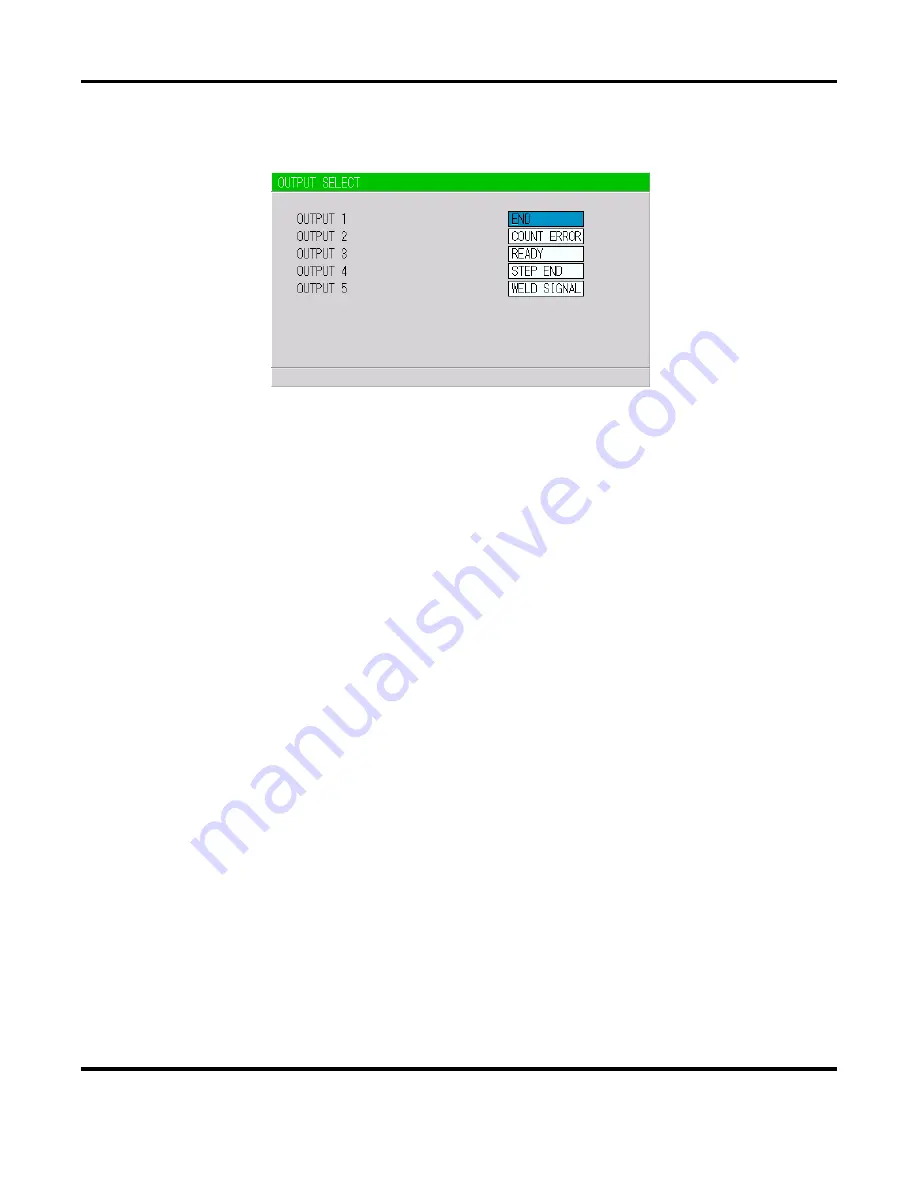
CHAPTER 3: USING PROGRAMMING FUNCTIONS
IS-300CA INVERTER POWER SUPPLY
990-418
3-21
7. OUTPUT SELECT Screen
Sets the output signals OUT1 (Pin 28) to OUT5 (Pin 32) of the external output signals.
NOTE:
This screen shows initial settings.
Pressing the
+ON
key switches the signal in the following order (in the reverse direction when
pressing -
OFF
key):
END
(end signal)
COUNT ERROR
(count error signal)
READY
(ready signal)
STEP END
(step end signal)
WELD SIGNAL
(welding timing signal)
GOOD
(normal signal)
COUNT UP
(count up signal)
OUT I
(OUT I timing output)
OUT II
(OUT II timing output)
For output timings of
END
,
WELD SIGNAL
,
GOOD
,
OUT I
, and
OUT II
, see the Timing Chart.
Содержание IS-300CA
Страница 1: ...990 418 REV D INVERTER POWER SUPPLY IS 300CA OPERATION MANUAL...
Страница 26: ......
Страница 30: ......
Страница 92: ......
Страница 104: ...APPENDIX A TECHNICAL SPECIFICATIONS IS 300CA INVERTER POWER SUPPLY A 4 990 418 Duty Cycles...
Страница 162: ...APPENDIX E EtherNet IPTM COMMUNICATIONS IS 300CR INVERTER POWER SUPPLY E 2 990 418 System Hardware Overview...
Страница 208: ...AMADA WELD TECH INC 1820 South Myrtle Ave Monrovia CA 91016 U S A TEL 1 626 303 5676 FAX 1 626 358 8048...