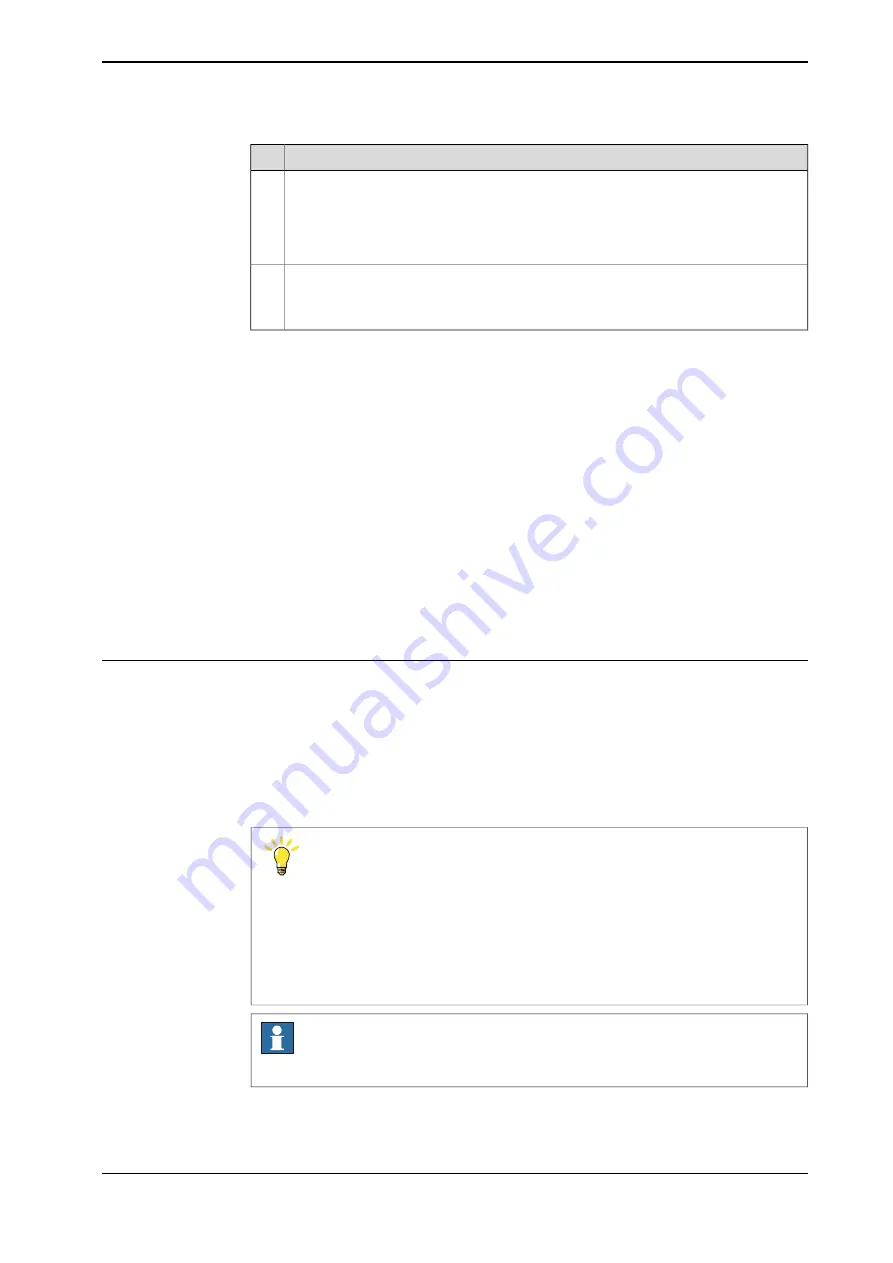
Action
If relevant, configure Safe I/O.
3
As general recommendation, two channel signals can be defined as separate single
channel signals that are combined by PreLogic in SafeMove.
Ensure correct safety checksum by using
Controller
->
Configuration
->
Vendor
Tool
. The generated checksum is then used in the SafeMove configuration.
Set device names on devices with RobotStudio ScanTool.
4
Modify the devices names if necessary, see
Standard network IP settings on page 51
Other tools can be used if desired.
The PROFINET controllers in FlexLoader function packages normally uses DCP
(Discovery Configuration Protocol), i.e. that they will configure devices when they
found them.
The key property for this method is the device name (same as station name). The
controller is told which devices to handle and communicate with and which device
names they have. With this information, the controller finds the actual devices with
the right names on the network and automatically assigns IP addresses that are
pre-configured in the controller.
ABB CI502 I/O nodes will get its name depending on the switches/knobs on the
module, e.g.
ci502-pn-01
if knobs are put in positions 0 (x10H) and 1 (x01H). A
cold start is needed to read new name. Do not use knob positions 0 and 0, as these
are used for user-defined names.
Robot PROFINET devices such as I/O nodes and Pluto gateway will get their IP
address as warm start as defined in robot I/O configurator.
Internal cell network
The internal cell network connects the FlexLoader Vision PC, robot, safety devices,
I/O devices, frequency converters and other internal cell components to each other.
The PC network connection is named
Robot
on physical port
LAN
.
This network is the robots private network, and both robot
LAN2
and
LAN3
as well
as the service port are connected to this network. The robot is acting as PROFINET
master.
Tip
The FlexLoader Vision PC can only be connected to
LAN2
.
A separate network connection to the robot network can be made by using
LAN3
network isolation.
In this case, the service port remains internally connected to
LAN2
.
See robot documentation for further information.
Note
Do not connect the internal network directly to the factory network.
Continues on next page
Product manual - FlexLoader SC 6000
49
3HAC051768-001 Revision: D
© Copyright 2014-2020 ABB. All rights reserved.
3 Installation
3.7 Network connections
Continued
Содержание FlexLoader SC 6000
Страница 1: ...ROBOTICS Product manual FlexLoader SC 6000 ...
Страница 8: ...This page is intentionally left blank ...
Страница 12: ...This page is intentionally left blank ...
Страница 78: ...This page is intentionally left blank ...
Страница 172: ...This page is intentionally left blank ...
Страница 174: ...This page is intentionally left blank ...
Страница 176: ...This page is intentionally left blank ...
Страница 178: ...This page is intentionally left blank ...
Страница 182: ...This page is intentionally left blank ...
Страница 184: ...This page is intentionally left blank ...
Страница 186: ...This page is intentionally left blank ...
Страница 192: ...This page is intentionally left blank ...
Страница 224: ...This page is intentionally left blank ...
Страница 283: ......