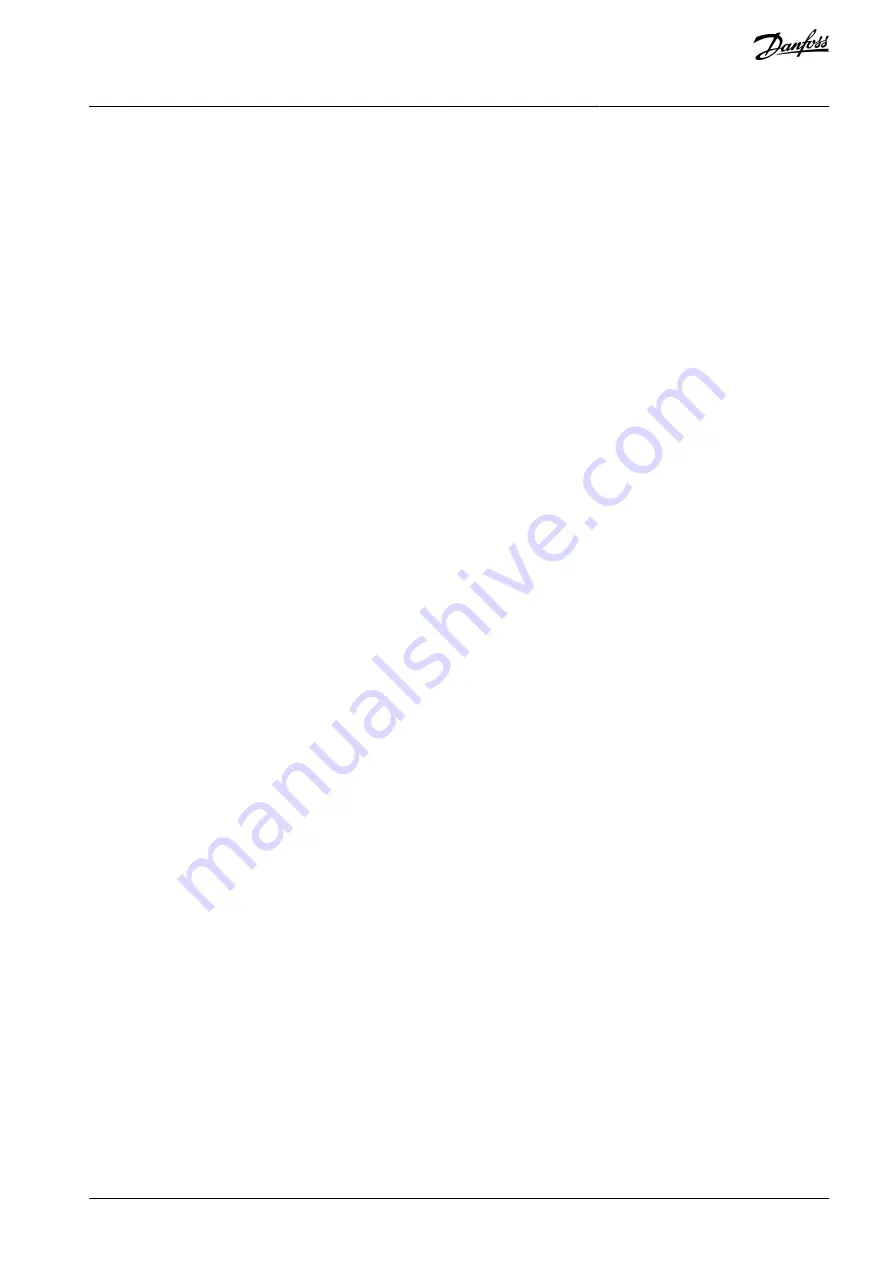
•
•
•
•
•
•
•
•
•
•
•
•
•
•
5.1.1.2 Reduction of Motor Acoustic Noise
There are 3 main sources for generation of acoustic noise in the motor:
The magnetic noise produced by the motor core through magnetostriction.
The noise produced by motor bearings.
The noise produced by motor ventilation.
When a motor is fed by a drive, the pulse-width-modulated (PWM) voltage applied to the motor causes extra magnetic noise at the
switching frequency and harmonics of the switching frequency (mainly the double of the switching frequency). In some applica-
tions, this is not acceptable. To eliminate this additional switching noise, use a sine-wave filter. This filter filters the pulse-shaped
voltage from the drive and provides a sinusoidal phase-to-phase voltage at the motor terminals.
5.1.1.3 Reduction of High-frequency Electromagnetic Noise in Motor Cables
Using filters reduces noise generated in the motor cables.
When no filters are used, the ringing voltage overshoot that occurs at the motor terminals is the main high-frequency noise source.
The noise can be explained by the correlation between the frequency of the voltage ringing at the motor terminals and the spec-
trum of the high-frequency conducted interference in the motor cable. Besides this noise component, there are also other noise
components such as:
The common-mode voltage between phases and ground at the switching frequency and its harmonics - high amplitude but
low frequency.
High-frequency noise (above 10 MHz) caused by the switching of semiconductors - high frequency but low amplitude.
Installing an output filter gives the following advantages:
dU/dt filters reduce the frequency of the ringing oscillation to a level below 150 kHz.
Sine-wave filters eliminate the ringing oscillation and the motor receives a sinusoidal phase-to-phase voltage.
5.1.1.4 Bearing Currents and Shaft Voltage
Fast switching transistors in the drive combined with an inherent common-mode voltage (voltage between phases and ground)
generate high-frequency bearing currents and shaft voltages. While bearing currents and shaft voltages can also occur in direct-on-
line motors, these phenomena are accentuated when the motor is fed from a drive.
Most bearing damage in motors fed by drives is caused by vibrations, misalignment, excessive axial or radial loading, improper lubri-
cation, and impurities in the grease. Sometimes, bearing damage is caused by bearing currents and shaft voltages. The mechanism
that causes bearing currents and shaft voltages is complicated to explain, but it is important to know that it exists. Two main mecha-
nisms can be identified:
Capacitive coupling: The voltage across the bearing is generated by parasitic capacitances in the motor.
Inductive coupling: Caused by circulating currents in the motor.
The grease film of a running bearing behaves like isolation. The voltage across the bearing can cause a breakdown of the grease film
and produce a small electric discharge (a spark) between the bearing balls and the running track. This discharge produces a micro-
scopic melting of the bearing ball and running track metal and over time it causes the premature wear-out of the bearing. This
mechanism is called electrical discharge machining (EDM).
Reduce bearing limit stress by using common-mode filters. Sine-wave filters reduce circulating currents but not common-mode cur-
rents.
5.1.2 Supported Motor Types
Today, the drive-controlled, 3-phase motor is a standard element in all automated applications. High-efficiency induction motors,
but also motor designs such as permanent magnet motors, EC motors, and synchronous reluctance motors, need regulation with
AC drives. Many motors cannot be operated directly from the 3-phase standard power supply.
The Danfoss VLT® drives can control multiple motor technologies:
Induction motors (IM).
Surface permanent magnet motors (SPM).
Interior permanent magnet motors (IPM).
Synchronous reluctance motors (SynRM).
Permanent magnet assisted synchronous reluctance motors (PMaSynRM).
AJ300847815559en-000101 / 130R0337 | 31
Danfoss A/S © 2020.09
Product Overview
VLT® AQUA Drive FC 202
Design Guide