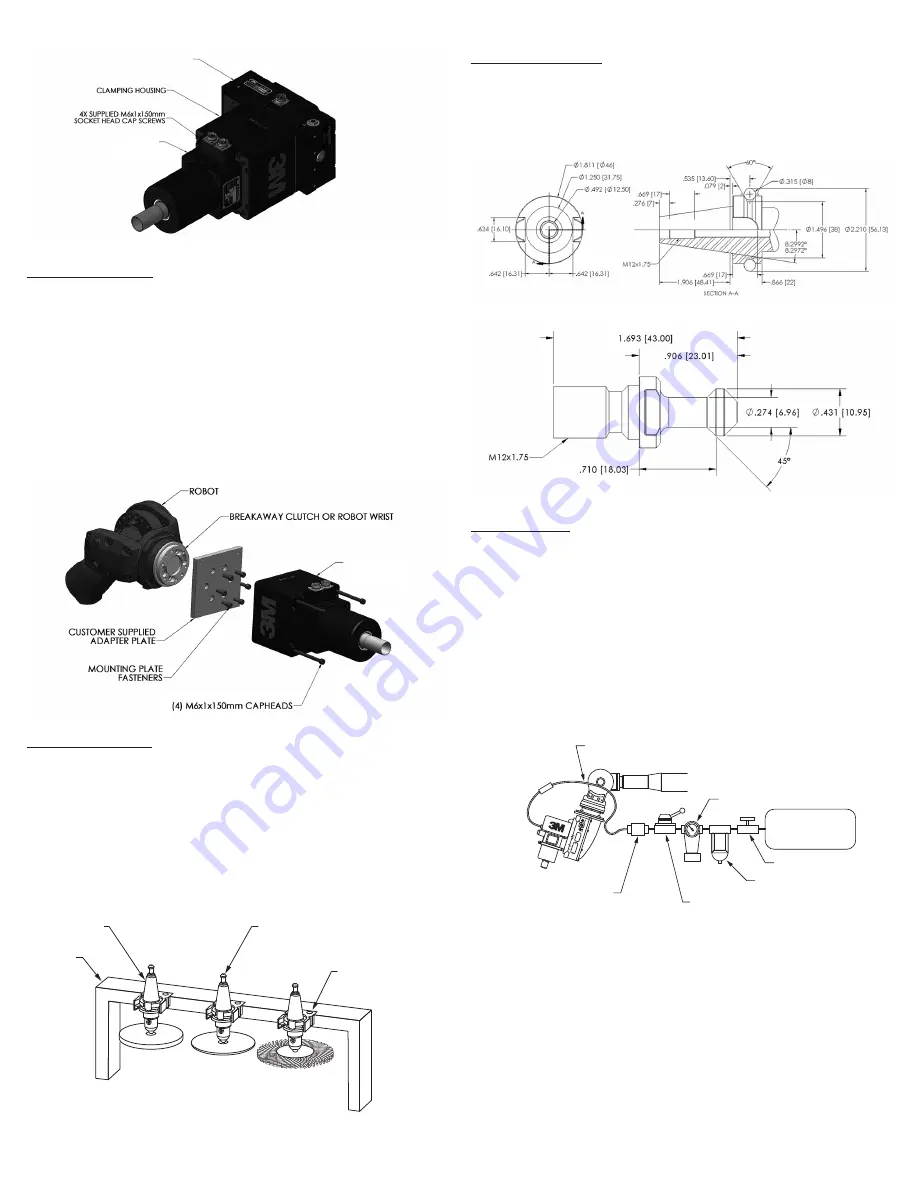
4
3M 06531
3M 06532
Figure 2. Spindle Motor Perpendicular-Axis Configuration
Mounting Directly to a Robot
For some processes compliance and force control are not required. The tools can be mounted
directly to the robot, in these cases, and the system can be operated in position mode. This
robotic system is equivalent to a 5-axis machining center with a very large work volume and
lower positional accuracy. Certain product types and processes are well suited for a Robotic
Machining Center (RMC). The tools can be attached to the Robot Mounting Flange using a
customer supplied Mounting Plate. For direct mounting it is recommended that a Breakaway
Clutch is installed. The Breakaway Clutch will help protect the motor in the event of a robot
crash. Loads on the motor shaft of over 300 lb (136 kg) radially and 150 (68 kg) axially will
damage the bearings.
To mount the tool, first attach the customer supplied Mounting Plate to the Robot Mounting
Flange or to the Breakaway Clutch, per the manufacturer’s specifications. Once the Mounting
Plate is secured, place the tool against the Mounting Plate and install four (4) M6x1x145mm
Socket Head Cap Screws. (See Figure 3.) Tighten the fasteners to the torque specified in the
Technical Specifications Section.
3M 06531
3M 06532
Figure 3. Spindle Motor Direct Mounting
Media and Tool Presentation
Media and tool presentation refers to how various discs, drill bits, router bits, etc. are
presented so that a robot may maneuver the motor into position to grasp the Toolholder
reliably. It is ultimately the user’s responsibility to provide a means to present the media and/
or tooling in an effective and repeatable way for a given application.
As shown in Figure 4, many types of media and tools may be accurately located in a Tool
Cradle. A robot can then be taught approach paths and docking locations to reliably bring the
motor down over the Toolholders and grasp them. The motor’s Collapsing Collet allows
0.015 in. (0.38 mm) diametrical clearance around the Toolholder when open. The Toolholder
must have a taper that mates to a Tapered Holder mounted in the Tool Cradle. The Tapered
Holder requires a slot to allow the Toolholder to pass through. This same method is applicable
to the motor’s design.
BT30 TOOLHOLDER
BT30 TOOLHOLDER GRIPPER
BT30 RETENTION KNOB
TOOL RACK
Printed Colors – Front:
Requester:
Marnie Cleveland
Creator:
deZinnia_25417
File Name:
Sample Media and Tooling Presentation Scheme.ai
Structure #:
Illustration
Date:
04/24/19
This artwork has been created as requested by 3M. 3M is responsible for the artwork
AS APPROVED and assumes full responsibility for its correctness.
Scale:
1 Inch
Figure 4. Sample Media and Tooling Presentation Scheme
BT30 Toolholder Specification
The 3M Model 06531 and 06532 motors are designed to grip a BT30 Toolholder. The BT30
Toolholder is a standard machine tool style and may be purchased from 3M (Part Number
06534, 5/8-11 X .48IN BT30 TOOLHOLDER HTC): The Customer can also make their own BT30
Toolholder to handle special media (See Figure 5 for Toolholder dimensions). The Toolholder
must be equipped with a Parlec (www.parlec.com) retention knob, part number 3003TRK, or
equivalent. Figure 6 shows the Parlec retention knob with the required dimensions.
Figure 5. STC-BT30 Toolholder Dimensions
Figure 6. BT30 Retention Knob
Pneumatic Connection
The Tool Changing function of the motor requires a dry, non-lubricated, filtered air supply,
with a minimum pressure of 90 psi (6.2 bar) and a maximum pressure of 100 psi (6.9 bar).
Failure to provide supply air to these specifications can degrade performance and will void any
warranty repairs concerning pneumatic components. If the supply air pressure is too low then
the unit will be unable to fully release the Toolholder. Exceeding the maximum air pressure
could result in permanent damage to the Tool Changing function. The pneumatic supply system
should be configured as shown in Figure 7. A manual or electrically operated valve may be
used to energize the Tool Changing function for Toolholder release, but the valve must exhaust
ALL line pressure when unenergized. An electrically operated pneumatic valve is normally
used in an automated workcell. 3M highly recommends the installation of a Pressure Switch
in the Supply Line to the Servo Motor. This switch should not allow the unit to start if there is
any pressure in the Supply Line. Pressure in the line will cause internal components to come
into contact. This will either cause the motor not to spin, or cause very high internal forces,
eventually friction welding components together.
Air Regulator/Pressure Gauge
1/4" (6mm) Polyurethane
Tubing
Manual or Electrically
Operated Valve
5µm Filter
Shut off Valve
90 psi minimum
(6.2 Bar)
Dry, Non-lubricated
Air Supply
Pressure Switch
Quick
Exhaust
Printed Colors – Front:
Requester:
Marnie Cleveland
Creator:
deZinnia_25417
File Name:
Pneumatic Connections.ai
Structure #:
Illustration
Date:
04/24/19
This artwork has been created as requested by 3M. 3M is responsible for the artwork
AS APPROVED and assumes full responsibility for its correctness.
Scale:
1 Inch
Figure 7. Pneumatic Connections
The motors are provided with 1/4 inch and 6 mm diameter tubing push-lock fittings for
installation in the R 1/8 (Metric) Collet Unclamp Port located on the top of the Clamping
Housing (See Figure 8). Remove the shipping plug and install the desired size push-lock fitting.
If another type of fitting is desired, unscrew the existing fitting and replace it with any fitting
having an R 1/8 (Metric) thread. Be sure to use a thread seal product and do not overtighten
the fitting. The Unclamp Supply Line to the device should be 1/4 inch or 6 mm diameter flexible
polyurethane tubing. The tubing should be routed to the device such that there are no kinks
and that there is plenty of slack to allow for manipulator motion. Before inserting the tubing
into the air fitting, open the Shut-Off Valve to blow out any contaminants which may be in the
Unclamp Supply Line. The tubing can now be pushed into the self-locking fitting located on the
Clamping Housing as shown in Figure 8. Charge the Unclamp Supply Line with compressed
air and verify that there are no air leaks and that there is a minimum of 90 PSI (6.2 bar) at the
Servo Motor. If a minimum air pressure cannot be achieved, then an auxiliary air compressor or
booster pump must be installed. NOTE: 3M highly recommends the use of flexible polyurethane
ACT