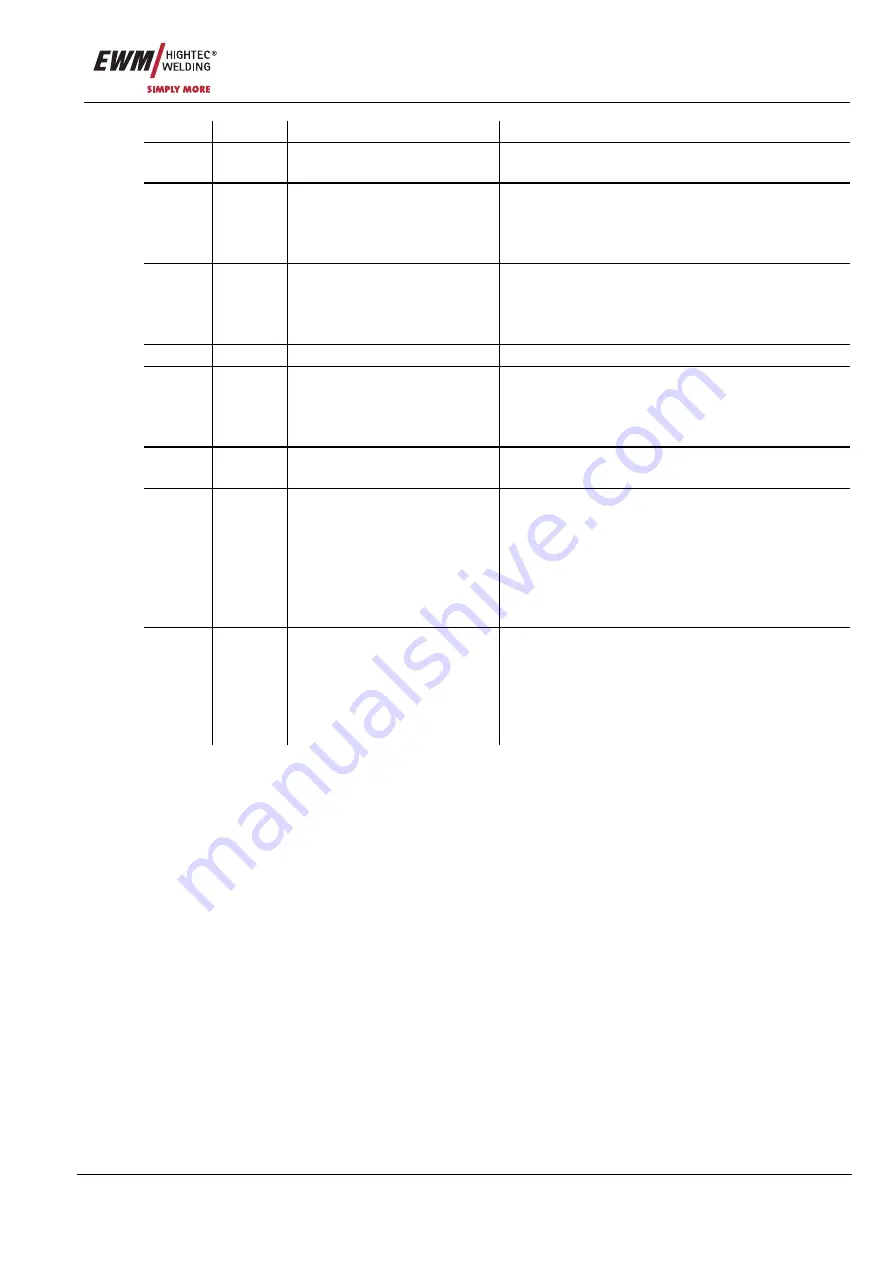
Profiles for PHOENIX MIG/MAG systems
Profiles for the CANopen module
Item No.: 099-008225-EWM01
45
Rx-PDO 1
Cob ID = 200h + address
Byte
no.
Bit no.
Function
Description
1 4 Position
search
Bit allocation:
0
1
Activates the position search function for the
workpiece
Position search off
Position search on
1 5 Blow-out
Bit allocation:
0
1
Manual check via the blow-out valve
Blow-out valve off
Blow-out valve on
1 6 Reserved
1
7
WF switching (optional)
Bit allocation:
0
1
Switches over between two wire feed units
Wire feed unit 1 is active
Wire feed unit 2 is active
2
0-7
JOB number specification
Select a JOB number in the range of
1-255
3 0-3
4-6
7
Program number specification
Not allocated
Welding simulation
Bit allocation:
0
1
Select a program number in the range 0-15
Welding simulation switched off
Welding simulation activated
4
0
Specification of master power
source with TANDEM
systems (optional)
Bit allocation:
0
1
Activates the master/slave power source in a
TANDEM system
System adopts slave function
System adopts master function