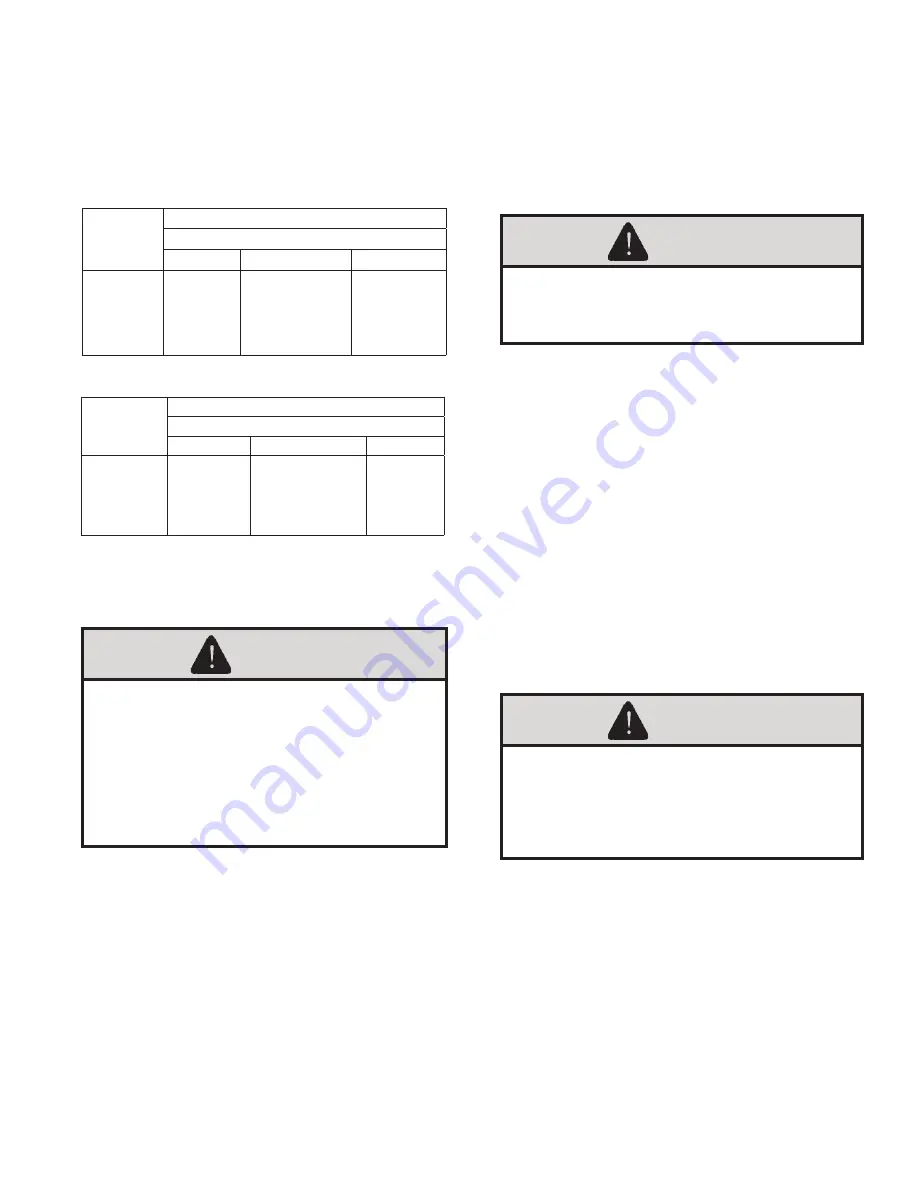
65
a. Lock boiler in high fire and allow boiler to
operate for approximately 5 minutes before
taking combustion readings. To lock boiler in
high fire, from the home screen, press “Adjust”,
Boiler
Model
Altitude Range
0 - 7000 Ft.
% CO
2
% O
2
Range
CO, PPM
PHNTM210
PHNTM285
9.9 - 8.2
(High Fire)
9.9 - 7.9
(Low Fire)
3.5 - 6.5
(High Fire)
3.5 - 7.0
(Low Fire)
Less than
100 PPM
Table 22: Typical Combustion Settings,
Natural Gas
IX. System Start-up
(continued)
to both gas valves equally and simultaneously.
Refer to Figure 34 for location of throttle screw.
Verify CO is less than 100 ppm.
d. Lock boiler in low fire and allow boiler to
operate for approximately 5 minutes before
taking combustion readings. Press “Low” to
lock boiler in low fire.
WARNING
Asphyxiation Hazard. Offset screw is adjusted
at the factory to the specification. DO NOT
touch the offset screw if measured low fire O
2
(or
CO
2
) is within limits specified in Table 22 or 23.
e. If low fire O
2
is too low (CO
2
is too high),
increase O
2
(decrease CO
2
) by turning offset
screw counterclockwise in less than 1/8 turn
increments and checking the O
2
(or CO
2
) after
each adjustment. If boiler is equipped with 2 gas
valves, offset screw adjustments must be done
to both gas valves equally and simultaneously.
Refer to Figure 34 for location of offset screw.
Verify CO is less than 100 ppm.
f. If low fire O
2
is too high (CO
2
is too low),
decrease O
2
(increase CO
2
) by turning offset
screw clockwise in less than 1/8 turn increments
and checking the O
2
(or CO
2
) after each
adjustment. If boiler is equipped with 2 gas
valves, offset screw adjustments must be done
to both gas valves equally and simultaneously.
Refer to Figure 34 for location of offset screw.
Verify CO is less than 100 ppm.
WARNING
Asphyxiation Hazard. Install flue temperature
sensor and sensor cap into two-pipe vent
connector port upon completion of combustion
test. Failure to properly secure the flue
temperature sensor into the port could lead to
property damage, personal injury or loss of life.
3. Reinstall flue temperature sensor with sensor
cap
at two-pipe vent adapter.
a. Inspect flue temperature sensor cap for
degradation. Replace if needed.
b. Use Molykote 111 grease to lubricate outer
surface of two-pipe vent adapter stub where flue
temperature sensor is inserted. Also lubricate
tip of flue temperature sensor. Reinstall flue
temperature sensor with cap into two-pipe vent
adapter.
4. Return boiler
to normal operating mode by
pressing “Auto”.
Boiler
Model
Altitude Range
0 - 7000 Ft.
% CO
2
% O
2
Range
CO, PPM
PHNTM210
PHNTM285
11.4 - 9.5
(High Fire)
11.4 - 9.1
(Low Fire)
3.5 - 6.5
(High Fire)
3.5 - 7.0
(Low Fire)
Less than
100 PPM
Table 23: Typical Combustion Settings, LP Gas
“Adjust”, “Login”, “000”. Enter the password
“086” and press return arrow to close the keypad.
Press “Save”, “Adjust”, “High” to lock boiler in
high fire.
WARNING
Make sure that all adjustments at high fire are
made with the throttle, not offset screw (see
Figure 34). The offset screw has been factory set
using precision instruments and must never be
adjusted in the field unnecessarily.
Attempting to adjust the offset screw
unnecessarily could result in damage to the gas
valve and may cause property damage, personal
injury or loss of life.
b. If high fire O
2
is too low (CO
2
is too high),
increase O
2
(decrease CO
2
) by turning the throttle
screw clockwise in 1/4 turn increments and
checking the O
2
(or CO
2
) after each adjustment.
Refer to Figure 34 for location of throttle screw.
Verify CO is less than 100 ppm.
c. If high fire O
2
is too high (CO
2
is too low),
decrease O
2
(increase CO
2
) by turning the
throttle screw counter-clockwise in 1/4 turn
increments and checking the O
2
(or CO
2
) after
each adjustment. If boiler is equipped with 2 gas
valves, throttle screw adjustments must be done
Содержание Phantom-X PHNTM210
Страница 7: ...7 Figure 1B Model PHNTM285 I Product Description Specifications and Dimensional Data continued...
Страница 52: ...52 VIII Electrical continued...
Страница 53: ...53 VIII Electrical continued Figure 26 Wiring Connections Diagram...
Страница 54: ...54 VIII Electrical continued Figure 27 Ladder Diagram...
Страница 59: ...59 Figure 29B Boiler to Boiler Communication with Crown Zone Panel PN 3501505 VIII Electrical continued...
Страница 109: ...109 XIII Repair Parts 1L 1K 1J 1E 1C 1D 1B 1L 1J 1A 1M 1F 1C 1D 1B 1L 1J 1A 1M 1F 1K 1G 1G 1K 1H 1G...
Страница 118: ...118...
Страница 119: ...119...