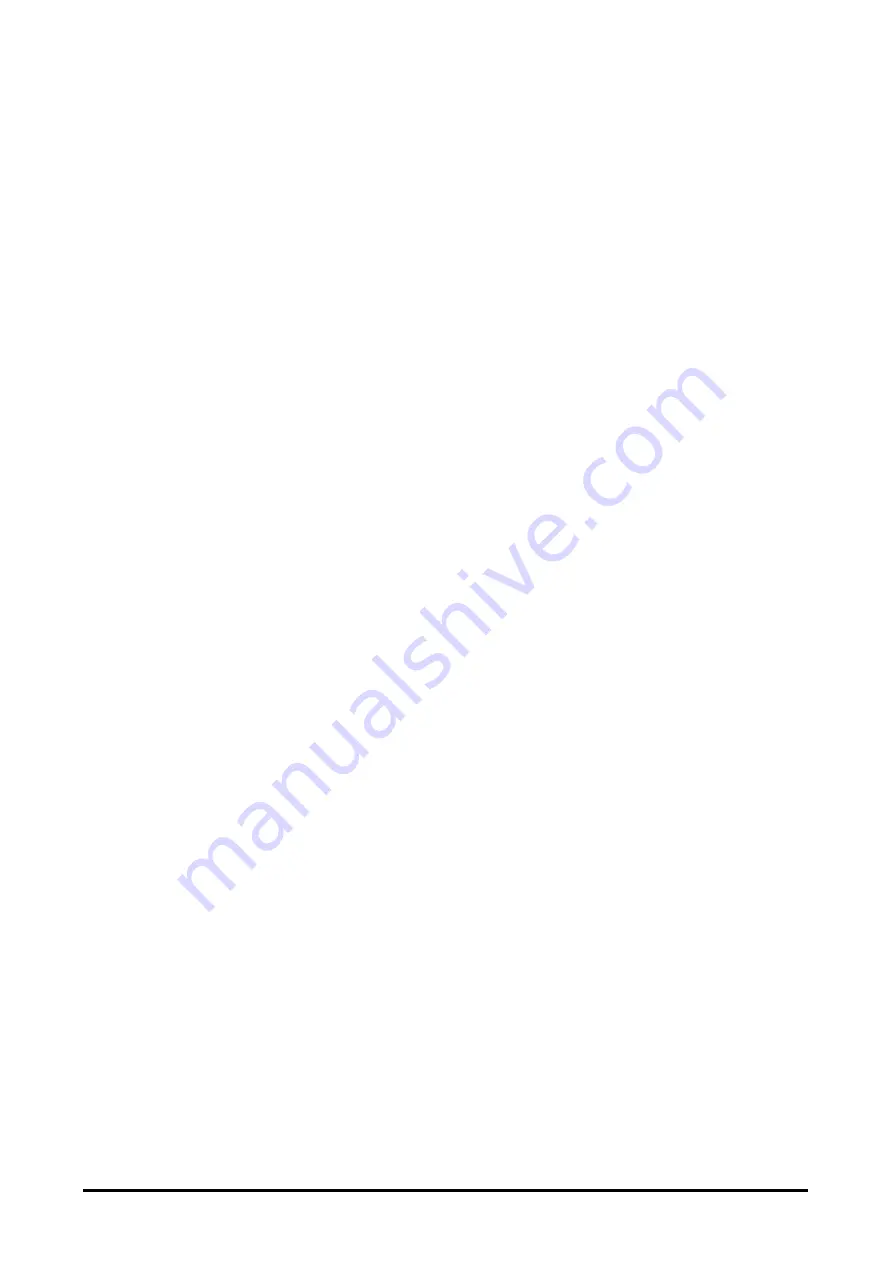
47
MicroController Control System
Testing And Adjusting
LED Diagnosis for Drive controller
Description of the alarms signalled by the diagnostic
LED. The alarm code is shown in parentheses.
A detailed description is given in the next section
1 BLINK = Logic anomaly (EEPROM DATA KO,
EEPROM PAR. KO, EEPROM CONF. KO,
EEPROM OFF-LINE, CHOPPER NO
CONF, WATCH-DOG).
2 BLINKS = Running request on startup or error in
handle/speeds sequence
(INCORRECT START).
3 BLINKS = Error on VMN test
(NO FULL CONDUCTION, VMN LOW).
4 BLINKS = Accelerator high in standby - this error
inhibits operation (VACC NOT OK).
5 BLINKS = Error in reading current- this error
inhibits operation
(I HIGH AT STAND, I=0 EVER).
6 BLINKS = Malfunctioning of the contactor driver
circuit
(DRIVER SHORTED, COIL SHORTED).
7 BLINKS = Excessive temperature, greater than
80˚C (TH. PROTECTION).
8 BLINKS = Contactors do not open or VMN high in
standby (BRAKE CONT. OPEN,
DIR CONT. OPEN, VMN HIGH).
9 BLINKS = Contact stuck (BRAKE CON CLOSED)
only for regenerative;(DIR. CON CLOSED)
only standard traction.
CONTINUOUS BLINKING (32BLINKS)
= Low battery charge, battery with <10% of residual
charge (BATTERY).
LED REMAINS ON
= Double running request (FORW BACK).
Analysis of Alarms Displaged on the Console
Drive controller
1) BRAKE CON CLOSED
Test carried out in the passage from running to
initial regenerative braking. If, on running contactor
closure, the VMN is >2/3 VBATT, an alarm is issued.
Possible causes:
a) The normally open contact of the braking contactor
is stuck. Unlock the contact and clean it: if it is too
much damaged replace the contator.
b) The braking contactor remains excited for a
defect in the logic board or because the coil wire
is in short towards the negative.
For understanding if the defect is produced by
one of these causes, select the running and
press the pedal without giving the seat or tiller
request, if the activation only of the braking
contactor is in synchrony with the pedal
(or selector) command verify what follows:
disconnect the wire from the connector and do
again the test above, if the contactor remains
disactivated replace the logic, otherwise if the
contactor moves check that there is not a wire in
short with a metallic part.
2) DIR. CONT. OPEN
Test carried out at running request :
running contator closure is verified by checking
that the VMN signal is consistent. Possible causes:
A1) There is not a good contact either on NO
(=nomally open) of FWD CTR or NC (=nomally
closed) of REV CTR, due to dust, dirt or any
particles which prevent a valid contact.
Clean contacts by means of compressed air :
if necessary remove dirt applying a soft
abrasive movement.
It could be necessary changing both contactors.
A2) There is not a good contact either on NO of
REV CTR or on NC of FWD CTR due to dust,
dirt or any particles which prevent a valid contact.
Clean contacts by means of compressed air;
if necessary remove dirt applying a soft
abrasive movement.
It could be necessary changing both contactors.
A3) The most probably reason is that the normally
closed contact of the braking contactor dosen’t
make a good contact towards the battery
negative for dust, dirt or because the contact
doesn’t lean completely for a mechanical
defect of the contactor.
It could be necessary to replace the contactor.
Содержание B20S-3
Страница 3: ......