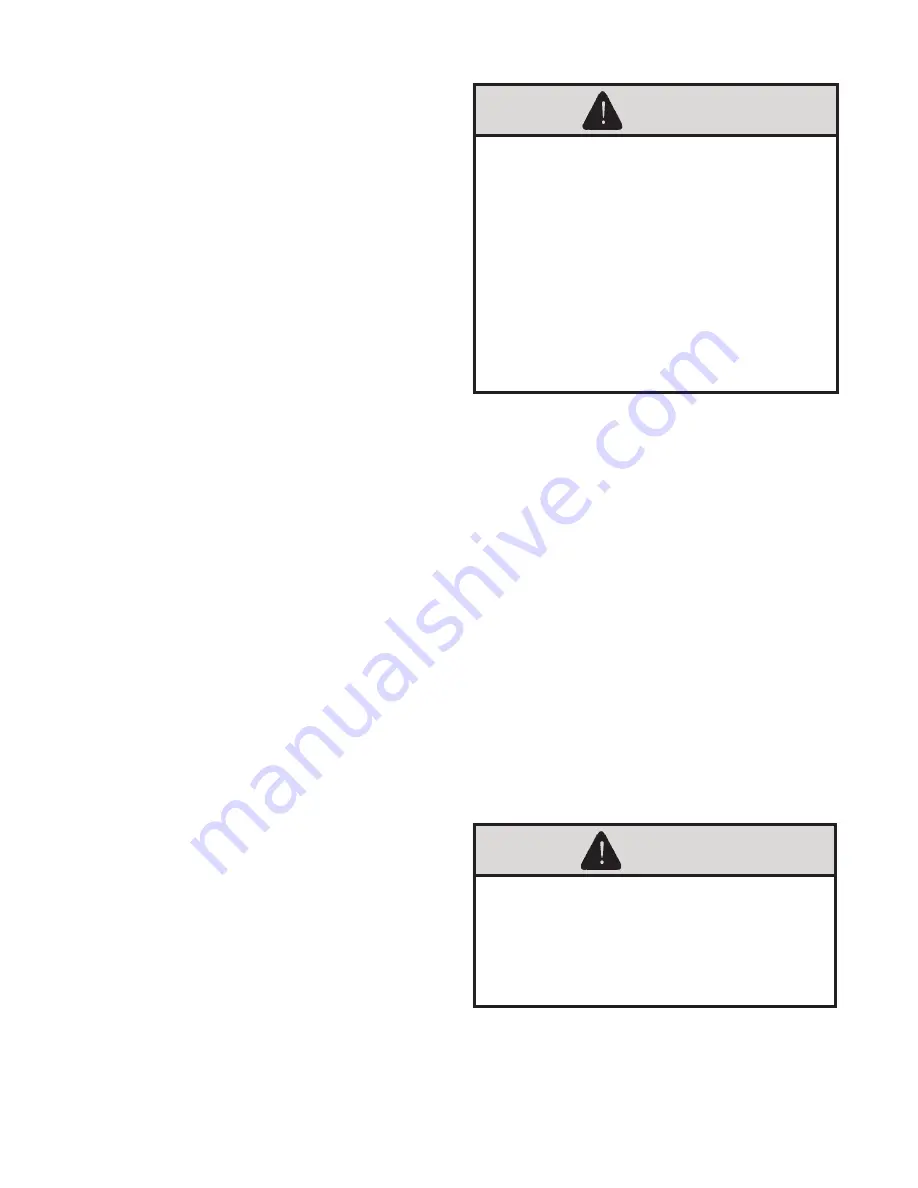
66
IX. System Start-up
(continued)
M. Test Safety Limits Controls
1. Test the ignition system safety shut-off
by
disconnecting the flame sensor connector (black
plug with orange wire) from the flame ionization
electrode. See Figure 26. The boiler must shut
down and must not start with the flame sensor
disconnected.
2. Test any other external limits
or other controls
in accordance with the manufacturer’s instructions.
N. Check Thermostat Operation
Verify that the boiler starts and stops in response to
calls for heat from the heating thermostat and indirect
water heater thermostat. Make sure that the appropriate
circulators also start and stop in response to the
thermostats.
O. Adjust Supply Water Temperature
As shipped, the heating set point supply temperature
is set to 180°F (82.2°C) and, indirect water heater set
point supply temperature is set to 170°F (76.7°C). If
necessary, adjust these to the appropriate settings for
the type of system to which this boiler is connected.
See Section X “Operation” (Parameter Table 29) of
this manual for information on how to adjust supply
setpoint.
P. Adjust Thermostats
Adjust the heating and indirect water heater thermostats
to their final set points.
Q. Field Conversion From Natural Gas to LP
Gas
Phantom models PHNTM210 and PHNTM285
are factory shipped as natural gas builds. Models
configured for use at altitudes below 7000ft can be
field converted to LP gas. Follow steps below for field
conversion from natural gas to LP Gas.
1. Conversion
of Phantom models PHNTM210
and PHNTM285 from one fuel to another is
accomplished using the throttle screw on the gas
valve. Figure 34 “Gas Valve Detail” shows the
location of the throttle screw on the valve. Locate
the throttle screw on the boiler being converted.
WARNING
Explosion Hazard. Asphyxiation Hazard.
This conversion should be performed by a
qualified service agency in accordance with the
manufacturer’s instructions and all applicable
codes and requirements of the authority
having jurisdiction. If the information in these
instructions is not followed exactly, a fire, an
explosion or production of carbon monoxide
may result causing property damage, personal
injury, or loss of life. The qualified service
agency is responsible for proper conversion of
these boilers. The conversion is not proper and
complete until the operation of the converted
appliance is checked as specified in this manual.
2. If conversion is being made on a new
installation,
install the boiler in accordance
with the installation instructions supplied with the
boiler. If an installed boiler is being converted,
connect the new gas supply to the boiler, check for
gas leaks, and purge the gas line up to the boiler
in accordance with the
National Fuel Gas Code
,
ANSI Z223.1/NFPA 54 and/or
Natural Gas and
Propane Installation Code
, CAN/CSA B149.1 or the
requirements of the authority having jurisdiction.
3. Before attempting to start the boiler,
make the
number of turns to the throttle screw called for in
Table 24.
4. Attempt to start the boiler
using the Operating
Instructions located inside the lower front cover of
the boiler. If the boiler does not light on the first
try for ignition, allow to boiler to make at least
four more attempts to light. If boiler still does not
light, turn the throttle counter clockwise in 1/4 turn
increments, allowing the boiler to make at least
three tries for ignition at each setting, until the boiler
lights.
WARNING
Asphyxiation Hazard. The throttle adjustments
shown in Table 24 are approximate. The
final throttle setting must be found using a
combustion analyzer. Leaving the boiler in
operation with a CO level in excess of the value
shown in Table 23 could result in injury or death
from carbon monoxide poisoning.
5.
After the burner lights,
complete all steps
outlined in Paragraph L “Perform Combustion Test”
before proceeding.
Содержание Phantom-X PHNTM210
Страница 7: ...7 Figure 1B Model PHNTM285 I Product Description Specifications and Dimensional Data continued...
Страница 52: ...52 VIII Electrical continued...
Страница 53: ...53 VIII Electrical continued Figure 26 Wiring Connections Diagram...
Страница 54: ...54 VIII Electrical continued Figure 27 Ladder Diagram...
Страница 59: ...59 Figure 29B Boiler to Boiler Communication with Crown Zone Panel PN 3501505 VIII Electrical continued...
Страница 109: ...109 XIII Repair Parts 1L 1K 1J 1E 1C 1D 1B 1L 1J 1A 1M 1F 1C 1D 1B 1L 1J 1A 1M 1F 1K 1G 1G 1K 1H 1G...
Страница 118: ...118...
Страница 119: ...119...