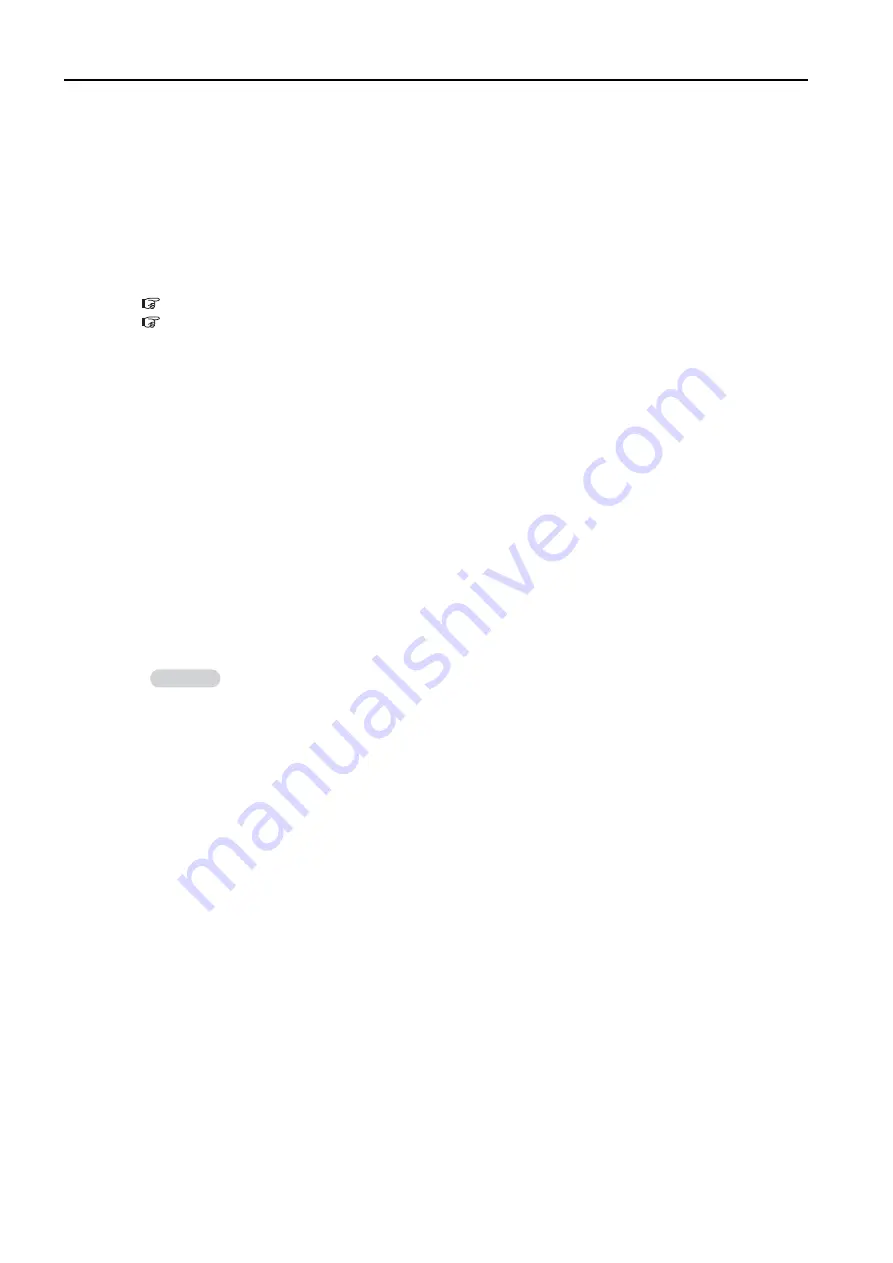
5.2 Absolute Encoders
5.2.6 Position Management Method for Each Machine Operation Type
5-36
Saving the Value of OL
48 before the Power Supply Is Turned
OFF
After the zero point is set, save the value of the OL
48 setting parameter (Zero Point Posi-
tion Offset in Machine Coordinate System) before you turn OFF the power supply to the
MP3000 so that the value will be written in OL
48 again the next time the power supply is
turned ON.
There are two methods to save the value of OL
48: from the MPE720 Parameters Tab
Page or from a ladder program to an M register.
Refer to the following sections for details on these methods.
•
Saving the Value of OL
48 from the MPE720 Parameters Tab Page
on page 5-29
•
Saving in M Registers from a Ladder Program
on page 5-31
Turning ON the Power after Setting the Origin in the Machine Coordi-
nate System
Bit 5 (Zero Point Return/Setting Completed) in the IW
0C monitor parameter changes to 0
(Zero point return/setting not completed) when the power supply to the MP3000 is turned OFF
and ON again or the communications are interrupted by turning the power supply to the slave
SERVOPACK OFF and ON again after the zero point has been set. Therefore, you must use the
following procedure to change bit 5 in IW
0C back to 1 (Zero point return/setting com-
pleted) after the power supply is turned back ON and communications are restored.
1.
Turn ON the power supply to the MP3000. Or, clear alarms to restart communications.
The saved offset is stored in OL
48.
2.
Check that communications are synchronized.
Check to make sure that bit 0 (Motion Operation Ready) in the IW
00 monitor parameter is 0
(Motion operation not ready) at this time.
3.
Set the OW
08 setting parameter (Motion Commands) to 9 to execute the ZSET
motion command.
Infinite-length Operation with Non-simple Absolute Infinite
Axis Position Management
If the conditions to perform simple absolute infinite axis position management cannot be satis-
fied, non-simple absolute infinite axis position management must be used to manage the posi-
tion with ladder programming in order to perform infinite-length operation.
If simple absolute infinite axis position management is not used, special ladder programming is
required for operation and for when the power supply to the system is turned ON.
The origin must also be set when the machine (system) first starts.
Parameter Settings
This section describes the parameter settings required for each axis when performing infinite-
length operation using non-simple absolute infinite axis position management.
This process is performed to set bit 5 in IW
0C to 1 (Zero point return/setting com-
pleted). This is not the same as the process to set the origin in the machine coordinate sys-
tem (i.e., the process to set OL
48).
Information
Summary of Contents for SVC
Page 34: ...2 6 4 Reference Output Timing 2 20 2 6 5 Precautions When Combining with Other Modules 2 21...
Page 383: ...5 2 Absolute Encoders 5 2 6 Position Management Method for Each Machine Operation Type 5 42...
Page 387: ...5 2 Absolute Encoders 5 2 6 Position Management Method for Each Machine Operation Type 5 46...