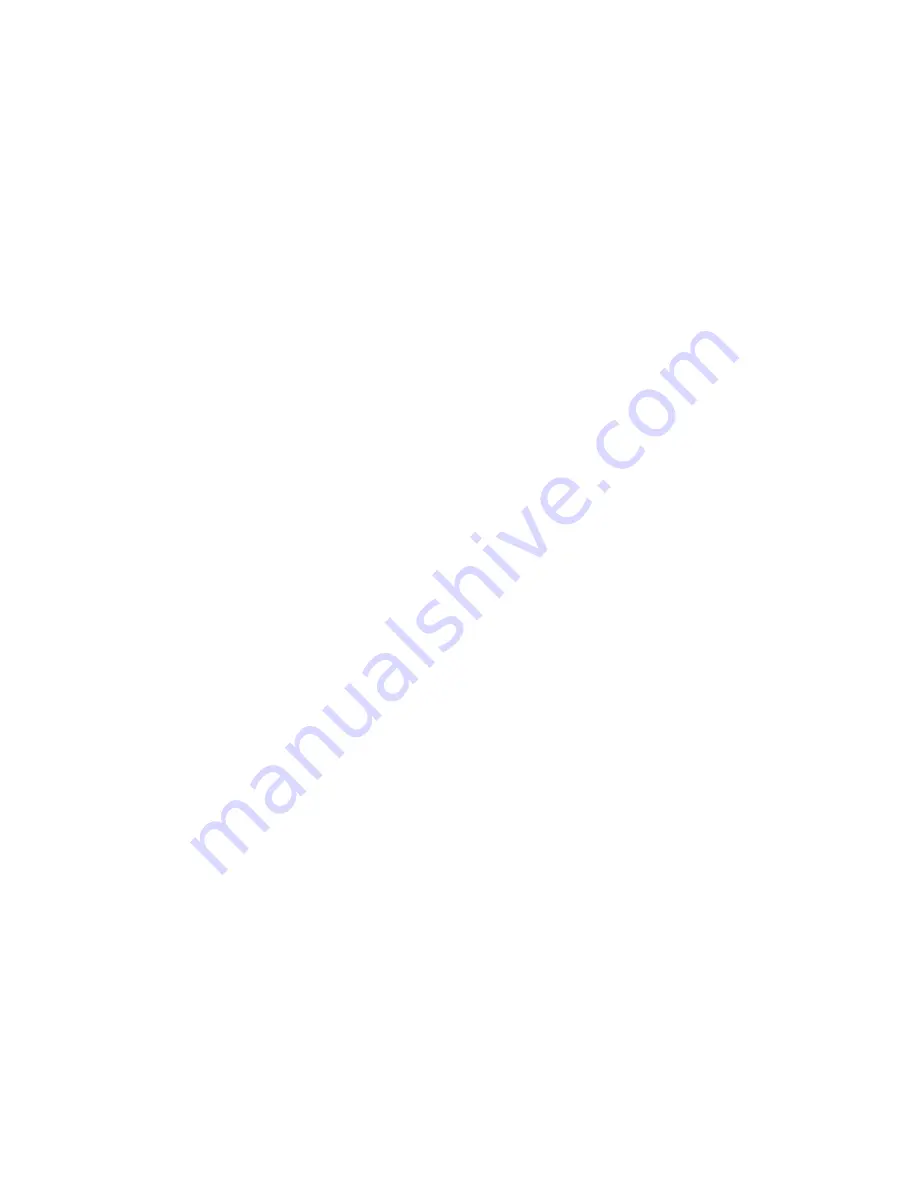
4.6
Theory
of
Operation
4.6.1
Process
Flow
Description
Water
enters
the
SWS
housing
by
means
of
the
Manual
Water
Pump
or
a
pressurized
water
source.
As
water
flows
through
the
SWS,
calcium,
magnesium
and
other
contaminants
are
removed.
Water
collects
in
the
WRS
Water
Tank.
This
tank
is
equipped
with
a
Liquid
Level
Switch
(LS
‐
1,
normally
closed)
that
will
not
allow
the
Pump
to
operate
should
the
water
reach
a
critically
low
level.
When
the
user
needs
to
pump
water
from
the
WRS
up
into
the
SMU
Jacket
(Boiler),
the
user
depresses
the
Fill
Switch
(SW2),
which
activates
the
Pump.
The
Recirculation
Valve
(SV
‐
6,
normally
open)
closes
and
the
Fill
Valve
(SV
‐
5,
normally
closed)
opens
to
allow
the
water
to
flow
from
the
WRS
Water
Tank
through
the
blue
‐
tagged
hose
into
the
SMU
Jacket.
The
Jacket
is
equipped
with
a
Liquid
Level
Switch
(FS
‐
1,
normally
opened)
which
prevents
the
immersion
heater
elements
from
being
energized
if
there
is
not
enough
water
in
the
Jacket.
In
addition,
as
a
secondary
safeguard,
the
unit
is
equipped
with
a
High
Temperature
Limit
Switch
(HTS
‐
1,
normally
opened)
to
turn
OFF
power
to
the
heaters
and
PLC.
Once
the
user
has
pumped
a
sufficient
amount
of
water
into
the
Jacket,
the
Liquid
Level
Switch
closes,
allowing
the
SMU
to
operate
and
the
immersion
heater
elements
to
turn
ON/OFF
by
means
of
the
programmable
logic
controller
(PLC).
As
heat
is
supplied
to
the
water
in
the
Jacket,
steam
is
generated
and
the
pressure
and
temperature
in
the
Jacket
rises.
The
Jacket
Pressure
Transmitter
(PT
‐
1)
supplies
pressure
data
to
allow
the
PLC
to
control
the
Jacket
at
a
steady
pressure
set
point
when
the
Jacket
is
in
pressure
control
(during
idle
and
certain
phases
of
a
cycle).
The
Door
Switch
(DS
‐
1,
normally
open)
will
not
allow
a
cycle
to
start
(and
steam
to
flow
into
the
chamber)
unless
the
door
is
closed
and
latched.
When
a
cycle
is
started
and
steam
is
required
in
the
Chamber,
the
Sterilize
Valve
(SV
‐
1)
is
opened
by
the
PLC
to
allow
steam
from
the
Jacket
to
flow
into
the
Chamber.
During
the
conditioning
phase
of
a
cycle,
the
Chamber
Pressure
Transmitter
(PT
‐
2)
supplies
pressure
data
to
the
PLC
to
allow
it
to
pressurize
or
pull
a
vacuum
in
the
Chamber
to
specific
set
points.
When
steam
condenses
during
a
cycle,
it
flows
through
the
chamber
drain,
past
the
Chamber
Temperature
Sensors
(RTD
‐
1
&
RTD
‐
2),
through
the
red
‐
tagged
hose,
and
finally
through
the
WRS
Steam
Trap
back
into
the
Water
Tank.
The
Chamber
Temperature
Sensors
provide
temperature
data
to
allow
the
PLC
to
control
the
heater
elements
and
maintain
the
Chamber
at
a
steady
temperature
set
point
when
the
P2131
is
in
temperature
control
(during
the
heat
‐
up
and
exposure
phases
of
a
cycle).
The
Steam
Trap
allows
cool
condensate
to
pass
through
to
the
WRS
Water
Tank
but
prevents
the
flow
of
steam.
During
the
conditioning
phase
and
the
vent
phase
of
a
cycle,
steam
and/or
air
is
evacuated
from
the
Chamber.
The
PLC
evacuates
the
Chamber
by
opening
the
Vacuum/Exhaust
Valve
(SV
‐
2),
allowing
a
venturi
vacuum
Eductor
to
pull
the
steam
and/or
air
from
the
Chamber
into
the
WRS
via
the
white
‐
tagged
Vacuum/Exhaust
hose.
The
steam/air
is
entrained
in
the
water
that
flows
through
the
Eductor
back
into
the
WRS
Water
Tank.
There
are
several
cycles
on
the
P2131
that
require
a
drying
phase
after
exposure.
Since
a
vacuum
facilitates
faster
drying,
the
PLC
pulls
a
vacuum
on
the
Chamber
by
opening
the
Vacuum/Exhaust
Valve
for
the
duration
of
the
dry
phase.
After
the
dry
phase,
the
PLC
will
equalize
the
pressure
by
opening
the
Vacuum
Break
Valves
(SV
‐
3/4)
to
allow
outside
air
to
be
drawn
through
a
HEPA
filter
into
the
Chamber.
Once
the
Chamber
Pressure
Transmitter
detects
equalized
pressure
between
the
Chamber
and
outside
environment,
the
PLC
closes
the
Vacuum
Break
Valves,
allowing
the
Chamber
Door
to
be
opened.
116
Содержание P2131
Страница 121: ... THIS PAGE INTENTIONALLY LEFT BLANK 115 ...
Страница 130: ...SECTION A APPENDIX 124 ...
Страница 131: ...A 1 Swagelok Fitting Installation Instructions 125 ...
Страница 135: ...A 2 PLC Data Sheet 129 ...
Страница 141: ...A 3 VERIFY Product Information 135 ...
Страница 147: ...A 4 WRS Pump Information 141 ...
Страница 158: ...A 5 Vacuum Leak Test Troubleshooting Guide 152 ...