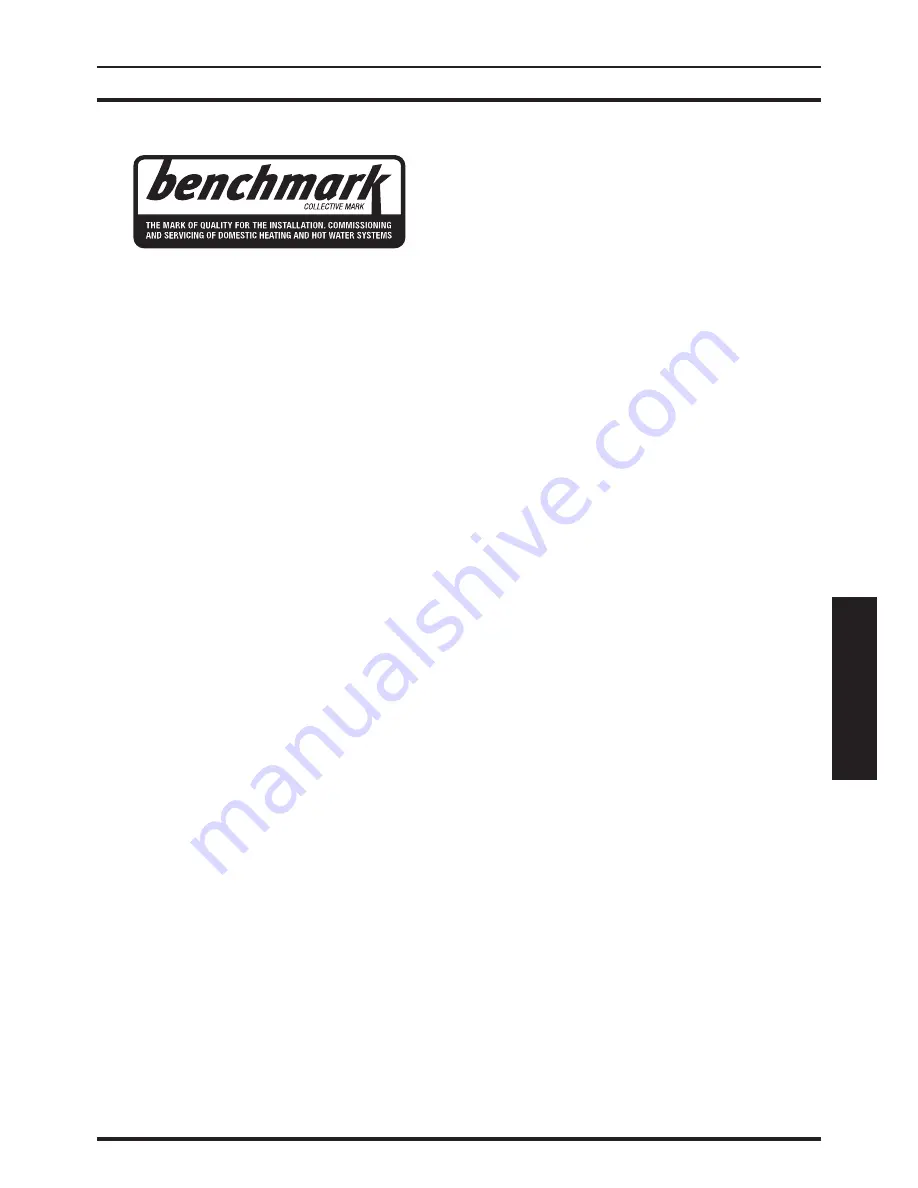
- 21 -
INST
ALLA
TION
- 21 -
INST
ALLA
TION
GENERAL REQUIREMENTS
5
GENERAL REQUIREMENTS
Benchmark places responsibilities on
both manufacturers and installers. The
purpose is to ensure that customers are
provided with the correct equipment for
their needs, that it is installed, commis-
sioned and serviced in accordance with
the manufacturer’s instructions by com-
petent persons and that it meets the re-
quirements of the appropriate Building
Regulations. The Benchmark Checklist
can be used to demonstrate compliance
with Building Regulations and should be
provided to the customer for future refer-
ence.
Installers are required to carry out installa-
tion, commissioning and servicing work in
accordance with the Benchmark Code of
Practice which is available from the Heat-
ing and Hotwater Industry Council who
manage and promote the Scheme. Visit
www.centralheating.co.uk for more infor-
mation.
Our Company supports the Benchmark in-
itiative. The Benchmark Checklist is locat-
ed at the back of this manual and should
be completed by the Installing/Commis-
sioning Engineer and handed over to the
User for future reference by other visiting
Engineers. Also included is the Service In-
terval Record card that should be complet-
ed by the Service Engineer following the
annual service maintenance of the boiler
and system.
For Ireland (IE), it is necessary to complete
a “Declaration of Conformity” to indicate
compliance to I.S.813.2002.
This appliance must be installed by a com-
petent person in accordance with the Gas
Safety (installation & Use) Regulations.
5.1 Related documents
The installation of this appliance must be in
accordance with the relevant requirements
of the current Gas Safety (Installation & Use)
Regulations, the Local Building Regulations,
the current I.E.E. Wiring Regulations, the
Regulations and by-laws of the local water
undertaking, and in Scotland, in accordance
with the Building Standards (Scotland) Reg-
ulation. Health and safety document n° 635
”Electricity at work regs.”.
It should also be in accordance with the Brit-
ish Standard Codes of Practice:
In Ireland (IE). The installation must be car-
ried out by a Competent Person and installed
in accordance with the current edition of
I.S.813.2002 “Domestic Gas Installations” the
current Building Regulations and reference
should be made to the current ETCI rules for
electrical installations.
5.2 Location of appliance
The appliance may be installed in any room
or internal space, although particular attention
is drawn to the requirements of the current
I.E.E. Wiring Regulations, and in Scotland,
the electrical provisions of the Building Regu-
lations applicable in Scotland, with respect to
the installation of the combined appliance in a
room containing a bath or shower.
For Ireland (IE), reference should be made
to the current edition of I.S.813.2002 and the
current ETCI rules for electrical installations.
Where a room-sealed appliance is in-