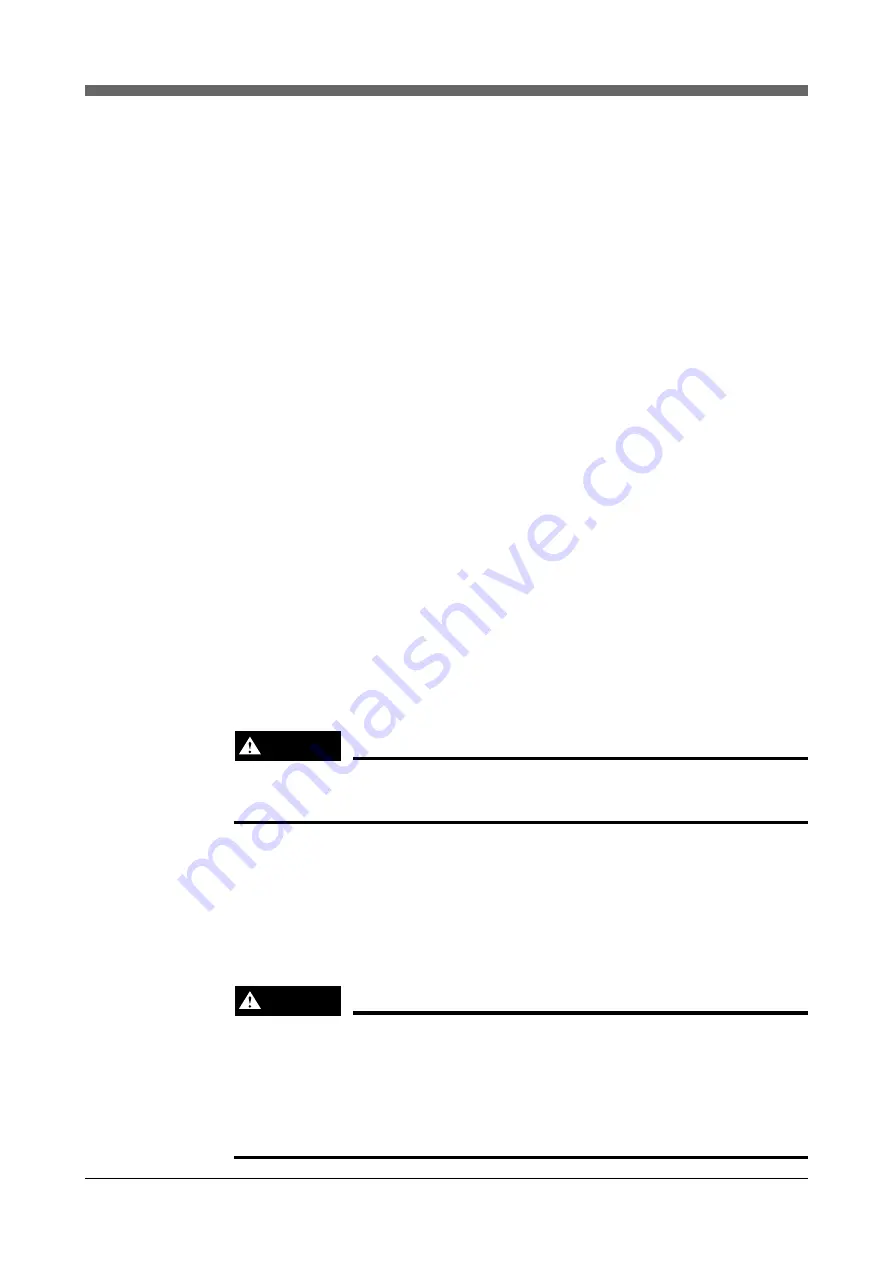
1-9
CHAPTER 1 Using the Robot Safely
4
Robot Safety Functions
(1) Overload detection
This function detects an overload applied to the motor and shuts off the servo
power. If an overload error occurs, take the following measures.
1. Insert a timer in the program.
2. Reduce the acceleration coefficient.
(2) Overheat detection
This function detects an abnormal temperature rise in the driver inside the
controller and shuts off the servo power. If an overheat error occurs, take the
following measures.
1. Insert a timer in the program.
2. Reduce the acceleration coefficient.
(3) Soft limits
Soft limits can be set on each axis to limit the working envelope in manual
operation after return-to-origin and during automatic operation.
Note: The working envelope is the area limited by soft limits.
(4) Mechanical stoppers
If the servo power is suddenly shut off during high-speed operation by emer-
gency stop or safety functions, these mechanical stoppers prevent the axis
from exceeding the movement range. The movement range is the area lim-
ited by mechanical stoppers.
• The movement ranges of the X-axis arm can be limited as needed by use of
mechanical stoppers.
• On the Y-axis arm, mechanical stoppers are fixed at both ends of the maxi-
mum movement range.
• The Z-axis has a mechanical stopper at the upper end and lower end.
• No mechanical stopper is provided on the R-axis.
WARNING
Axis movement will not stop immediately after the servo power supply is shut
off by emergency stop or other safety functions.
(5) Z-axis (vertical axis) brake
An electromagnetic brake is installed on the Z-axis to prevent the Z-axis
from sliding down when servo power is turned off. This brake is working
when the controller is off or the Z-axis servo power is off even when the
controller is on. The Z-axis brake can be released by means of the program-
ming unit or by a command in the program when the controller is on.
WARNING
The Z-axis will slide down when the Z-axis brake is released, creating a haz-
ardous situation.
• Press the emergency stop button and prop the Z-axis with a support stand
before releasing the brake.
• Use caution not to let your body get caught between the Z-axis and installa-
tion base when releasing the brake to perform direct teach.
Summary of Contents for YK-X Series
Page 1: ...User s Manual ENGLISH E YAMAHA SCARA ROBOT E35 Ver 1 08 YK XG YK X series ...
Page 2: ......
Page 6: ...MEMO ...
Page 10: ...MEMO ...
Page 12: ...MEMO ...
Page 30: ...MEMO ...
Page 36: ...MEMO ...
Page 46: ...3 10 CHAPTER 3 Installation Ground symbol M4 Ground terminal Fig 3 6 Ground terminal ...
Page 78: ...3 42 MEMO ...
Page 80: ...MEMO ...
Page 101: ...4 21 CHAPTER 4 Adjustment Cover Elongated hole Y axis origin sensor stay Bolt Fig 4 8 a ...
Page 102: ...4 22 CHAPTER 4 Adjustment Dog Hex nut Fig 4 8 b Bolt Y axis arm X axis arm Fig 4 8 c ...
Page 119: ...4 39 CHAPTER 4 Adjustment R End effector End effector Z Y X Fig 4 18 ...
Page 120: ...4 40 MEMO ...
Page 122: ...MEMO ...
Page 138: ...5 16 CHAPTER 5 Periodic Inspection M6 16 M5 16 X axis motor Base Fig 5 3 ...
Page 146: ...5 24 CHAPTER 5 Periodic Inspection M3 16 M4 18 X axis arm Fig 5 10 ...
Page 155: ...5 33 CHAPTER 5 Periodic Inspection O ring r M5 14 M6 16 R axis motor Fig 5 17 ...
Page 156: ...5 34 CHAPTER 5 Periodic Inspection M3 14 M3 16 O ring w Fig 5 18 ...
Page 161: ...CHAPTER 6 Increasing the robot operating speed 1 Increasing the robot operating speed 6 1 ...
Page 162: ...MEMO ...
Page 168: ...6 6 MEMO ...
Page 170: ...MEMO ...
Page 177: ...MEMO ...