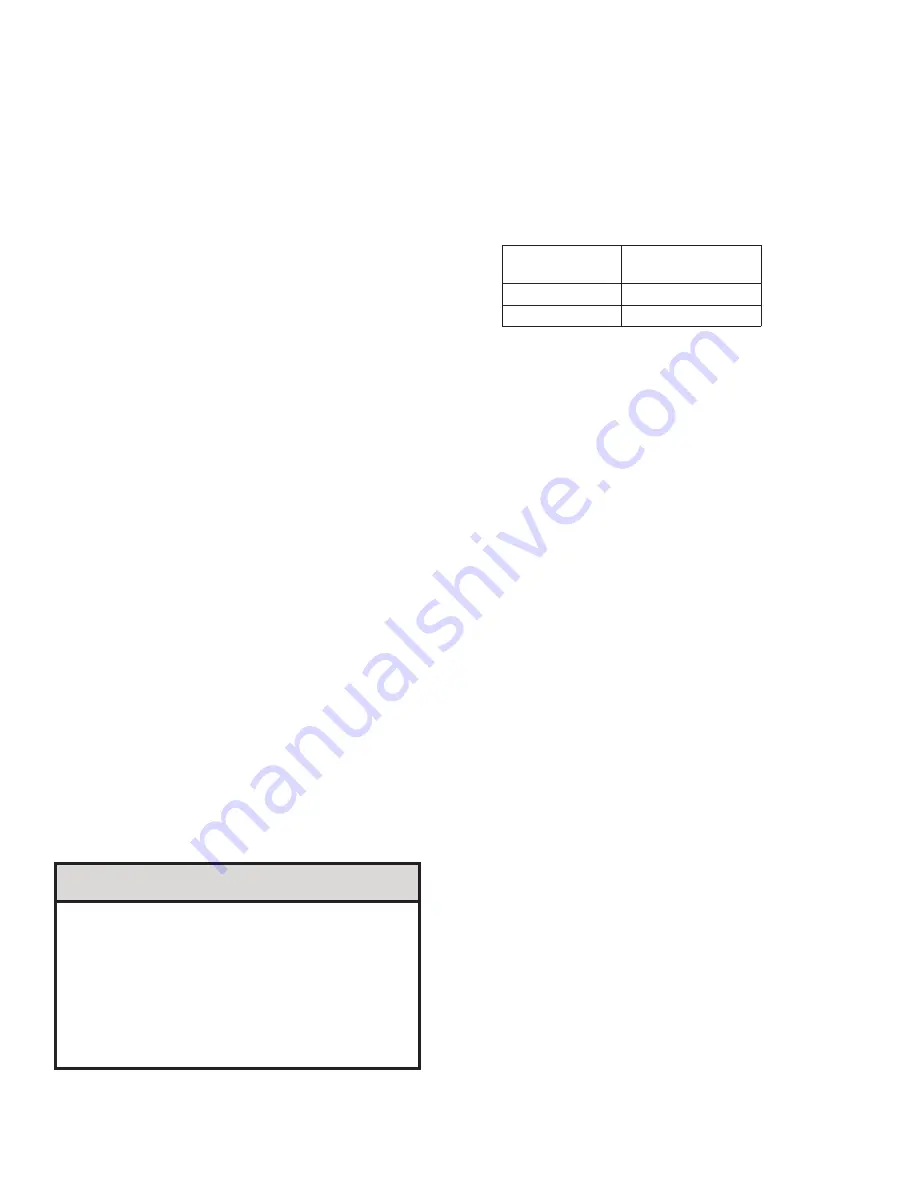
52
3. The terminal block TB-2
in conjunction with
terminal screw identification label is attached to the
junction box front and located inside R7910 Control
compartment on the left side.
4. The connections are (listed identification
label top to bottom):
• 1 – “Heating Thermostat”
• 2 – “Heating Thermostat”
• 3 – “DHW Temperature Switch”
• 4 – “DHW Temperature Switch”
• 5 – “Outdoor Sensor”
• 6 – “Outdoor Sensor”
• 7 – “Header Sensor”
• 8 – “Header Sensor”
• 9 – “Remote Firing Rate -”
• 10 – “Remote Firing Rate +”
• 11 – “External Limit”
• 12 – “External Limit”
5. If the outdoor sensor is connected
to
terminals 5 and 6 “Outdoor Sensor”, the boiler
will adjust the target space heating set point supply
water temperature downwards as the outdoor air
temperature increases. If used, this sensor should
be located on the outside of the structure in an area
where it will sense the average air temperature
around the house. Avoid placing this sensor in areas
where it may be covered with ice or snow. Locations
where the sensor will pick up direct radiation from
the sun should also be avoided. Avoid placing the
sensor near potential sources of electrical noise
such as transformers, power lines, and fluorescent
lighting. Wire the sensor to the boiler using 22
gauge or larger wire. As with the sensor, the sensor
wiring should be routed away from sources of
electrical noise. Where it is impossible to avoid such
noise sources, wire the sensor using a 2 conductor,
UL Type CM, AWM Style 2092, 300 Volt 60°C
shielded cable. Connect one end of the shielding on
this cable to ground.
NOTICE
When making low voltage connections, make
sure that no external power source is present
in the thermostat or limit circuits. If such a
power source is present, it could destroy the
boiler’s microprocessor control (R7910). One
example of an external power source that could
be inadvertently connected to the low voltage
connections is a transformer in old thermostat
wiring.
D. Power Requirements
Nominal boiler current draw is provided in Table
21. These values are for planning purposes only
and represent only the boiler’s power consumption.
To obtain total system power consumption add any
selected circulator and component current draws.
VIII. Electrical
(continued)
Model Number
Nominal Current
(amps)
PHNTM399
< 7
PHNTM500
< 6
Table 21: Boiler Current Draw
E. Flow Switch Wiring
Phantom boilers include factory provided flow switch to
prevent boiler overheating. See Section VI, Water Piping
and Trim for pertinent details.
The flow switch is an operating control and must be used in
combination and wired in series with boiler safety high limit
control and other safety controls where applicable.
Wiring of the switch to boiler, including wire and conduit
supplies, is the responsibility of the installing contractor.
Use properly rated temperature wire for the anticipated
service temperature. Make all electrical connections in
accordance with the
National Electrical Code
,
NFPA 70,
and/or
Canadian Electrical Code
Part 1, CSA C22.1 and
local codes, where applicable.
To wire the installed flow switch proceed as follows:
1. Remove jumper
that is factory installed between
terminals 11 and 12 at the low voltage terminal strip
located inside boiler control panel assembly.
2. Using installer-provided wire and conduit,
wire the switch NO (normally open) terminal to
the terminal 11 and, the switch COM (common)
terminal to terminal 12. Also see/follow Taco
Instruction Sheet for Flow Switch Kit supplied
with the flow switch for specific details and Figure
26 “Ladder Diagram” and Figure 27 “Connection
Diagram” in this section.
F. Multiple Boiler Wiring
Install over-current protection in accordance with
authority having jurisdiction or, in the absence of
such requirements, follow the
National Electric Code
,
NFPA 70, and/or
Canadian Electrical Code
Part 1,
CSA C22.1. Do not provide over-current protection
greater than 15 amperes. If it becomes necessary to
provide greater amperes (because of the number of
boilers provided) use separate circuits and over-current
protection for additional boilers.
Содержание PHNTM399
Страница 6: ...6 I Product Description Specifications and Dimensional Data continued Figure 1A Phantom Model PHNTM399...
Страница 7: ...7 Figure 1B Phantom Model PHNTM500 I Product Description Specifications and Dimensional Data continued...
Страница 53: ...53 VIII Electrical continued Figure 26 Ladder Diagram...
Страница 54: ...54 VIII Electrical continued...
Страница 55: ...55 Figure 27 Wiring Connections Diagram VIII Electrical continued...
Страница 63: ...63 IX System Start up continued Phantom Series Operating Instructions Figure 32 Operating Instructions...
Страница 113: ...113 THIS PAGE LEFT BLANK INTENTIONALLY...
Страница 114: ...114 XIII Repair Parts continued PHNTM399 and PHNTM500...
Страница 118: ...118...
Страница 119: ...119...