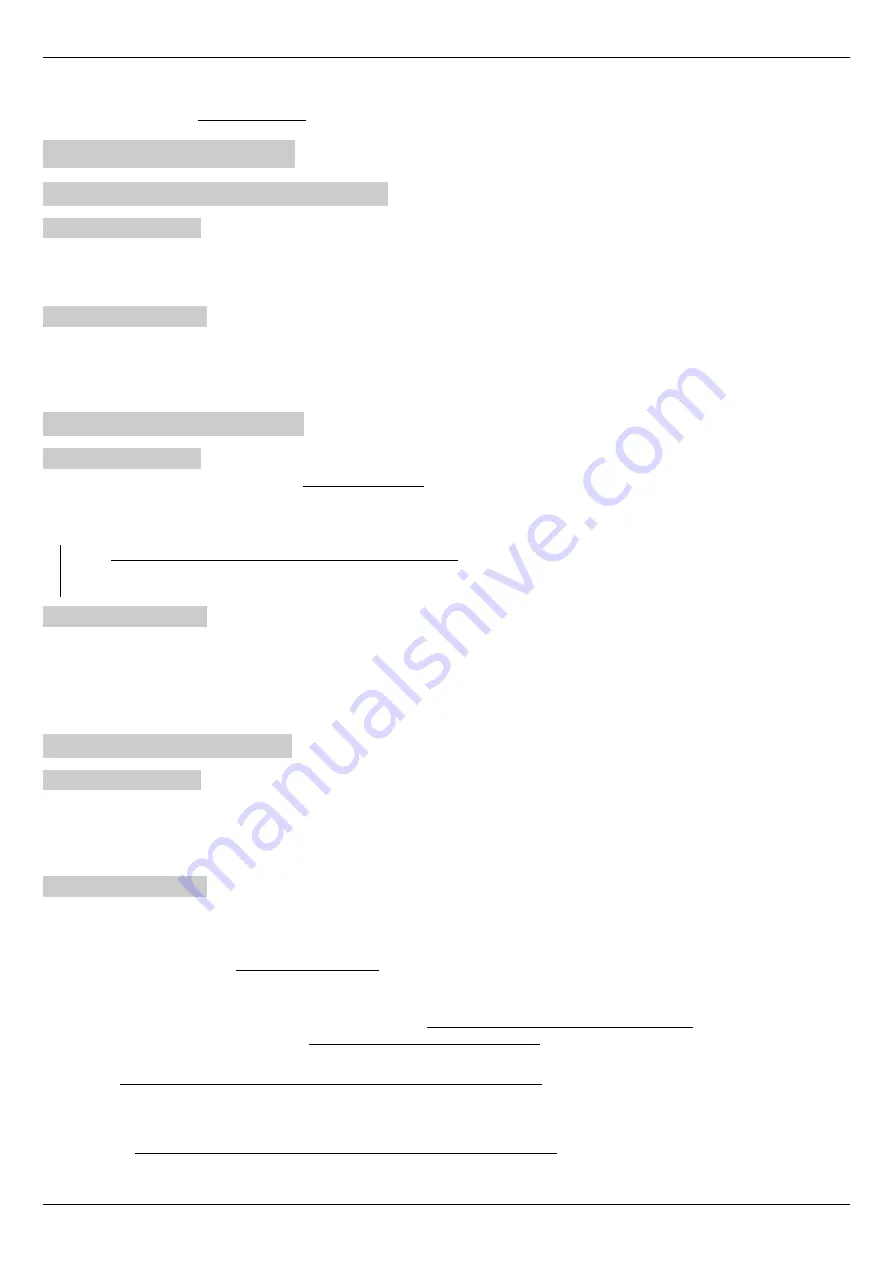
Commissioning
Instruction manual 91/121 V6.3
5. When the motor stops, the above menu will automatically become DISABLED.
6. At this point the calibration is over. You don't need to save the parameters.
5.6 Special functions
5.6.1 Zero speed motor signalling
5.6.1.1 Generality
This function is used to signal on a selectable digital output (usually matched to the DO1 output), when the motor is still. If the motor
speed is less than 2 RPM for a time greater than 500 mSec the signaling occurs and the associated output changes logical status and
leads to +24V or 0V if the inversion of sign is activated (see ”Dig.Op. X Sign“ on page 44).
5.6.1.2 Calibration
This function does not need calibration. To use it you have to go to the configuration menu "I/O Configure → Digital Outputs" and
from the selection menu of the source of the desired output go to select the item "Zero Speed" (see paragraph ” Dig.Op. X source“ on
page 44). If you want to change the logical state of the output when the motor is still, you must enable (or disable) the logical reversal
setting of the output (see paragraph ”Dig.Op. X Sign“ on page 44).
5.6.2 Motor brake control
5.6.2.1 Generality
This function is used to control the release of the parking brake of the motor using any digital output (usually combined with the DO2
output). If the drive is disabled and the motor is stationary (following the same conditions as in the previous paragraph) the signaling
occurs and the associated output changes logical status and leads to 0V or +24V if the inversion of sign is activated (see ”Dig.Op. X
Sign“ on page 44).
NOTE:
This
output
is not used to control an “emergency brake”
but a “parking brake”. For this reason, the brake is controlled
only when the motor is stationary. A digital output associated with the "Drive Running" source may be used to activate an emer-
gency brake (see section ”Dig.Op. X source“ on page 44).
5.6.2.2 Calibration
This function does not need calibration. To use it you have to go to the configuration menu "I/O Configure → Digital Outputs" and
from the selection menu of the source of the desired output go to select the item "Motor Brake" (see paragraph ” Dig.Op. X source“ on
page 44). If you want to change the logical state of the brake control output, you must insert (or disconnect) the logical reversal setting
of the output (see paragraph ”Dig.Op. X Sign“ on page 44).
Normally when the motor brake is to be inserted, the output goes to 0V, so it removes power to the brake coil.
5.6.3 Motor temperature
5.6.3.1 Generality
This function is used to signal on a selectable digital output or to block the drive, when the motor has exceeded its maximum operat-
ing temperature, connecting a PTC probe internally mounted to the appropriate connectors (see paragraph ”Connector X3“ on page
14). This probe must have a low resistance (some ohms) when the motor temperature is in the correct range of use; on the other hand,
if it exceeds its maximum temperature, the probe must increase the resistance (greater than 3Kohm).
5.6.3.2 Calibration
1. First of all you have to decide whether the motor over-temperature signal must be managed by the CNC or the drive and set
the parameter in the “Advanced Setup → Aux Function → Motor Overtemp → Signal Mode” menu in one of the following
ways:
◦
DIG.OUT ONLY: The drive does not
stop
, but only signals the intervention of the PTC on the digital output. It must be
the CNC or PLC that stops the motor when it considers it possible.
◦
DRIVE FAULT: The drive reports PTC intervention on the digital output and with a message on the display (see mes -
sage ”Warning!!! Motor overtemp.“ on page 76). If the CNC or PLC does not stop the motor within the time set in the
“Drive FLT delay” parameter, the drive locks and disables the motor, signaling the alarm ”Motor Overtemperature“ and
take the digital output "DOK" to the logical level "0”.
2. Set on which digital output you want to exit the over-temperature signal of the motor; In the configuration menu "I/O Con-
figure → Digital Outputs" and from the selection menu of the source of the desired output go to select the input "Motor
Temp." (see paragraph ”Dig.Op. X source“ on page 44). If you want to change the logical state of the temperature signaling
output, insert (or disconnect) the logical reversal setting of the output (see paragraph ”Dig.Op. X Sign“ on page 44). Nor-
mally when the motor is overheated, the associated output goes logically “0”.
62
Alter Elettronica s.r.l.