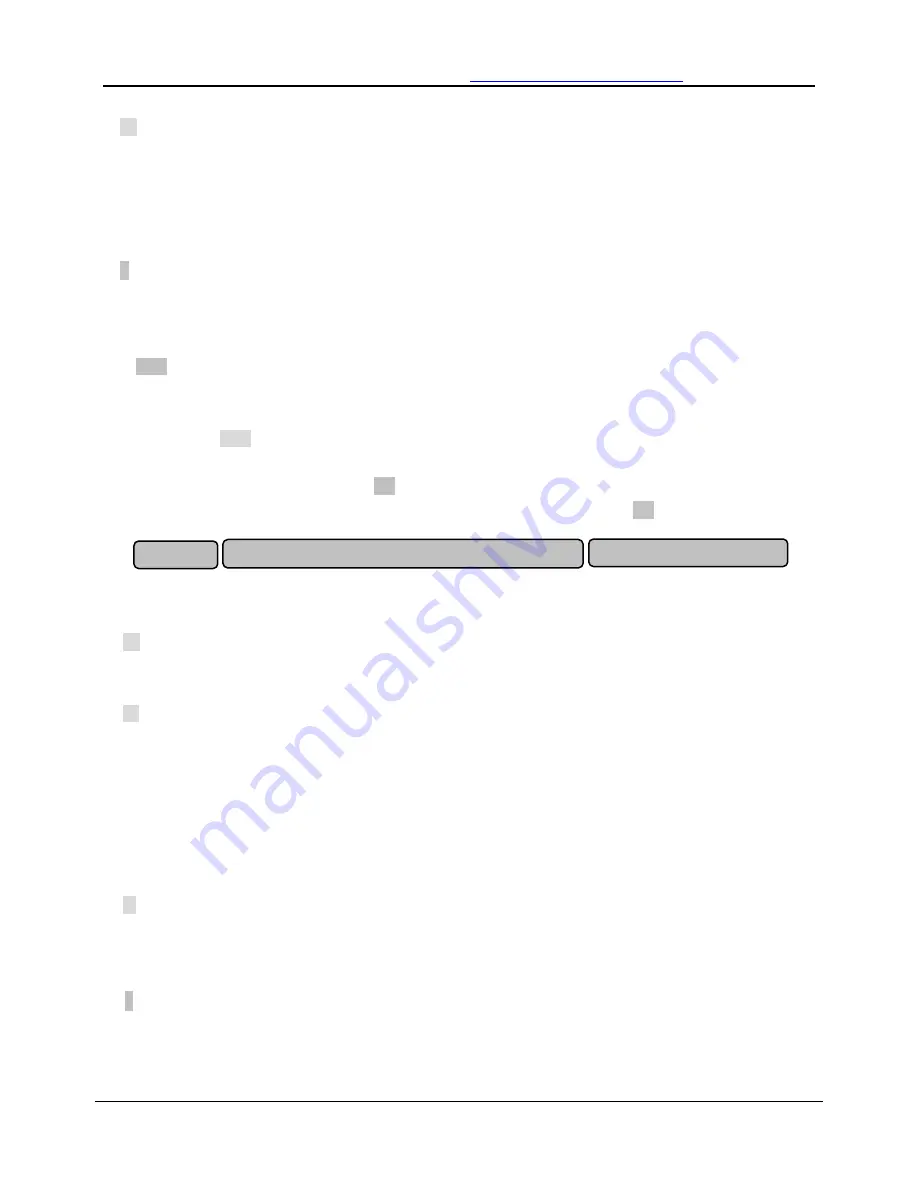
V&T Technologies Co., Ltd.
http://www.ecodrivecn.com
Chapter 6 Parameter Description
63
2: Menu mode of non-leave-factory value function code: The operation panel only displays the
parameters different from the leave-factory values.
When the technical personnel perform onsite maintenance, to quickly view the parameters
set by the user and detect the failure, this mode can be used.
After the inverter commissioning is completed, to conveniently record and inquire the
modified parameters, this mode can be set.
3
:
Menu mode of last changed 10 function codes: When the inverter has abnormal operation or it is
necessary to inquire the commissioning parameters, the last changed 10 parameters can be inquired by
setting this menu mode. When the leave-factory parameters are recovered, the record of the last changed
10 function codes will also be cleared.
Note:
Both P0.00 and P0.02 are visible in all the menu display modes for the convenience of menu
mode switching.
Press ESC key and hold for over 5 seconds, it will restore to basic menu mode, and P0.02 is
automatically restored to 0.
In non-basic menu mode, the >> key cannot be used to switch the function zone code and group
number. The current menu mode will be displayed after pressing the >> key for several times.
This function is used to set the control operation mode of the inverter. 0 ~ 3 indicates vector control 1, 4 ~
7 indicates vector control 2.
Vector control 1 without encoder speed feedback:
0: Process open loop control: It is applicable to most applications, including the application of one
inverter driving one motor and the application of one inverter driving multiple motors (the motors are in
the same work conditions).
1: Analog value feedback process close loop control: It is applicable to applications with general
requirement of speed control precision. The feedback analog can represent such parameters as
temperature, pressure and humidity. For the reference and feedback setting of the analog feedback
process close loop control, refer to P1.02~P1.07 function description. For the setting of the process PID
close loop parameters, refer to Group P8 function code description.
AI1 and AI2 terminal input specification: 0~10V or 0~20mA.
AI3 terminal input specification: -10~10V;
X7/DI terminal input specification: 0~ maximum input pulse frequency P5.10.
2: Single-phase pulse feedback process close loop control: It is applicable to applications with higher
speed control precision, and pulse encoder shall be installed at the motor end or mechanical equipment
axle end. Single-phase pulse feedback channel: X7/DI terminal: The X7/DI terminal function must be set
to process close loop control single-phase pulse input (P5.06=47) .
3
:
Composite control: The composite control of process open loop and analog feedback closed loop is
suitable for special applications.
As for the set frequency of the inverter, if it is necessary to made fine tuning on another physical
parameter in the system in addition to the open loop setting, closed loop adjustment can be made to this
P0.03
Control operation mode
0~7(0)