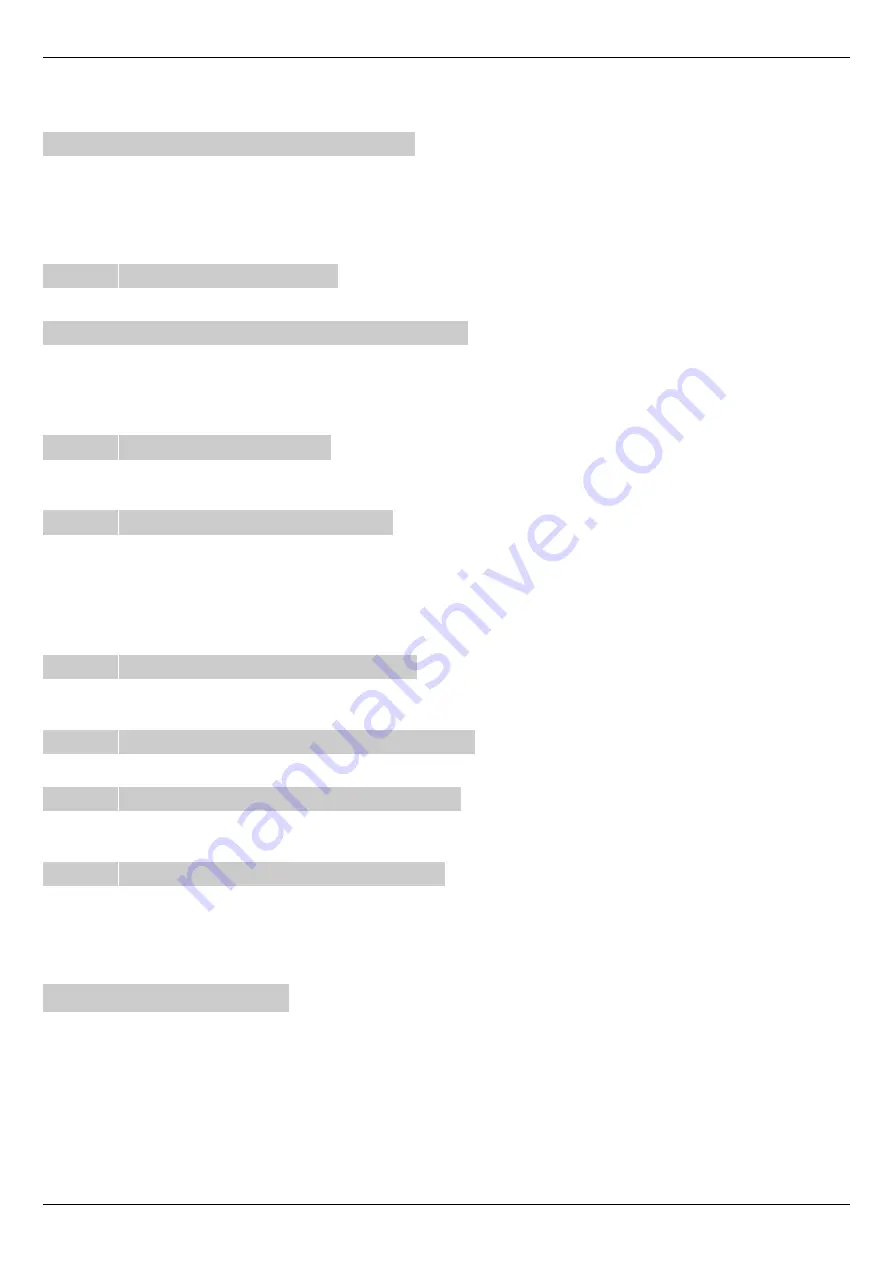
Diagnostics
Instruction manual 91/121 V6.3
•
Enter the optional motor parameters or perform the Autotune procedure as indicated in paragraph ”Autotune for the syn-
chronization of the transducer“ on page 54.
6.5.9 Motor Overload Limit activated
This message indicates that the automatic current limiter has been activated in the motor. At this time the motor can only absorb the
current set in the parameter ”Continuous service Current“ instead of the normal one set to ”Maximum Current”. This limitation occurs
when the function is activated in the ”Autom. Curr. Lim.“ menu (see page 49) and after the motor is overloaded for a time longer than
set in ”Overload Time“ (see page 49).
For more information about this message and its settings, see paragraph ”Motor Overload Function“ on page 66.
6.5.10 Overrun Control Loop
If this message appears, the drive must be returned to the ALTER for a check.
6.5.11 Resolver pole not comp with motor
This message can appear after giving the drive command to the drive (DEN=on) and indicates that the number of resolver pole set in
the parameter “Quick Setup → Motor Parameters → Resolver Pole” is not compatible with the number of motor poles set in the para -
meter “Quick Setup → Motor Parameters → Motor Pole”.
Check the motor plate and the manufacturer’s technical data.
6.5.12 Tachogenerator fault.
This message may appear during autotune function (see page 54) if there are problems with the signals received by the speed trans-
ducer “tachogenerator brushless” or “tachogenerator 10V”. Check the electrical connections.
6.5.13 Warning!!! Motor overtemp.
This message appears if the motor is overheated and if the drive block is enabled in case of motor over-temperature; When the mes-
sage appears it means that the PTC probe installed in the motor has just taken, when the time set in the ”Drive FLT delay“ menu has
elapsed (see page 49), the drive will go in bulk. motor temperature control shall be carried out using the PTC probe to be integrated
into the motor under construction; It must be like a closed contact when the temperature range is correct and must be like an open
contact when the maximum motor temperature is exceeded (see section ”Motor temperature on page ”62). To disable this alarm or
change some signalling modes you can use the ”Motor overtemp“ menu (see page 49).
6.5.14 Wrong hall sect for this motor
This message may appear during the autotune function (see page 54) if the signals received from the motor Hall sectors are not com-
patible with the number of motor poles set in the relevant parameter.
6.5.15 Wrong pole setup motor or resolver
This message may appear during the autotune function (see page 54) if the setting of the motor poles or resolver poles is not right.
6.5.16 Wrong pole setup or Encoder PPR
This message may appear during the autotune function (see page 54) if the setting of the motor poles or that of the Encoder PPR is not
right.
6.5.17 Wrong Pole setup or lack track Z
This message may appear during the Autotune procedure (see paragraph ”Autotune for the synchronization of the transducer“ on page
54), and indicates that there is some incorrect setting in one or more of the following parameters:
•
Pole motor (see paragraph ”Motor pole“ on page 37).
•
Lack of track Z from the TTL encoder or SinCos.
6.6 Diagnostic menu
On the LCD display there is a menu group called “Diagnostic” which leads to together some important parameters that can be dis -
played in case of need.
For more information please refer to the appropriate paragraph ”Diagnostic“ from page 44 with the full list of parameters.
76
Alter Elettronica s.r.l.