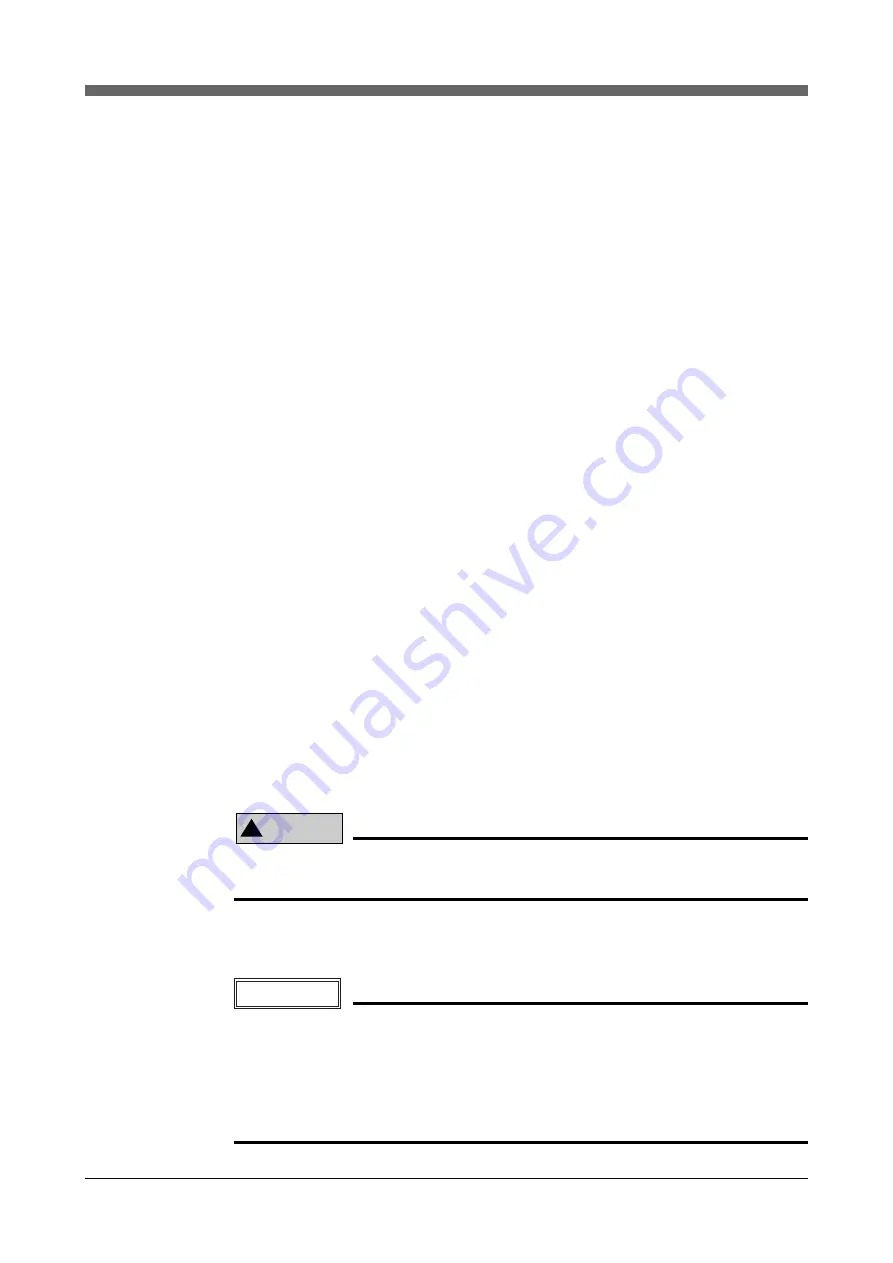
4-24
CHAPTER 4 Adjustment
3
Adjusting the R-axis machine reference
The adjustment method for the R-axis machine reference is as follows.
1) Prepare a hex wrench set.
2) Check that no one is inside the safeguard enclosure and then turn on the
controller.
3) Perform the absolute reset from outside the safeguard enclosure.
Refer to "3-3 Absolute reset procedures" for information about the absolute
reset method.
4) If any machine reference value displayed on the MPB is not in the range
between 40 and 60 (recommended range) after the absolute reset has been
completed, then proceed with the following adjustment procedure.
5) Place a sign indicating that the robot is being adjusted in order to keep others
from operating the controller or operation panel.
6) Turn off the controller and enter the safeguard enclosure.
7) Mark off the reference mark at the current origin position on the R-axis area
of the robot.
At this time, be careful not to touch the tool at the tip of the robot arm so that
the origin position does not shift.
8) Remove the cover.
9) Scribe a mark on the position of the R-axis origin sensor stay.
10) Using the hex wrench, loosen the two bolts securing the R-axis origin sensor
stay. (See Fig. 4-9.)
!
CAUTION
The bolts only need to be loosened, and do not need to be completely re-
moved.
11) Move the R-axis origin sensor stay in the following manner and then secure
it with the bolts.
NOTE
• When the machine reference is less than 40%, move the stay in direction
q
:
See Fig. 4-9.
• When the machine reference is more than 40%, move the stay in direction
w
:
See Fig. 4-9.
As an approximate guide, a 1.9mm movement equals to 100%.
Summary of Contents for YK-X Series
Page 1: ...User s Manual ENGLISH E YAMAHA SCARA ROBOT E35 Ver 1 08 YK XG YK X series ...
Page 2: ......
Page 6: ...MEMO ...
Page 10: ...MEMO ...
Page 12: ...MEMO ...
Page 30: ...MEMO ...
Page 36: ...MEMO ...
Page 46: ...3 10 CHAPTER 3 Installation Ground symbol M4 Ground terminal Fig 3 6 Ground terminal ...
Page 78: ...3 42 MEMO ...
Page 80: ...MEMO ...
Page 101: ...4 21 CHAPTER 4 Adjustment Cover Elongated hole Y axis origin sensor stay Bolt Fig 4 8 a ...
Page 102: ...4 22 CHAPTER 4 Adjustment Dog Hex nut Fig 4 8 b Bolt Y axis arm X axis arm Fig 4 8 c ...
Page 119: ...4 39 CHAPTER 4 Adjustment R End effector End effector Z Y X Fig 4 18 ...
Page 120: ...4 40 MEMO ...
Page 122: ...MEMO ...
Page 138: ...5 16 CHAPTER 5 Periodic Inspection M6 16 M5 16 X axis motor Base Fig 5 3 ...
Page 146: ...5 24 CHAPTER 5 Periodic Inspection M3 16 M4 18 X axis arm Fig 5 10 ...
Page 155: ...5 33 CHAPTER 5 Periodic Inspection O ring r M5 14 M6 16 R axis motor Fig 5 17 ...
Page 156: ...5 34 CHAPTER 5 Periodic Inspection M3 14 M3 16 O ring w Fig 5 18 ...
Page 161: ...CHAPTER 6 Increasing the robot operating speed 1 Increasing the robot operating speed 6 1 ...
Page 162: ...MEMO ...
Page 168: ...6 6 MEMO ...
Page 170: ...MEMO ...
Page 177: ...MEMO ...