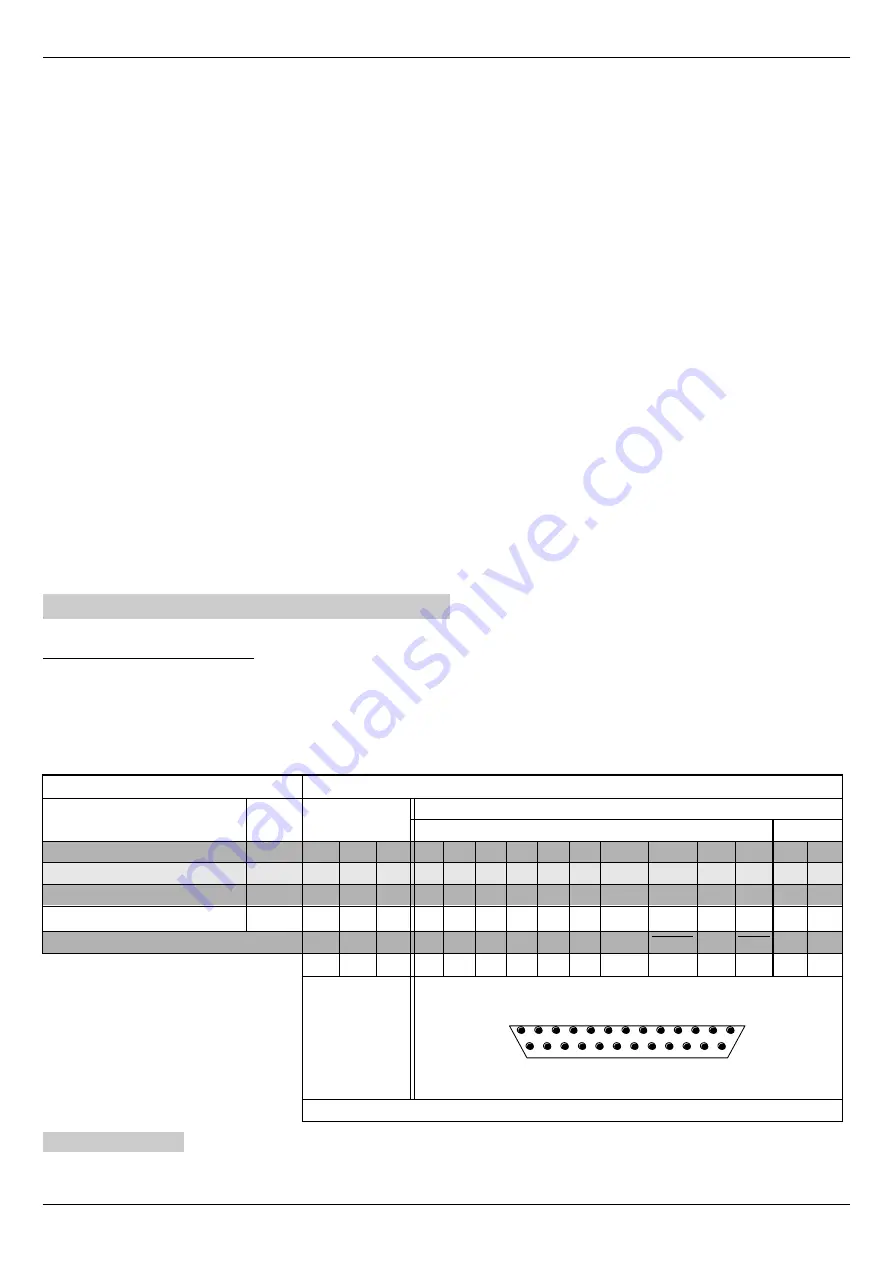
Commissioning
Instruction manual 91/121 V6.3
4. Navigate the drive menu to the “Quick setup → Motor Parameters → Feedback Type” parameter. Use the keys to change set-
ting and select “SIN-COS”. If you cannot select this transducer, see step 6 just ahead to check if the board is working prop -
erly.
5. Scroll through the menu to the parameter “Quick setup → Motor Parameters → Encoder Lines”. Set the number of sinus -
oids/turn as reported on the plate or technical data of the transducer.
6. Check if the card is compatible and if it has been recognised by moving to the menu “Diagnostic → Transduc. Board →
Transduc. Board for...." and verify that the word "SIN-COS" is present. If this does not occur, please contact the ALTER
Technical Office for some verifications.
7. Check the amplitude of incremental signals connected on the X14 connector to pins 3, 4, 6, 7 and the connection of the trans-
ducer’s electrical wires by moving to the “Diagnostic → Transduc Board → SinCos signal A and B" and verify that there is
"OK", otherwise perform these verifications:
◦
Written “LOW”: check that you've connected the cable from both sides. Check the cable and welding of wires on the
X14 connector at pins 3, 4, 6, 7.
◦
Written “HIGH”: check the cable and welding of wires on the X14 connector at pins 3, 4, 6, 7 that are not short-circuited
with other signals.
8. Check the amplitude of the absolute signals connected on the X14 connector to pins 19, 20, 21, 22 and the connection of the
transducer’s electrical wires by moving to the “Diagnostic → Transduc Board → SinCos signal C and D" and verify that
there is "OK", otherwise perform these verifications:
◦
Written “LOW”: check that you've connected the cable from both sides. Check the cable and welding of wires on the
X14 connector at pins 19, 20, 21, 22.
◦
Written “HIGH”: check the cable and welding of wires on the X14 connector at pins 19, 20, 21, 22 that are not short-cir-
cuited with other signals.
9. If all previous verifications are positive, autotune of motor parameters can be performed as explained in paragraph ”Autotune
for the synchronization of the transducer“ on page 54.
10. At the end of the autotune procedure, the parameters must be stored in order to complete the commissioning of the transducer
card.
5.5.3 01/327 board for EnDat transducer
This card makes it possible to connect an EnDat encoder to the X14 connector and to use it to control the motor.
Encoders compatible with this card must have the following features:
•
Interface
: EnDat 2.1 or EnDat 2.2.
•
Order code
: EnDat01 or EnDat02 (with incremental 1Vpp signals).
•
Incremental pulses/turn signals:
less than 16384 PPRs.
•
Type of encoder
: single revolution absolute rotary.
Example of connection of some motor models to the drive:
ENCODER MODEL
MOTOR SIDE CONNECTIONS
TYPE
POLES
MOTOR
CABLE
TRANSDUCER CABLE
SINUSOIDAL ENCODER
PTC
Heidenhain ECN 1313
U
V
W
7
10 15 16 12 13
8
9
14
17
5
6
Heidenhain EQN 1125
U
V
W
10
7
1
2
11
12
5
14
3
13
9
8
RCV UL5 and UL7
8
2
1
3
8
7
3
4
5
6
9
10
11
12 PTC PTC
Signals:
U
V
W +5V ØV A+ A- B+ B-
CLOCK CLOCK DATA DATA
PTC PTC
A
B
C
1
2
3
4
6
7
10
12
15
23
25
13
TERMINALS
Connector X14( pin)
25
14
13
1
WELDING SIDE VIEW
drive SIDE CONNECTIONS
5.5.3.1 Settings
Follow these points for proper commissioning of the transducer card:
58
Alter Elettronica s.r.l.