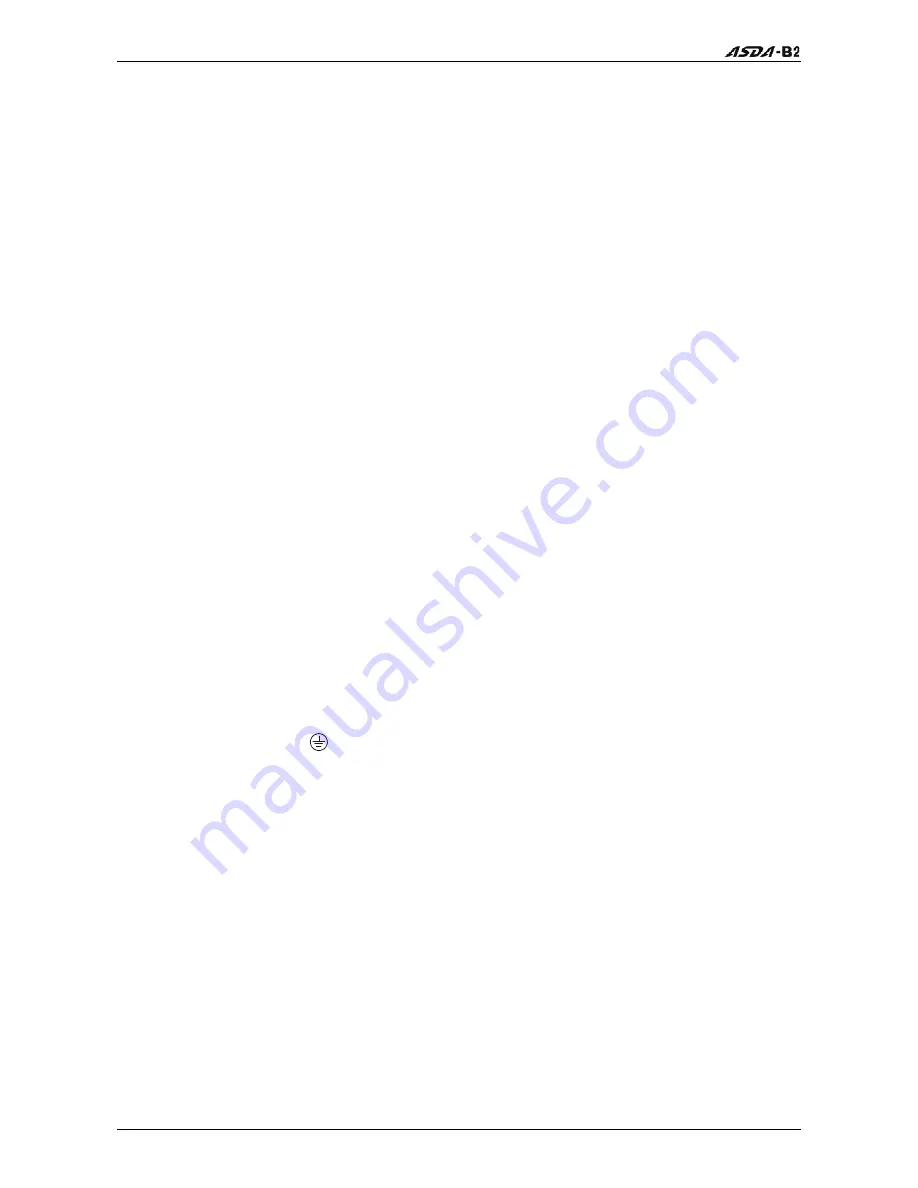
Chapter 3 Connections and Wiring
3-4
Revision June 2010
Wiring Notes
Please observe the following wiring notes while performing wiring and touching any
electrical connections on the servo drive or servo motor.
1.
Ensure to check if the power supply and wiring of the "power" terminals (R, S, T,
L1c, L2c, U, V, & W) is correct.
2.
Please use shielded twisted-pair cables for wiring to prevent voltage coupling and
eliminate electrical noise and interference.
3.
As a residual hazardous voltage may remain inside the drive, please do not
immediately touch any of the "power" terminals (R, S, T, L1c, L2c, U, V, & W) and/or
the cables connected to them after the power has been turned off and the charge
LED is lit. (Please refer to the Safety Precautions on page ii).
4.
The cables connected to R, S, T and U, V, W terminals should be placed in separate
conduits from the encoder or other signal cables. Separate them by at least 30cm
(11.8 inches).
5.
If the encoder cable is too short, please use a twisted-shield signal wire with
grounding conductor. The wire length should be 20m (65.62ft.) or less. For lengths
greater than 20m (65.62ft.), the wire gauge should be doubled in order to lessen
any signal attenuation. Regarding the specifications of 20m (65.62ft.) encoder
cable, please choose wire gauge AWG26, UL2464 metal braided shield twisted-pair
cable.
6.
As for motor cable selection, please use the 600V PTFE wire and the wire length
should be less than 98.4ft. (30m). If the wiring distance is longer than 30m
(98.4ft.), please choose the adequate wire size according to the voltage.
7.
The shield of shielded twisted-pair cables should be connected to the SHIELD end
(terminal marked
) of the servo drive.
8.
For the connectors and cables specifications, please refer to section 3.1.6 for
details.
Содержание ASD-B2-0121-B
Страница 1: ......
Страница 13: ...Table of Contents xii Revision June 2010 This page intentionally left blank...
Страница 17: ...Chapter 1 Unpacking Check and Model Explanation 1 4 Revision June 2010 ECMA Series Servo Motor...
Страница 19: ...Chapter 1 Unpacking Check and Model Explanation 1 6 Revision June 2010 1 4 Servo Drive Features...
Страница 21: ...Chapter 1 Unpacking Check and Model Explanation 1 8 Revision June 2010 This page intentionally left blank...
Страница 25: ...Chapter 2 Installation and Storage 2 4 Revision June 2010 Minimum Clearances Side by Side Installation...
Страница 43: ...Chapter 3 Connections and Wiring 3 6 Revision June 2010 Figure 3 3 Three Phase Power Supply all models...
Страница 72: ...Chapter 3 Connections and Wiring Revision June 2010 3 35 3 5 2 Connection between PC and Connector CN3...
Страница 87: ...Chapter 4 Display and Operation 4 12 Revision June 2010 This page intentionally left blank...
Страница 100: ...Chapter 5 Trial Run and Tuning Procedure Revision June 2010 5 13 5 5 2 Load Inertia Estimation Flowchart...
Страница 131: ...Chapter 6 Control Modes of Operation 6 22 Revision June 2010 Time Domain...
Страница 153: ...Chapter 6 Control Modes of Operation 6 44 Revision June 2010 This page intentionally left blank...
Страница 267: ...Chapter 8 MODBUS Communications 8 18 Revision June 2010 This page intentionally left blank...
Страница 271: ...Chapter 9 Maintenance and Inspection 9 4 Revision June 2010 This page intentionally left blank...
Страница 291: ...Chapter 11 Specifications 11 8 Revision June 2010 11 3 Servo Motor Speed Torque Curves...