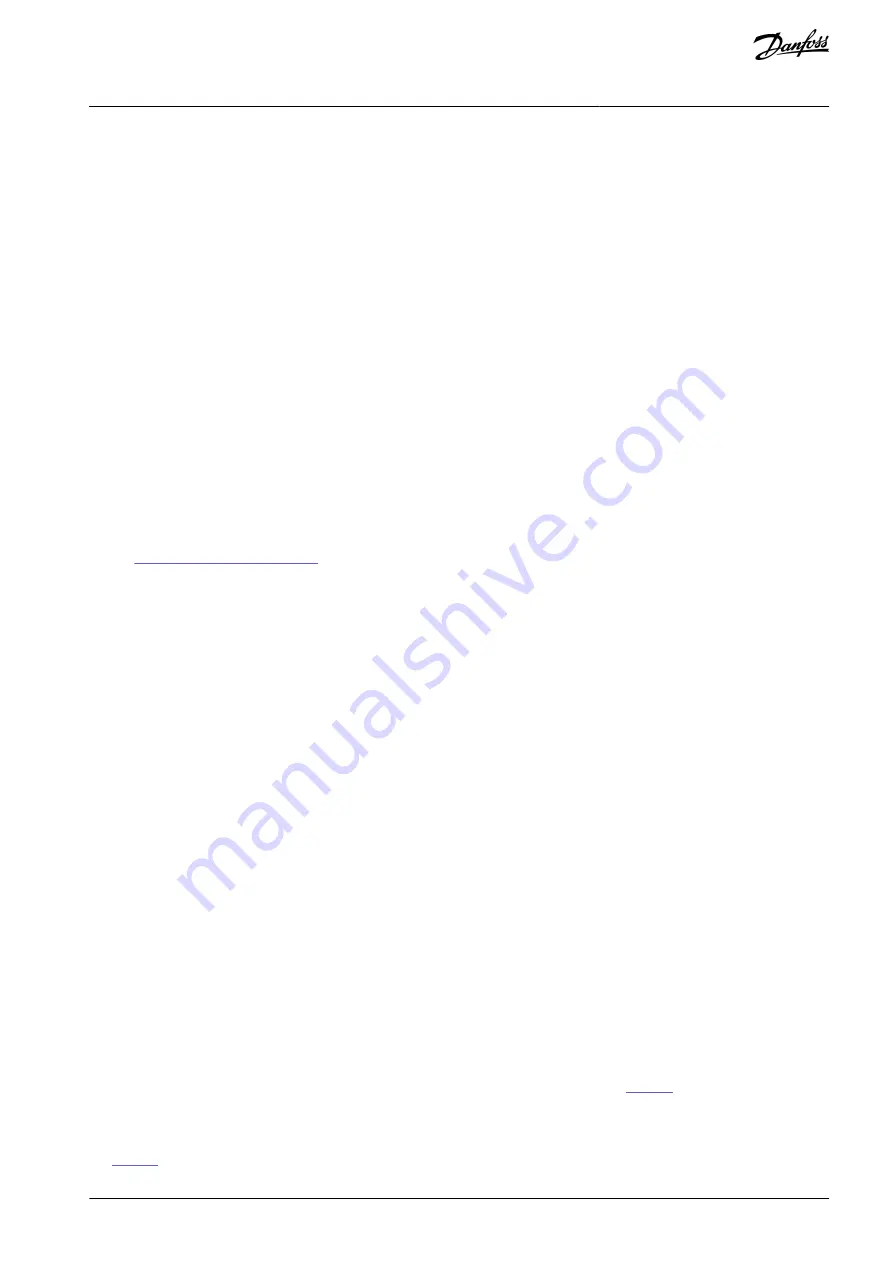
•
•
•
•
-
•
-
•
-
•
-
•
-
•
-
•
•
•
6.2.13 Safe Torque Off
To run STO, extra wiring for the drive is required. Refer to the VLT® Safe Torque Off Operating Guide for further information.
Liability conditions
The customer is responsible for ensuring that personnel know how to install and operate the Safe Torque Off function by:
Reading and understanding the safety regulations concerning health, safety, and accident prevention.
Understanding the generic and safety guidelines provided in the VLT® Safe Torque Off Operating Guide.
Having a good knowledge of the generic and safety standards for the specific application.
6.3 Dynamic Braking
Dynamic braking slows the motor using 1 of the following methods:
AC brake:
The brake energy is distributed in the motor by changing the loss conditions in the motor (
parameter 2-10 Brake Function
=
[2] AC Brake
). The AC brake function cannot be used in applications with high cycling frequency since this situation over-
heats the motor.
DC brake:
An overmodulated DC current added to the AC current works as an eddy current brake (
parameter 2-02 DC Braking Time ≠
0 s
).
Resistor brake:
A brake IGBT keeps the overvoltage under a certain threshold by directing the brake energy from the motor to the connec-
ted brake resistor (
parameter 2-10 Brake Function
=
[1] Resistor Brake
). For more information on selecting a brake resistor, see
10.9.1 Selection of Brake Resistor
or the VLT® Brake Resistor MCE 101 Design Guide.
For drives equipped with the brake option, a brake IGBT along with terminals 81(R-) and 82(R+) are included for connecting an ex-
ternal brake resistor. The function of the brake IGBT is to limit the voltage in the DC link whenever the maximum voltage limit is
exceeded. It limits the voltage by switching the externally mounted resistor across the DC bus to remove excess DC voltage present
on the bus capacitors.
External brake resistor placement has the advantages of selecting the resistor based on application need, dissipating the energy
outside of the control panel, and protecting the drive from overheating if the brake resistor is overloaded. The brake IGBT gate sig-
nal originates on the control card and is delivered to the brake IGBT via the power card and gatedrive card. Also, the power and
control cards monitor the brake IGBT for a short circuit. The power card also monitors the brake resistor for overloads.
External brake resistor placement has the advantages of selecting the resistor based on application need, dissipating the energy
outside of the control panel, and protecting the drive from overheating if the brake resistor is overloaded.
6.4 Load Sharing
Load sharing enables connection of multiple Danfoss VLT® drives over the same DC link with the following benefits:
Energy savings:
A motor running in regenerative mode can supply drives that are running in motoring mode. Alternatively, the motor run-
ning in regenerative mode can supply any brake resistors used with the drives.
Reduced need for spare parts:
Usually, only 1 brake resistor is required for the installation instead of a brake resistor for each drive.
Power back-up:
If there was mains failure, all Danfoss VLT® drives can be supplied through the DC link from a back-up. The application can
thus continue running or go through a controlled shutdown process.
6.4.1 Preconditions and Special Conditions
Before considering load sharing, ensure that the following preconditions are met:
Equip the drives with load sharing terminals. Enclosure sizes A1–A5 and B3 have load sharing terminals by default.
Enclosure sizes B, C, and F must be configured for load sharing when ordering. The standard load share selection in character 21
or the type code is D, but other selections are available. For more configuration options, see
. It is not possible to retrofit
load sharing terminals on enclosure sizes B, C, and F.
Enclosure sizes D and E must be configured for load sharing either when ordering or by using a retrofit kit. The standard load
share selection in character 21 of the type code is D, but other options are available. For more configuration options, see the
AJ300847815559en-000101 / 130R0337 | 53
Danfoss A/S © 2020.09
Product Features
VLT® AQUA Drive FC 202
Design Guide