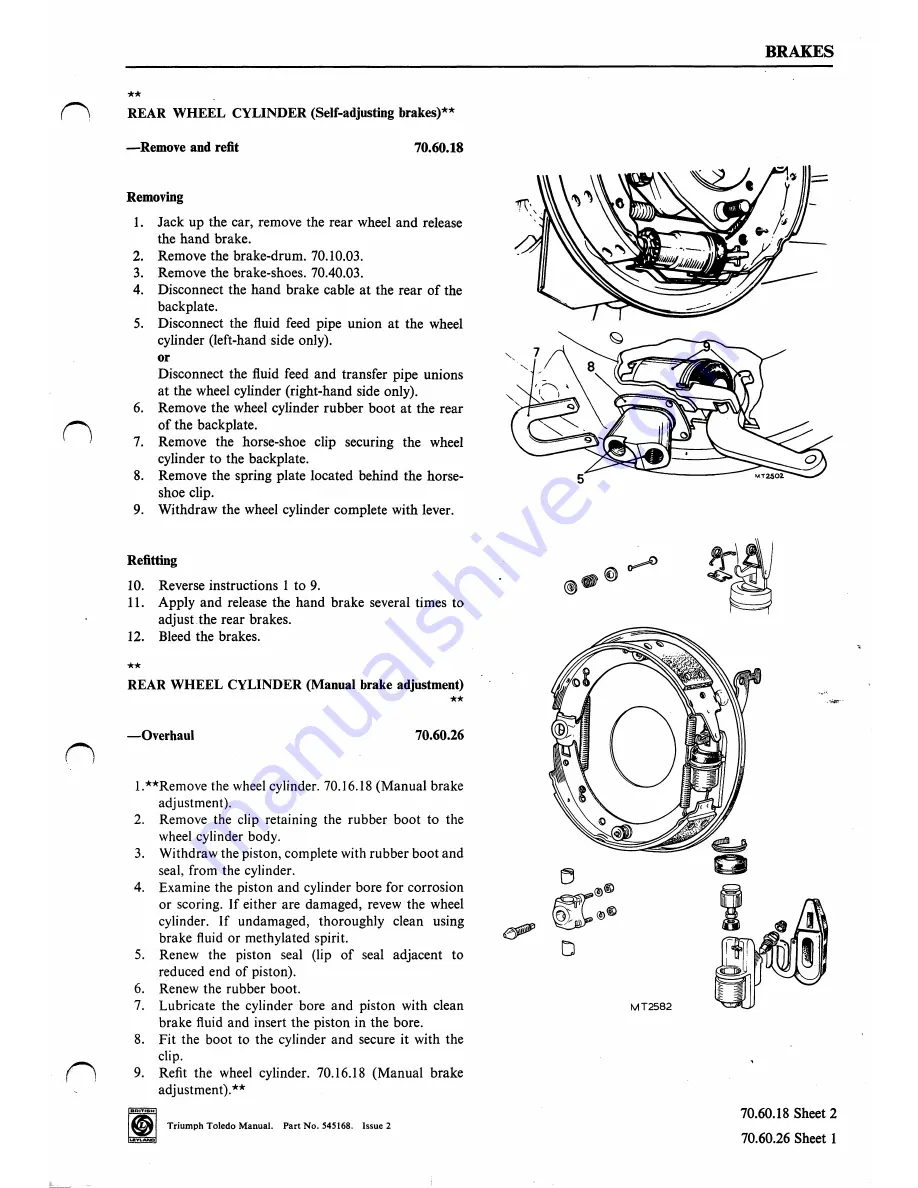
BRAKES
**
f ^ \
REAR WHEEL CYLINDER (Self-adjusting brakes)**
—Remove and refit
70.60.18
n
Removing
1. Jack up the car, remove the rear wheel and release
the hand brake.
2. Remove the brake-drum. 70.10.03.
3. Remove the brake-shoes. 70.40.03.
4. Disconnect the hand brake cable at the rear of the
backplate.
5. Disconnect the fluid feed pipe union at the wheel
cylinder (left-hand side only).
or
Disconnect the fluid feed and transfer pipe unions
at the wheel cylinder (right-hand side only).
6. Remove the wheel cylinder rubber boot at the rear
of the backplate.
7. Remove the horse-shoe clip securing the wheel
cylinder to the backplate.
8. Remove the spring plate located behind the horse
shoe clip.
9. Withdraw the wheel cylinder complete with lever.
Refitting
10. Reverse instructions 1 to 9.
11. Apply and release the hand brake several times to
adjust the rear brakes.
12. Bleed the brakes.
★ ★
REAR WHEEL CYLINDER (Manual brake adjustment)
*★
—Overhaul
70.60.26
1. **Remove the wheel cylinder. 70.16.18 (Manual brake
adjustment).
2. Remove the clip retaining the rubber boot to the
wheel cylinder body.
3. Withdraw the piston, complete with rubber boot and
seal, from the cylinder.
4. Examine the piston and cylinder bore for corrosion
or scoring. If either are damaged, revew the wheel
cylinder. If undamaged, thoroughly clean using
brake fluid or methylated spirit.
5. Renew the piston seal (lip of seal adjacent to
reduced end of piston).
6. Renew the rubber boot.
7. Lubricate the cylinder bore and piston with clean
brake fluid and insert the piston in the bore.
8. Fit the boot to the cylinder and secure it with the
clip.
9. Refit the wheel cylinder. 70.16.18 (Manual brake
adjustment).**
Triumph Toledo Manual.
Part N o. 545168. Issue 2
70.60.18 Sheet 2
70.60.26 Sheet 1
Содержание Triumph Toledo
Страница 8: ......
Страница 12: ...GENERAL SPECIFICATION DATA W 04 4 Triumph Toledo Manual Part N o 545168 Issue MTO 3 6 4 ...
Страница 113: ...J V ...
Страница 125: ...SYNCHROMESH GEARBOX Section Through Gearbox Assembly ...
Страница 182: ...n n n ...
Страница 236: ...BODY n n Triumph Toledo Manual Part No 545168 Issue 1 76 10 01 Sheet 3 ...
Страница 278: ...WINDSCREEN WIPERS AND WASHERS ...
Страница 283: ...WIRING DIAGRAM TOLEDO RIGHT HAND STEER 1970 TO 1972 MODELS ELECTRICAL L 094 ...
Страница 285: ...Triumph Toledo Manual Part No 545168 86 00 04 ...
Страница 291: ...ELECTRICAL O ...
Страница 329: ...INSTRUMENTS u 88 30 06 88 30 07 88 30 01 Triumph Toledo Manual Part No S4S168 Issue ...
Страница 337: ......
Страница 338: ...SERVICE TOOLS 550 Triumph Toledo Manual Part No 545168 Issue 2 99 00 02 ...
Страница 339: ...SERVICE TOOLS S 4221 A 5 S 4221 A 17 S 6118 1 Triumph Toledo Manual Part No 545168 Issue 1 99 00 03 ...