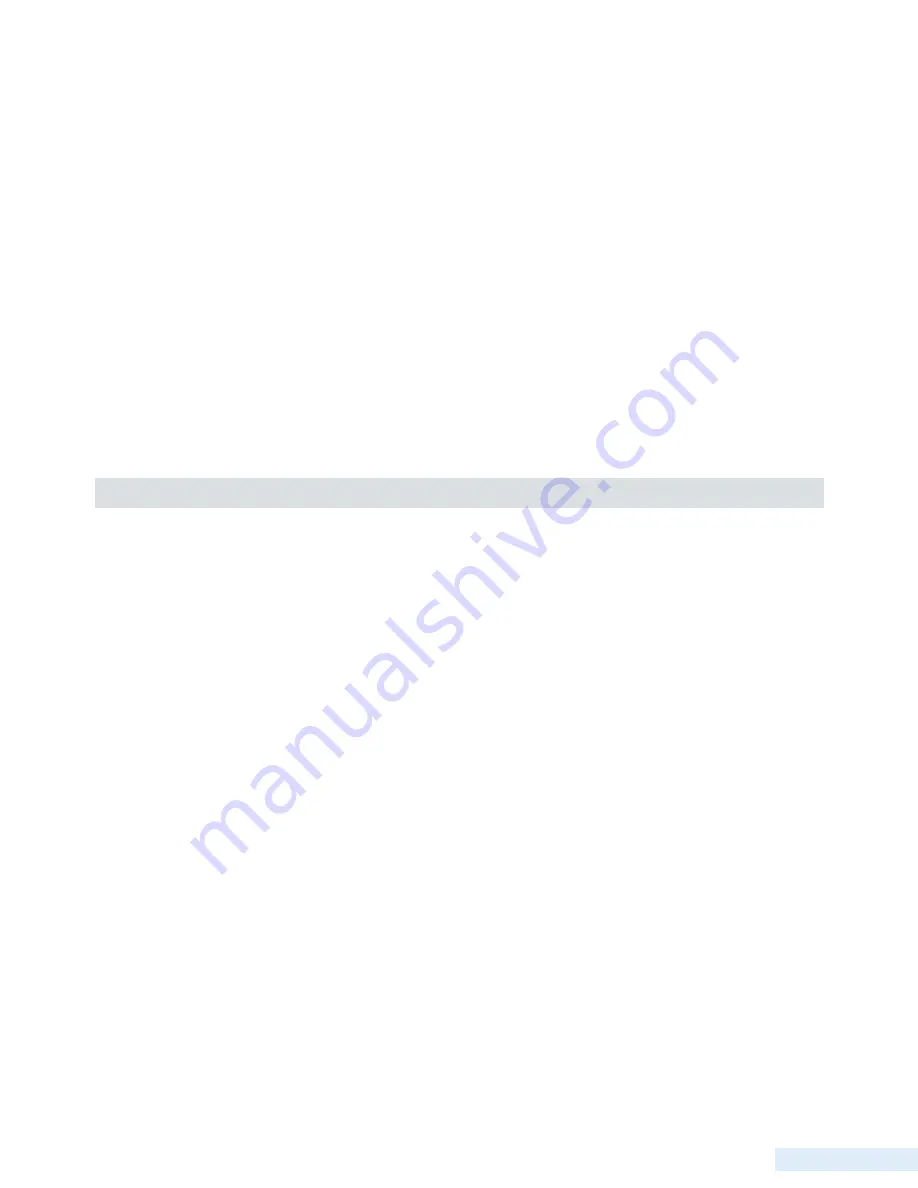
73
V i e w i n g a n d T r o u b l e s h o o t i n g A l a r m s
Check the starter circuit for faults by using the H-O-A switches to control the pumps. Verify that the pump run LED and
the corresponding pump motor turn on when the H-O-A switch is in the “Hand” position and off when the switch is in the
“Off” position. Switching the H-O-A switch out of the “Auto” position should clear the flashing pump run LED. If the LED
does not turn on when the motor starts and turn off when the motor stops, check the wiring and verify that:
• Only one bias source is used to bias all motor run inputs.
• The same voltage-dropping resistor is used for all motor run inputs.
• The return for the bias voltage is properly connected to the IN_COM_1 terminal.
• If the EXT_PM input is used, make sure that it uses the same bias voltage and dropping resistor as the motor run
inputs.
Verify that the TCU’s configured motor start fault delay (Start Fault) is set to an adequate length of time. If necessary,
increase the Start Fault delay.
If the problem cannot be resolved, the TCU may require factory service. See “Appendix H: Support, Service, and Warranty”
for removal, replacement, and servicing instructions.
Motor Stop Fault
A motor stop fault indicates that either the TCU sent a signal to turn off a pump and the pump remained on, or a pump came
on without the TCU calling it. When this occurs, the LED under the faulted pump’s H-O-A switch flashes.
The default time allowed for the input to follow the output is two seconds. To accommodate applications where the stop
signal may not be immediate, such as occurs with solid-state motor controllers, you can configure the TCU with a start and
stop delay from 2-510 seconds.
If the Auto Retry function is enabled (see Auto Retry, page 53), the TCU will attempt to use the faulted pump the next time
its turn comes up in the alternation order. If the TCU is successful at calling the pump to run and receives a pump run status,
it will clear the Motor Stop Fault. This response is identical to that of the PCU.
If the Auto Retry function is disabled, the TCU will not clear a Motor Stop Fault and will not use a faulted pump until the
pump’s operation is overridden (by moving the corresponding H-O-A switch to the Off or Hand position, or by overriding
the pump via telemetry). The TCU considers the pump failed and will take the failed pump out of rotation and assign a new
lead pump to start with the lead level. A PCU with Auto Retry disabled also will not clear the Motor Stop Fault. However,
the PCU will attempt to start the faulted pump the next time its turn comes up in the alternation order. The PCU makes
the assumption that the pump run status is accurate and will delay another pump from starting until the number of pumps
required is one more than the failed number of pumps. For example if pump 2 has failed, and pump 1 is the lead pump,
pump 1 will not start until the Lag 1 level is reached.
If a motor stop fault occurs, verify that:
• The TCU’s configured motor stop fault delay (Stop Fault) is set for an adequate length of time. If necessary, increase
the Stop Fault delay.
Содержание TCU800
Страница 1: ...Installation and Operation Manual T C U 8 0 0 Data Flow Systems Inc P r e l i m i n a r y ...
Страница 2: ...Intentionally left blank ...
Страница 4: ...D a t a F l o w S y s t e m s I n c Intentionally left blank ...
Страница 8: ...ii Intentionally left blank ...
Страница 10: ...ii Intentionally left blank ...
Страница 49: ...39 S e t u p Externally Powered Non submersible Transducer TCU Powered Non submersible Transducer ...
Страница 56: ...46 C h a p t e r 5 Quick View Analog View Pump Statistics ...
Страница 57: ...47 U s e r I n t e r f a c e Alarms Settings Screen 1 Settings Screen 2 ...
Страница 58: ...48 C h a p t e r 5 Advanced Settings About ...
Страница 77: ...67 O p e r a t i n g P r o c e d u r e s TCU Installed in Existing Control Panel ...
Страница 87: ...77 M o d b u s S u p p o r t Figure 1 Figure 2 Figure 3 ...
Страница 92: ...82 D a t a F l o w S y s t e m s I n c Appendix ...
Страница 157: ...147 D a t a F l o w S y s t e m s I n c ...
Страница 158: ...148 D a t a F l o w S y s t e m s I n c ...
Страница 159: ...149 D a t a F l o w S y s t e m s I n c ...
Страница 160: ......
Страница 161: ...151 D a t a F l o w S y s t e m s I n c ...
Страница 162: ...Data Flow Systems Inc 605 N John Rodes Blvd Melbourne Florida 32934 321 259 5009 www dataflowsys com ...