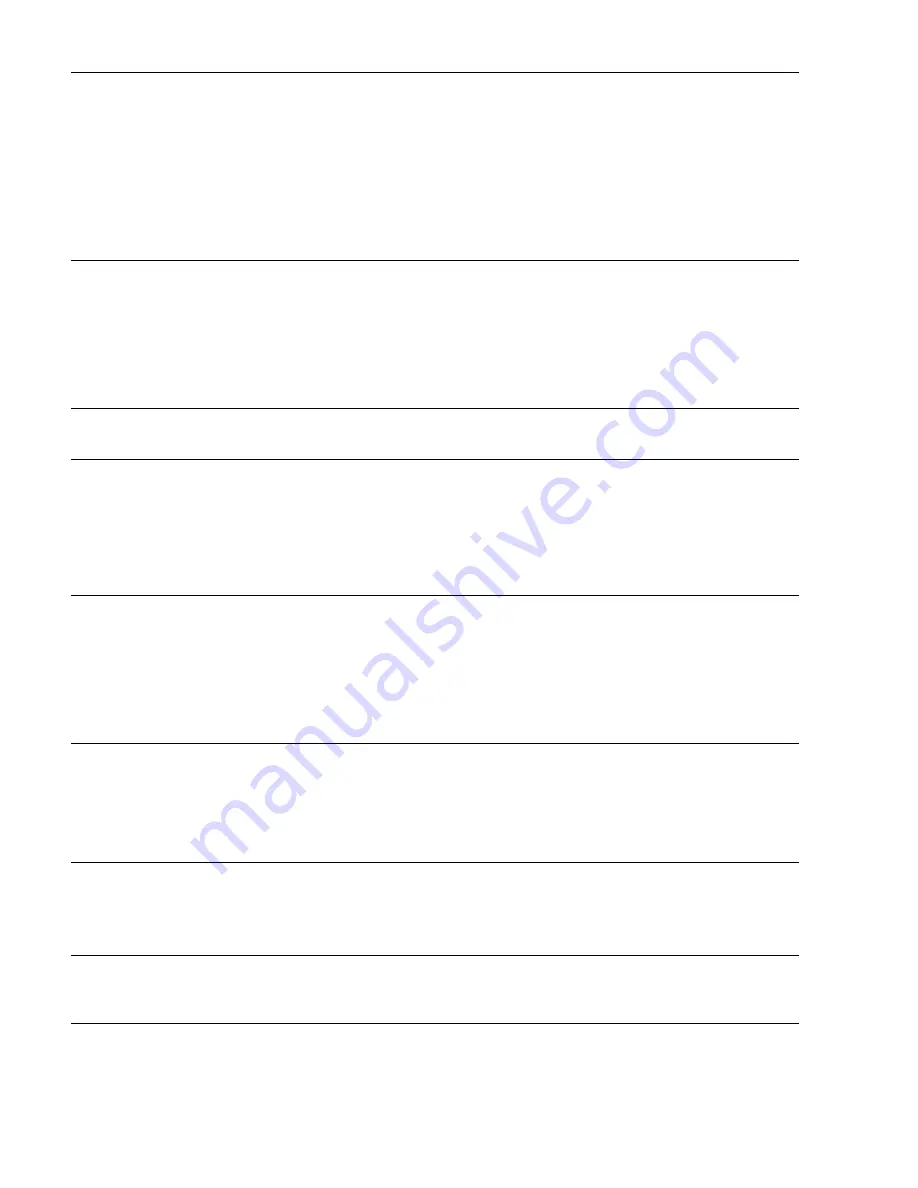
Technical data
Micropilot M FMR 240 with PROFIBUS PA
96
E Hauser
10
Technical data
10.1
Additional technical data
10.1.1
Input
Measured variable
The measured variable is the distance between a reference point and a reflective
surface (i.e. medium surface).
The level is calculated based on the tank height entered.
The level can be converted into other units (volume, mass) by means of a linearization.
10.1.2
Output
Output signal
PROFIBUS PA
Signal on alarm
Error information can be accessed via the following interfaces:
•
Local display:
– Error symbol (see Page 35)
– Plain text display
•
Current output
•
Digital interface
Linearization
The linearization function of the Micropilot M allows the conversion of the measured
value into any unit of length or volume. Linearization tables for calculating the volume in
cylindrical tanks are pre-programmed. Other tables of up to 32 value pairs can be
entered manually or semi-automatically.
10.1.3
Performance characteristics
Reference operating
conditions
•
temperature = +20 °C (68 °F) ±5 °C (9 °F)
•
pressure = 1013 mbar abs. (14.7 psia) ±20 mbar (0.3 psi)
•
relative humidity (air) = 65 % ±20%
•
ideal reflector
•
no major interference reflections inside the signal beam
Maximum measured error
Typical statements for reference conditions, include linearity, repeatability, and
hysteresis:
•
FMR 240: up to10 m ±3 mm, off10 m ±0,03% of measuring range
Resolution
Digital / analog in % 4…20 mA
•
FMR 240: 1mm / 0.03 % of measuring range
Reaction time
The reaction time depends on the parameter settings (min. 1 s). In case of fast level
changes, the instrument needs the reaction time to indicate the new value.