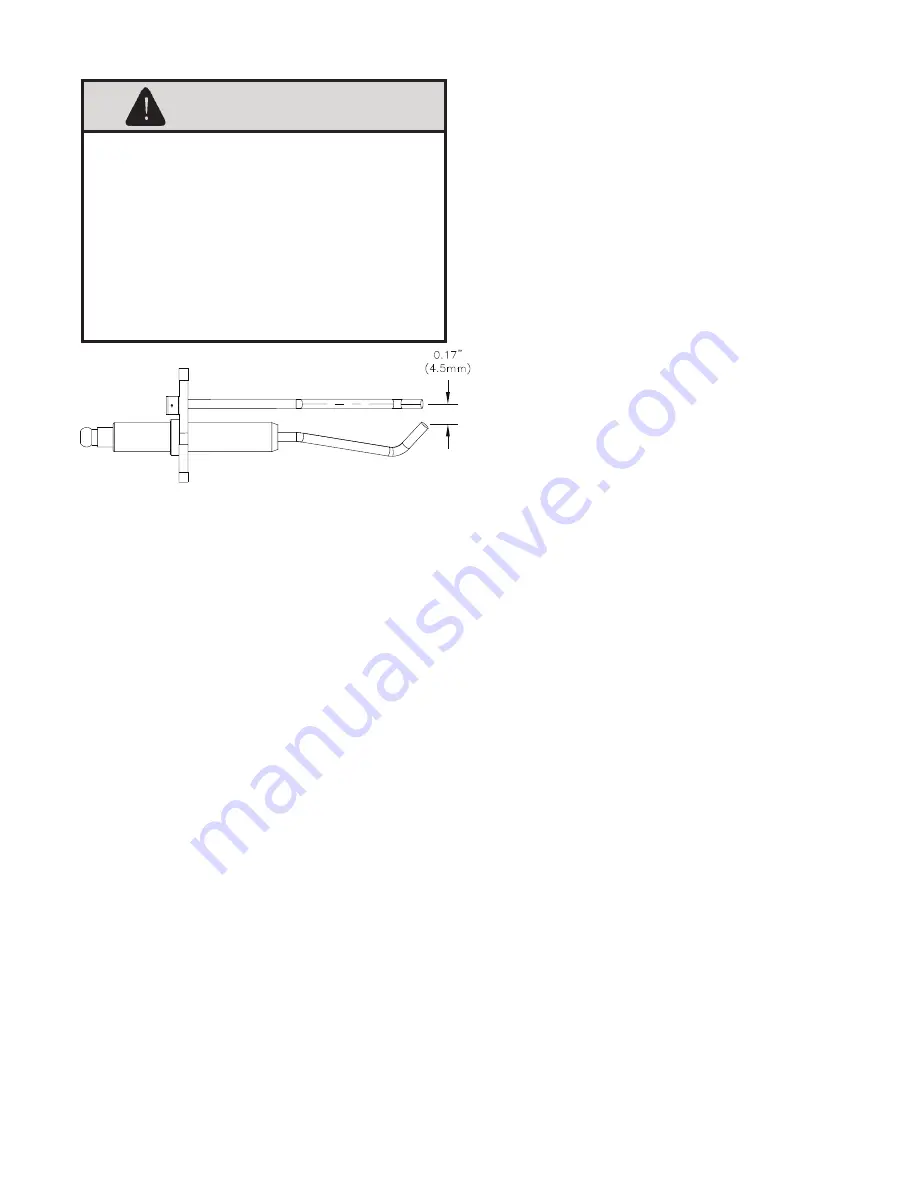
101
CAUTION / ATTENTION
Electrical Shock Hazard. Label all wires prior to
disconnection when servicing controls. Wiring
errors can cause improper and dangerous
operation. Verify proper operation after
servicing.
Au moment de l´entretien des commandes,
étiquetez tous les fils avant de les débrancher.
Les erreurs de câblage peuvent nuire au bon
fonctionnement et être dangereuses.
S´assurer que l´appareil fonctionne
adéquatement une fois k´entretien terminé.
acid or alkali products is prohibited. Do not use any
cleaning agents or solvents. If insulation disc has signs
of damage, it must be replaced.
8. Inspect the condensate trap
to verify it is open
and free from debris. Inspect condensate line integrity
between boiler and condensate neutralizer (if used),
condensate neutralizer and the drain. Clean/repair if
needed.
If the condensate neutralizer is used, check pH before
and after the neutralizer to determine neutralizing
effectiveness. Replace limestone chips and clean out
the neutralizer if needed.
9. Inspect the flue temperature sensor cap
to verify
that it is free from leakage and deterioration. Replace
if needed.
10. Inspect vent connections and vent connector
to
heat exchanger seals to verify that they are free from
leakage and deterioration. Repair as needed. Follow all
instructions in Section IV “Venting” when reassembling
vent system.
11. Check for vent and air intake terminal
for
obstructions and clean as necessary. Check rodent
screens in vent and air intake terminations to verify
they are clean and free of debris.
12. Reinstall the burner/blower/gas valve assembly
and secure with M6X1 hex flange nuts.
13. Reconnect any wiring
which has been disconnected.
14. Verify
that the system pH is between 7.5 and 9.5.
15. Inspect the heating system
and correct any other
deficiencies prior to restarting the boiler.
16. Follow Section IX
“System Start-up” before leaving
installation.
17. Perform the combustion test
outlined in Section
IX “System Start-up”.
D. Recommended Heating System Water
Treatment Products:
1. System Cleaning and Conditioning:
a. The following heating system water treatment
products are recommended for an initial existing
heating system sludge removal, initial boiler
cleaning from copper dust, flux residue and any
boiler debris and for preventive treatment as
corrosion/scale inhibitors:
i.
Fernox™ Restorer (universal cleaner, sludge
remover, scale remover, flux residue/debris
remover, corrosion inhibitor)
ii.
Fernox™ Protector (Alphi 11, CH#, Copal)
(sludge remover, corrosion inhibitor)
Follow manufacturer application procedure
for proper heating system/boiler cleaning and
preventive treatment.
Figure 39: Igniter Electrode Gap
3. Remove the igniter assembly and flame sensor
and inspect them for oxide deposits. Clean the oxide
deposits from the igniter electrodes and flame sensor
rod with steel wool. Do not use sandpaper for the
cleaning. Inspect the ceramic insulators for cracks
and replace the igniter assembly and/or flame sensor
if necessary. Check the igniter electrode spacing gap.
Refer to Figure 39 “Igniter Electrode Gap” for details.
4. To gain access to boiler burner and combustion
chamber,
first disconnect and remove gas inlet piping
from gas valve. Then, remove six M6X1 hex flange
nuts and take out the burner/blower/gas valve assembly
from the boiler. To prevent stud breakage, apply a
generous amount of good quality penetrating oil to
nuts and let soak in prior to attempting nut removal.
5. Inspect the assembly
for lint and dust presence.
If significant lint and dust accumulations are found,
disassemble the blower/gas valve assembly to expose
the swirl plate and blower inlet. For parts identification,
refer to Section XIII “Repair Parts”. Vacuum these
parts as required, being careful not to damage the vanes
on the swirl plate.
6. Vacuum any dust or lint
from the burner if present.
If the burner shows any visual deterioration or corrosion
signs, replace it immediately. Inspect the burner gasket
and replace if necessary.
7. Inspect the heat exchanger combustion
chamber,
clean and vacuum any debris found on
the surfaces. If required, brush the coils of the heat
exchanger using a non-abrasive, non-metal bristle
brush. Any cleaning of the combustion chamber with
XI. Service and Maintenance
(continued)
Содержание Phantom-X PHNTM210
Страница 7: ...7 Figure 1B Model PHNTM285 I Product Description Specifications and Dimensional Data continued...
Страница 52: ...52 VIII Electrical continued...
Страница 53: ...53 VIII Electrical continued Figure 26 Wiring Connections Diagram...
Страница 54: ...54 VIII Electrical continued Figure 27 Ladder Diagram...
Страница 59: ...59 Figure 29B Boiler to Boiler Communication with Crown Zone Panel PN 3501505 VIII Electrical continued...
Страница 109: ...109 XIII Repair Parts 1L 1K 1J 1E 1C 1D 1B 1L 1J 1A 1M 1F 1C 1D 1B 1L 1J 1A 1M 1F 1K 1G 1G 1K 1H 1G...
Страница 118: ...118...
Страница 119: ...119...