the setting, the shorter the integration time
will be. The default setting of 0.0 will inhibit integration. A setting of 100.0 will have the lon-
gest integration time.
NOTE: using the default values, the VFD should never overshoot its target. If overshooting
is observed, the VFD drive is using its own PID control. If the user wishes to use the VFD's
PID control, the user must set the PPC4000's VFD RUN MODE to MANUAL to disable
the PID control. Either the VFD Drive or the PPC4000 can use PID control, not both.
Before the user attempts commissioning, the PID control of the VFD system must be set
properly or the commissioning process will be very difficult and time consuming waiting
for the VFD to stabilize.
7.
Tolerance is the acceptable error in feedback signal received from the VFD. Feedback signal can be
the VFD’s analog 4-20 mA of encoder pulses. Both feedback types are normalized to a range of 0 -
1000. Tolerance is expressed in terms of percentage of current feedback reading. A LOW tolerance
requires the positioning error to be less than 4% of setpoint over a 30 second period. A HIGH toler-
ance requires the positioning error be less than 6% of setpoint over a 15 second period. Lockout
occurs if the tolerance level is exceeded. Default is HIGH.
8.
The ACCELeration / DECELeration time is the time required to move from minimum (0 Hz) to max-
imum (60 Hz) and from maximum to minimum speeds. The default value is 30 seconds and has a
range of 0-255 seconds. With ACCEL and DECEL specified the rate of change of the 4-20 mA out-
put is based on this time. During the accel/decel period, the VFD is allowed to move to its next posi-
tion and not be checked for errors until the time has expired.
9.
When using flame safeguard controls that require the air flow switch to be proved open before the
start of a cycle, the VFD must be nearly stopped before the air flow switch may open. The STOP
TIME parameter is the amount of time the PPC4000 will wait between cycles before closing the
OCRC relay, allowing large motors to fully coast to a stop. User can adjust STOP TIME between 0
and 100s, with 1s increments. The default value for STOP TIME is 0 seconds.
10. Shows the current position during a burner cycle, of the VFD in units specified by DISPLAY FOR-
MAT. Unlike a servo, the VFD position cannot be adjusted or displayed properly in standby. Manual
adjustment of the position is prohibited during a burner cycle.
ENCODER INPUT
1.
The encoder inputs on the NXCESVFD plug-in board are designed to use an encoder that provides
an open collector output. The encoder input of the NXCESVFD is a 2.4 Kohm pull-up resistor inter-
nally connected to 24 vdc. The encoder selected must be able to handle 10 mA.
2.
The PPC4000 tolerates maximum encoder counts over a range of 300 to 5000 counts per second. For
a motor with a maximum RPM of 1750, the range of encoder would be 12 to 150 counts per revolu-
tion. Likewise for a motor with a maximum RPM of 3600, the range of encoder would be 5 to 80
counts per revolution.
3.
Shielded cable should be used to connect the encoder output to the NXCESVFD. The drain wire
must be connected to the EARTH post.
Operational Notes:
1.
Consult the VFD manual for adapting, connecting and configuring the VFD to the combustion
blower motor. Be sure all inputs and outputs are compatible with the PPC4000 and NXCESVFD.
2.
The VFD is commissioned like any of the servo motors and must have a position for every setpoint
for the commissioned profile.
3.
For a VFD channel to be used as a VFD controller, the ANALOG OUT SETUP value for that VFD
channel must be set to UNUSED. Only then will the VFD channel be displayed in the servo setup
sub menu where the user selects that particular VFD channel and configures it for operation.